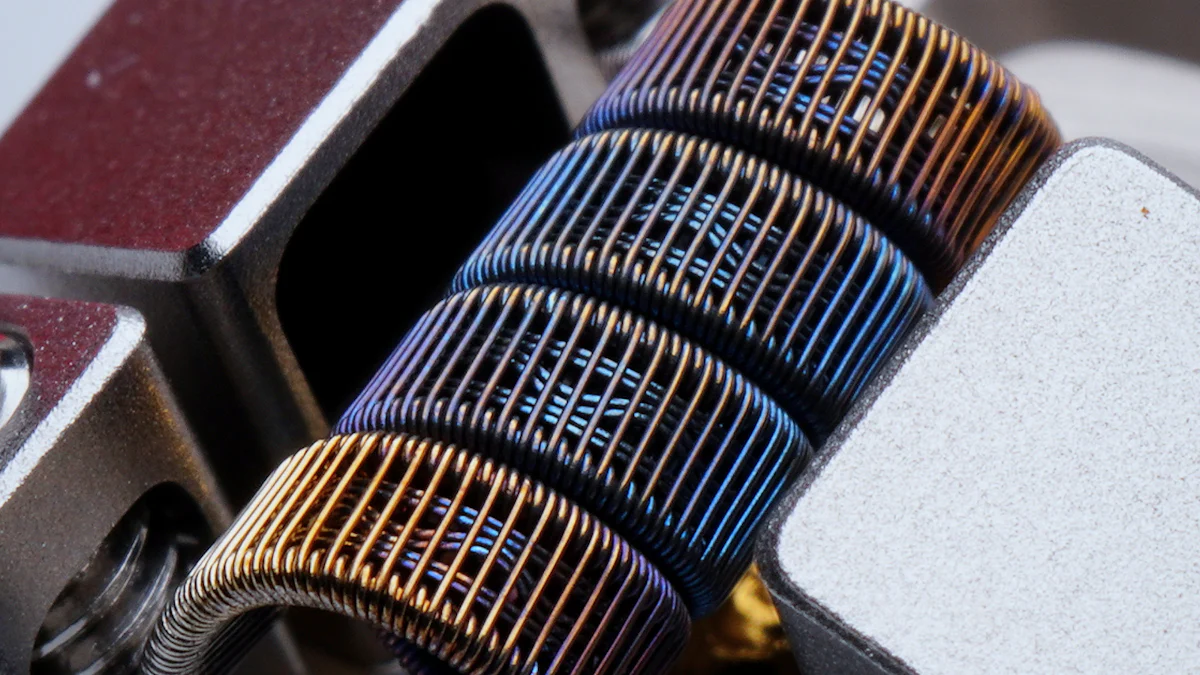
Forge carbon fiber has transformed industries by combining exceptional strength with a lightweight structure. Its unique composition offers a superior strength-to-weight ratio, making it indispensable in applications where performance and efficiency are critical. Unlike traditional materials, forge carbon fiber resists cracks, abrasion, and corrosion, ensuring durability under extreme conditions. The innovative manufacturing process allows for intricate designs, enabling engineers to create components with unmatched precision. This adaptability has made forge carbon fiber a cornerstone in advancing automotive and aerospace technologies, where reducing weight without sacrificing strength remains a top priority.
主要收获
Forged carbon fiber offers an exceptional strength-to-weight ratio, making it ideal for high-performance applications in automotive and aerospace industries.
The unique manufacturing process of forged carbon fiber allows for intricate designs and complex geometries, enhancing both functionality and aesthetic appeal.
This advanced material is highly durable, resisting cracks, corrosion, and extreme temperatures, which ensures reliability in demanding environments.
Forged carbon fiber is cost-effective due to reduced material waste and simplified production processes, leading to long-term savings in maintenance and operational costs.
Its lightweight nature contributes to improved fuel efficiency, making it a sustainable choice for industries focused on reducing carbon emissions.
The marbled texture of forged carbon fiber provides a modern aesthetic, appealing to luxury markets and enhancing the visual appeal of high-end products.
As industries evolve, forged carbon fiber continues to drive innovation, paving the way for advancements in robotics, renewable energy, and sustainable aviation.
What Is Forged Carbon Fiber?
Definition and Characteristics
Forged carbon fiber is an advanced composite material known for its exceptional strength, lightweight nature, and unique appearance. Unlike traditional carbon fiber, which features a woven pattern, forged carbon fiber exhibits a marbled texture. This distinct look results from its manufacturing process, where chopped carbon fibers are combined with resin and compressed under high heat and pressure. The material’s tightly bonded structure ensures superior mechanical properties, including high tensile strength, excellent crack resistance, and remarkable durability.
The strength-to-weight ratio of forged carbon fiber sets it apart from conventional materials like steel or aluminum. It provides the same or greater strength while being significantly lighter. This characteristic makes it ideal for industries that prioritize performance and efficiency, such as automotive and aerospace. Additionally, forged carbon fiber resists corrosion, abrasion, and extreme temperatures, ensuring reliability in demanding environments.
锻造碳纤维与传统碳纤维的区别
While both forged carbon fiber and traditional carbon fiber share a common base material, their manufacturing techniques and resulting properties differ significantly. Traditional carbon fiber involves weaving continuous strands into a fabric-like structure, which is then layered and infused with resin. This process creates a uniform, grid-like pattern and is well-suited for applications requiring consistent strength across large surfaces.
In contrast, forged carbon fiber uses short, randomly oriented carbon fibers mixed with resin. This method eliminates the need for weaving and allows the material to be molded into complex shapes. The random fiber orientation enhances its isotropic properties, meaning it exhibits consistent strength in all directions. This feature makes forged carbon fiber particularly advantageous for components with intricate geometries or areas subjected to multidirectional forces.
Another key distinction lies in aesthetics. Traditional carbon fiber’s woven appearance appeals to those seeking a sleek, uniform look, while forged carbon fiber’s marbled texture offers a modern, artistic alternative. This visual versatility has made it a popular choice for luxury automotive interiors and other high-end applications.
The Manufacturing Process of Forged Composites
The production of forged carbon fiber involves a highly specialized process designed to maximize its strength and adaptability. Manufacturers begin by chopping carbon fibers into small pieces, which are then mixed with a thermosetting resin. This mixture is placed into a mold shaped according to the desired component. Under extreme heat and pressure, the resin cures, binding the fibers together into a solid, compact structure.
This process eliminates the need for traditional weaving, allowing for greater design flexibility. Engineers can create components with complex geometries, such as curved or hollow shapes, without compromising structural integrity. The high-pressure compression ensures that the material remains dense and free of voids, enhancing its mechanical properties.
The efficiency of this manufacturing technique also contributes to cost-effectiveness. By reducing material waste and simplifying production steps, forged carbon fiber becomes a more accessible option for industries requiring high-performance materials. Its adaptability and streamlined production make it a revolutionary choice in carbon fiber manufacturing.
Key Benefits of Forged Carbon Fiber
卓越的强度重量比
Forged carbon fiber stands out for its exceptional strength-to-weight ratio, making it a preferred material in industries where performance and efficiency are critical. This advanced composite material provides superior strength while being significantly lighter than traditional materials like steel and aluminum. For instance, forged carbon fiber reduces weight by approximately 42% when replacing aluminum and is nearly five times lighter than steel. This reduction in weight directly enhances fuel efficiency and overall performance in applications such as automotive and aerospace engineering.
The material’s ability to deliver high strength without adding unnecessary bulk ensures that components remain robust under stress. Engineers leverage this property to design lightweight yet durable structures, improving both speed and energy efficiency. By combining strength and lightness, forged carbon fiber redefines the possibilities for high-performance applications.
Exceptional Durability and Resistance
Forged carbon fiber exhibits remarkable durability, making it highly resistant to wear and tear. Its tightly bonded structure ensures excellent crack resistance, even under extreme conditions. Unlike traditional materials, it resists corrosion and abrasion, which extends the lifespan of components exposed to harsh environments. This durability proves invaluable in industries like aerospace, where materials must endure high temperatures, pressure fluctuations, and impact forces.
The material’s resilience also contributes to safety and reliability. Components made from forged carbon fiber maintain their structural integrity over time, reducing the risk of failure. This reliability makes it an ideal choice for critical applications, such as aircraft parts and automotive safety features.
Design Flexibility for Complex Geometries
The manufacturing process of forged carbon fiber allows for unparalleled design flexibility. Unlike traditional carbon fiber, which requires weaving and layering, forged carbon fiber uses randomly oriented fibers mixed with resin. This unique process enables the material to be molded into intricate shapes and complex geometries without compromising strength. Engineers can create curved, hollow, or multi-dimensional components that meet specific design requirements.
This adaptability opens new possibilities for innovation. In the automotive industry, manufacturers use forged carbon fiber to craft lightweight structural components and luxury interior elements with artistic appeal. Its marbled texture adds a modern aesthetic, making it a popular choice for high-end designs. The ability to combine functionality with visual appeal sets forged carbon fiber apart from other materials.
Cost-Effectiveness in Production
Forged carbon fiber offers a cost-effective solution for industries requiring high-performance materials. Its manufacturing process reduces material waste by utilizing chopped carbon fibers instead of continuous strands. This approach minimizes the need for precision weaving, which is both time-consuming and labor-intensive. By streamlining production steps, manufacturers achieve significant savings in both time and resources.
The ability to mold forged carbon fiber into complex shapes in a single step further enhances its cost efficiency. Traditional materials like aluminum and steel often require multiple processes, such as cutting, welding, and finishing, to achieve similar results. In contrast, forged composites eliminate these additional steps, reducing production costs while maintaining superior quality.
Moreover, the lightweight nature of forged carbon fiber contributes to long-term savings. For example, replacing aluminum with forged carbon fiber reduces weight by approximately 42%, while it is nearly five times lighter than steel. This weight reduction translates to improved fuel efficiency in automotive and aerospace applications, lowering operational costs over time. The durability of forged carbon fiber also minimizes maintenance expenses, as its resistance to corrosion and wear ensures a longer lifespan for components.
Industries benefit from the adaptability of forged carbon fiber, which allows for the production of intricate designs without compromising structural integrity. This versatility eliminates the need for additional materials or reinforcements, further reducing costs. By combining affordability with exceptional performance, forged carbon fiber has become a revolutionary choice for manufacturers seeking to optimize both production and operational efficiency.
Applications in the Automotive Industry

Lightweight Structural Components
Forged carbon fiber has revolutionized the design of lightweight structural components in the automotive industry. Engineers prioritize reducing vehicle weight to enhance fuel efficiency and performance. Forged carbon fiber achieves this by offering a superior strength-to-weight ratio compared to traditional materials like steel and aluminum. For example, replacing aluminum with forged carbon fiber can reduce weight by approximately 42%, while maintaining or even exceeding the strength of the original material.
The adaptability of forged composites allows manufacturers to create intricate structural parts such as chassis components, suspension arms, and body panels. These parts not only reduce the overall weight of the vehicle but also improve handling and acceleration. The material’s resistance to corrosion and wear ensures that these components maintain their integrity over time, even under extreme conditions. This combination of durability and lightness makes forged carbon fiber an indispensable material for modern automotive engineering.
Luxury Interiors and Aesthetic Features
In addition to its functional benefits, forged carbon fiber has become a popular choice for luxury interiors and aesthetic features in high-end vehicles. Its marbled texture provides a unique, modern appearance that distinguishes it from the traditional woven pattern of standard carbon fiber. This visual appeal has made it a favorite among designers seeking to create sophisticated and innovative interiors.
Automakers use forged composites to craft elements such as dashboard trims, center consoles, and door panels. These components not only enhance the vehicle’s aesthetic value but also contribute to weight reduction. The material’s ability to be molded into complex shapes allows designers to experiment with bold and intricate designs, elevating the overall luxury experience for consumers. Furthermore, the durability of forged carbon fiber ensures that these interior features remain pristine and resistant to wear over time.
Motorsport Innovations with Forged Composites
Motorsport teams have embraced forged composites for their ability to deliver high performance under demanding conditions. The lightweight nature of forged carbon fiber plays a crucial role in improving speed and agility on the racetrack. By reducing the weight of critical components such as aerodynamic elements, suspension systems, and engine covers, teams achieve better acceleration and handling.
The isotropic properties of forged carbon fiber provide consistent strength in all directions, making it ideal for parts subjected to multidirectional forces during high-speed maneuvers. Additionally, its resistance to heat and impact ensures reliability during intense competition. Motorsport engineers also value the material’s design flexibility, which allows them to create custom components tailored to specific performance requirements.
The use of forged composites in motorsport not only enhances performance but also drives innovation in automotive technology. Many advancements developed for racing applications eventually find their way into consumer vehicles, further solidifying the importance of forged carbon fiber in the industry.
Applications in the Aerospace Industry

Structural Components for Aircraft
Forged composites have become a cornerstone in the aerospace industry, particularly for crafting structural components. Aircraft manufacturers prioritize materials that combine strength, lightness, and durability. Forged composites meet these demands by offering a superior strength-to-weight ratio compared to traditional materials like aluminum or steel. This property allows engineers to design lighter fuselage sections, wing structures, and other critical parts without compromising safety or performance.
The adaptability of forged composites enables the creation of intricate shapes and geometries essential for modern aircraft designs. Engineers can mold components to fit specific aerodynamic requirements, enhancing fuel efficiency and reducing drag. Additionally, the material’s resistance to fatigue and corrosion ensures long-term reliability, even under extreme conditions such as high altitudes and fluctuating temperatures. These qualities make forged composites an indispensable material for advancing aerospace engineering.
Heat and Impact Resistance in Aerospace Applications
The aerospace industry demands materials that can withstand extreme environments. Forged composites excel in this regard, offering exceptional resistance to both heat and impact. Aircraft components often face intense thermal stress during flight, especially in areas near engines or exposed to atmospheric friction. Forged composites maintain their structural integrity under these conditions, ensuring consistent performance and safety.
Impact resistance is another critical factor in aerospace applications. During flight, aircraft encounter various forces, including turbulence and potential debris impacts. Forged composites absorb and distribute these forces effectively, reducing the risk of damage. This resilience not only enhances safety but also minimizes maintenance requirements, contributing to cost efficiency for airlines and manufacturers.
Future Innovations in Sustainable Aviation
Forged composites play a pivotal role in shaping the future of sustainable aviation. The material’s lightweight nature directly contributes to reduced fuel consumption, which lowers carbon emissions. As the aerospace industry shifts toward greener technologies, forged composites offer a viable solution for creating more efficient and environmentally friendly aircraft.
Researchers and engineers continue to explore new applications for forged composites in sustainable aviation. Potential innovations include integrating the material into electric aircraft designs, where weight reduction is crucial for optimizing battery performance. Additionally, advancements in recycling processes for forged composites could further enhance their sustainability, aligning with global efforts to reduce waste and promote circular economies.
The unique properties of forged composites position them as a key driver of innovation in the aerospace industry. By enabling lighter, stronger, and more efficient designs, they pave the way for a future where aviation becomes both high-performing and environmentally responsible.
Comparison with Other Materials
Advantages Over Traditional Carbon Fiber
Forged composites offer distinct advantages over traditional carbon fiber, making them a preferred choice for many industries. Traditional carbon fiber relies on woven strands arranged in a grid-like pattern, which provides strength primarily along specific directions. In contrast, forged composites consist of randomly oriented carbon fibers mixed with resin. This unique structure ensures consistent strength in all directions, enhancing their performance under multidirectional forces.
The manufacturing process of forged composites also eliminates the need for weaving, allowing for greater design flexibility. Engineers can mold these materials into complex shapes without compromising structural integrity. This adaptability proves invaluable in applications requiring intricate geometries, such as automotive body panels or aerospace components. Furthermore, the marbled appearance of forged composites offers a modern aesthetic that appeals to luxury markets, unlike the uniform woven texture of traditional carbon fiber.
Durability is another area where forged composites excel. Their tightly bonded structure resists cracks, abrasion, and environmental wear more effectively than traditional carbon fiber. This resilience ensures a longer lifespan for components, reducing maintenance costs and enhancing reliability in demanding environments.
Comparison with Aluminum in Weight and Strength
Forged composites outperform aluminum in both weight and strength, making them a superior material for high-performance applications. Aluminum, while lightweight, cannot match the strength-to-weight ratio of forged composites. For example, replacing aluminum with forged composites reduces weight by approximately 42%, while maintaining or exceeding the original material’s strength. This weight reduction directly improves fuel efficiency and performance in industries like automotive and aerospace.
The ability of forged composites to withstand extreme conditions further sets them apart. Aluminum is prone to corrosion and fatigue over time, especially in harsh environments. Forged composites, on the other hand, resist these issues due to their robust structure and resistance to environmental factors. This durability ensures that components remain reliable and safe throughout their operational life.
Additionally, the design flexibility of forged composites surpasses that of aluminum. Engineers can create intricate shapes and complex geometries in a single production step, whereas aluminum often requires multiple processes like cutting and welding. This streamlined manufacturing process not only saves time but also reduces production costs, making forged composites a more efficient and cost-effective choice.
How Forged Carbon Fiber Outperforms Steel
Forged composites redefine performance standards by outperforming steel in several critical areas. Steel, known for its strength, is significantly heavier than forged composites. The lightweight nature of forged composites makes them nearly five times lighter than steel, offering substantial weight savings without compromising strength. This characteristic is crucial in industries where reducing weight enhances efficiency and performance.
The corrosion resistance of forged composites also surpasses that of steel. Steel requires protective coatings to prevent rust and degradation, especially in environments exposed to moisture or chemicals. Forged composites eliminate this concern with their inherent resistance to corrosion, ensuring long-term durability and reduced maintenance requirements.
Impact resistance is another domain where forged composites excel. Steel, while strong, can deform under high-impact forces. Forged composites absorb and distribute impact energy more effectively, maintaining their structural integrity even under extreme conditions. This property makes them ideal for safety-critical applications, such as automotive crash structures or aerospace components.
The versatility of forged composites further enhances their appeal. Unlike steel, which often requires extensive machining and assembly, forged composites can be molded into complex shapes during production. This capability reduces manufacturing steps and costs, providing a more efficient solution for creating high-performance components.
The Future of Forged Carbon Fiber
Expanding Applications in Emerging Technologies
Forged carbon fiber continues to redefine possibilities in emerging technologies. Its unique combination of strength, lightness, and adaptability positions it as a material of choice for industries pushing the boundaries of innovation. Engineers and designers are leveraging its properties to create advanced solutions in fields such as robotics, renewable energy, and consumer electronics.
In robotics, forged carbon fiber enables the development of lightweight yet durable components. Robotic arms and structural frames benefit from its superior strength-to-weight ratio, which enhances precision and efficiency. The material’s resistance to fatigue ensures long-term reliability, even in high-stress environments. Additionally, its ability to be molded into intricate shapes allows for compact and efficient designs, critical for modern robotics.
Renewable energy systems also gain significant advantages from forged carbon fiber. Wind turbine blades, for instance, require materials that combine rigidity with minimal weight. Forged carbon fiber meets these demands by offering excellent stiffness and resistance to environmental stressors. Its low coefficient of thermal expansion ensures stability under varying temperatures, making it ideal for solar panel frames and other energy infrastructure.
Consumer electronics represent another area of growth. Manufacturers use forged carbon fiber to produce lightweight, durable casings for smartphones, laptops, and wearable devices. Its marbled texture adds a premium aesthetic, appealing to high-end markets. The material’s toughness and resistance to abrasion ensure that these products maintain their quality over time, enhancing user satisfaction.
Role in Advancing Sustainability in High-Performance Industries
Forged carbon fiber plays a pivotal role in advancing sustainability across high-performance industries. Its lightweight nature directly contributes to reducing energy consumption, particularly in automotive and aerospace applications. By replacing heavier materials like steel and aluminum, forged carbon fiber helps lower fuel usage and carbon emissions, aligning with global efforts to combat climate change.
The material’s durability further supports sustainability goals. Components made from forged carbon fiber resist wear, corrosion, and environmental degradation, extending their lifespan. This longevity reduces the need for frequent replacements, minimizing waste and conserving resources. Industries benefit from lower maintenance costs while contributing to a circular economy.
Recycling initiatives for forged carbon fiber are also gaining momentum. Researchers are exploring methods to repurpose used composites, ensuring that the material remains environmentally responsible throughout its lifecycle. These advancements align with the growing demand for sustainable practices in manufacturing and production.
“Forged carbon fiber’s ability to combine performance with sustainability makes it a cornerstone for future innovations,” as noted by industry experts. Its potential to revolutionize sectors while addressing environmental concerns underscores its importance in shaping a greener future.
As industries continue to prioritize efficiency and eco-friendliness, forged carbon fiber will remain at the forefront of sustainable development. Its unmatched properties and expanding applications ensure that it will play a critical role in driving progress across diverse fields.
Forged carbon fiber has emerged as a transformative material, reshaping industries with its unmatched combination of strength, durability, and adaptability. Its innovative manufacturing process enables the creation of lightweight components that enhance performance and efficiency. Automotive and aerospace sectors rely on this material to achieve superior designs and operational advancements. The ability of forged carbon fiber to withstand extreme conditions while maintaining structural integrity ensures its relevance in high-performance applications. As industries evolve, forge carbon continues to drive innovation, offering sustainable solutions that align with future technological and environmental goals.
常见问题
锻造碳纤维与传统碳纤维有何不同?
Forged carbon fiber differs from traditional carbon fiber in its structure and manufacturing process. Traditional carbon fiber uses woven strands arranged in a grid-like pattern, providing strength in specific directions. Forged carbon fiber, on the other hand, consists of randomly oriented chopped fibers bonded with resin under high heat and pressure. This unique composition ensures consistent strength in all directions, making it ideal for components subjected to multidirectional forces. Additionally, its marbled texture offers a distinct aesthetic compared to the uniform woven appearance of traditional carbon fiber.
Why is forged carbon fiber considered lightweight yet strong?
Forged carbon fiber achieves its lightweight yet strong properties through its innovative manufacturing process. The material combines tightly interwoven carbon fibers with epoxy resin, creating a dense and compact structure. This results in a superior strength-to-weight ratio, outperforming materials like steel and aluminum. For example, forged carbon fiber is nearly five times lighter than steel while maintaining comparable or greater strength, making it indispensable for high-performance applications.
How does forged carbon fiber improve fuel efficiency?
The lightweight nature of forged carbon fiber directly contributes to improved fuel efficiency. By reducing the weight of vehicles or aircraft, the material lowers energy consumption during operation. In the automotive industry, replacing heavier materials like steel or aluminum with forged carbon fiber enhances fuel economy and reduces carbon emissions. Similarly, in aerospace, lighter aircraft components lead to better fuel efficiency and overall performance.
哪些行业最受益于锻造碳纤维?
Forged carbon fiber has revolutionized industries such as automotive, aerospace, and sporting goods. In the automotive sector, it enhances vehicle performance by reducing weight and improving safety. Aerospace applications rely on its strength-to-weight ratio for crafting lightweight structural components and improving fuel efficiency. Sporting goods manufacturers use it to create durable yet lightweight equipment, such as bicycles and tennis rackets, that enhance user performance.
Can forged carbon fiber withstand extreme conditions?
Yes, forged carbon fiber is highly resistant to extreme conditions. Its tightly bonded structure ensures durability under high temperatures, pressure fluctuations, and impact forces. The material resists corrosion and abrasion, making it suitable for harsh environments. These properties make it a reliable choice for critical applications, such as aircraft components and motorsport innovations, where materials must endure demanding conditions without compromising performance.
Is forged carbon fiber more cost-effective than traditional materials?
Forged carbon fiber offers cost advantages due to its efficient manufacturing process. The use of chopped fibers eliminates the need for precision weaving, reducing production time and material waste. Additionally, its ability to be molded into complex shapes in a single step minimizes the need for additional machining or assembly. While the initial cost may be higher than some traditional materials, the long-term savings in fuel efficiency, maintenance, and durability make it a cost-effective solution.
What are the aesthetic benefits of forged carbon fiber?
Forged carbon fiber features a marbled texture that sets it apart from the uniform woven appearance of traditional carbon fiber. This unique aesthetic appeals to luxury markets, particularly in automotive interiors and high-end consumer products. Designers value its modern and artistic look, which adds sophistication to components like dashboard trims, center consoles, and electronic device casings.
How does forged carbon fiber contribute to sustainability?
Forged carbon fiber supports sustainability by reducing energy consumption and waste. Its lightweight nature lowers fuel usage in transportation industries, leading to decreased carbon emissions. The material’s durability extends the lifespan of components, minimizing the need for replacements and conserving resources. Researchers are also exploring recycling methods to repurpose used composites, further enhancing its environmental benefits.
What advancements can be expected in forged carbon fiber technology?
Ongoing advancements in materials engineering will expand the applications of forged carbon fiber. Emerging technologies, such as robotics and renewable energy systems, are already leveraging its properties. For instance, wind turbine blades and solar panel frames benefit from its strength and resistance to environmental stressors. As recycling processes improve, forged carbon fiber will become even more sustainable, solidifying its role as a game-changing material in various industries.
为什么锻造碳纤维被认为是革命性的?
Forged carbon fiber is revolutionary due to its unmatched combination of strength, lightness, and adaptability. Its innovative manufacturing process enables the creation of complex geometries without compromising structural integrity. Industries like automotive and aerospace rely on it to achieve superior designs and operational advancements. Its ability to enhance performance while addressing sustainability challenges positions it as a transformative material for the future.