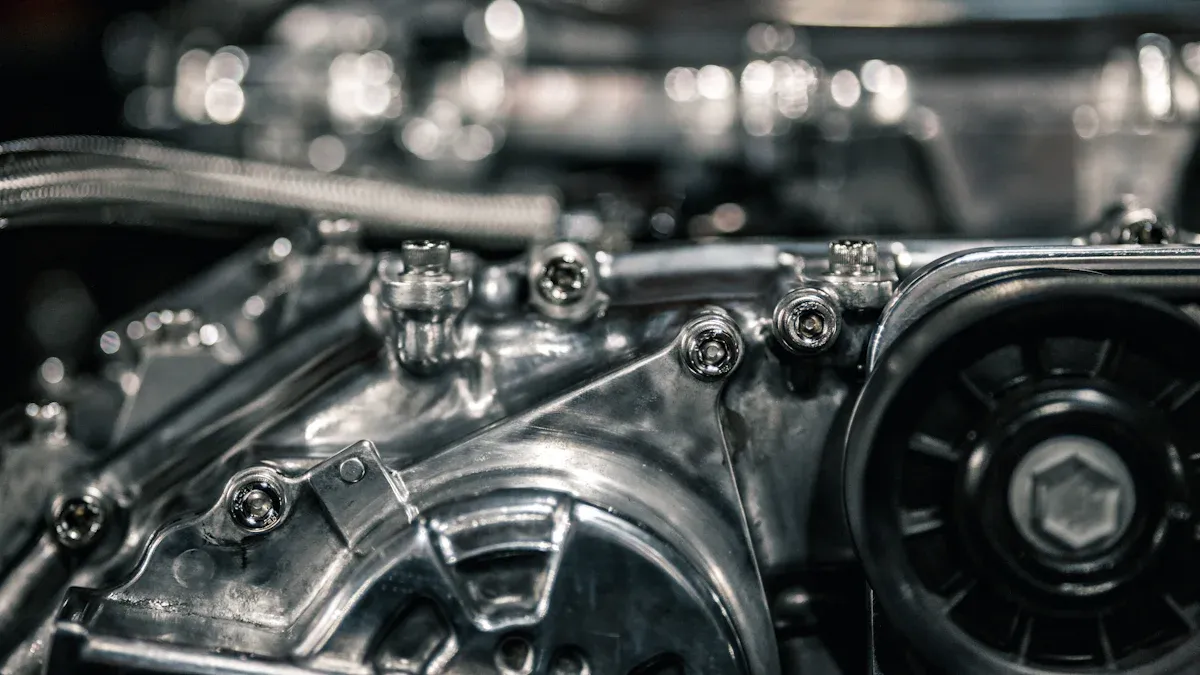
Stainless steel has revolutionized the automotive industry with its unmatched durability and versatility. You see its impact in electric vehicles (EVs), where it ensures corrosion resistance, enhances battery efficiency, and supports lightweight designs for better fuel economy. Globally, the automotive stainless steel market reached a value of USD 120 billion in 2022, with the U.S. contributing USD 102 billion. Its recyclability and strength-to-weight ratio make it a cornerstone of sustainable transportation. By embracing stainless steel, you contribute to 不锈钢在汽车和运输中的应用, driving both innovation and environmental responsibility.
Belangrijkste opmerkingen
Stainless steel is fully recyclable, helping reduce waste and save resources.
Lightweight stainless steel makes cars use less fuel, up to 8% better for every pound saved. This is great for electric cars.
Special stainless steel alloys make cars safer by absorbing crash energy and staying strong in tough situations.
Adding IoT tech to stainless steel parts helps monitor cars in real-time, making them safer and work better.
3D printing with stainless steel makes creating parts faster and cheaper, helping build complex car parts more easily.
Sustainability and Eco-Friendly Practices
Recyclability and Circular Economy
Stainless steel plays a vital role in sustainable manufacturing practices. Its ability to retain properties after multiple recycling cycles makes it ideal for a circular economy. You can rely on stainless steel to reduce waste in automotive production. It is 100 percent recyclable, ensuring minimal environmental impact. Its durability also minimizes the need for new resources, as it resists corrosion and product failure.
Functie | Beschrijving |
---|---|
Recycleerbaarheid | Stainless steel retains its properties even after multiple recycling cycles, making it ideal for closed-loop systems. |
Efficiënt gebruik van hulpbronnen | The recycling process is less resource-intensive than producing new stainless steel from raw materials. |
By focusing on recyclability and circular economy principles, you contribute to environmental sustainability while supporting innovation in automotive design.
Energy-Efficient Production
Energy-efficient production methods further enhance stainless steel’s eco-friendly practices. Recycling stainless steel saves approximately 50-60% of the energy required to produce it from raw materials. This significant energy reduction benefits the entire production lifecycle.
Many manufacturers now use renewable energy sources to power stainless steel production. For example:
JSL Global utilizes 282 MW of hybrid renewable power, combining wind and solar energy.
This clean energy approach reduces carbon emissions and ensures eco-friendly operations.
By adopting these advanced methods, you help reduce the environmental footprint of automotive manufacturing.
Reducing Carbon Footprint in Vehicles
Lightweight stainless steel improves fuel efficiency in vehicles. Every pound lost in a vehicle’s mass can increase fuel economy by up to 8%. The Forta H-Series stainless steel, with its high yield strength, allows for thinner components. This can reduce weight by up to 40% compared to mild steels, directly enhancing fuel efficiency.
In electric vehicles (EVs), stainless steel offers additional benefits. Its high strength-to-weight ratio supports lightweight designs, improving energy efficiency and driving range. Corrosion resistance ensures the durability of components like battery housings and connectors, reducing maintenance costs. Stainless steel also enhances thermal conductivity, helping maintain optimal battery temperatures and improving overall vehicle performance.
By integrating stainless steel into vehicle designs, you promote eco-friendly practices and reduce the carbon footprint of modern transportation.
Advanced Alloys and Lightweight Applications
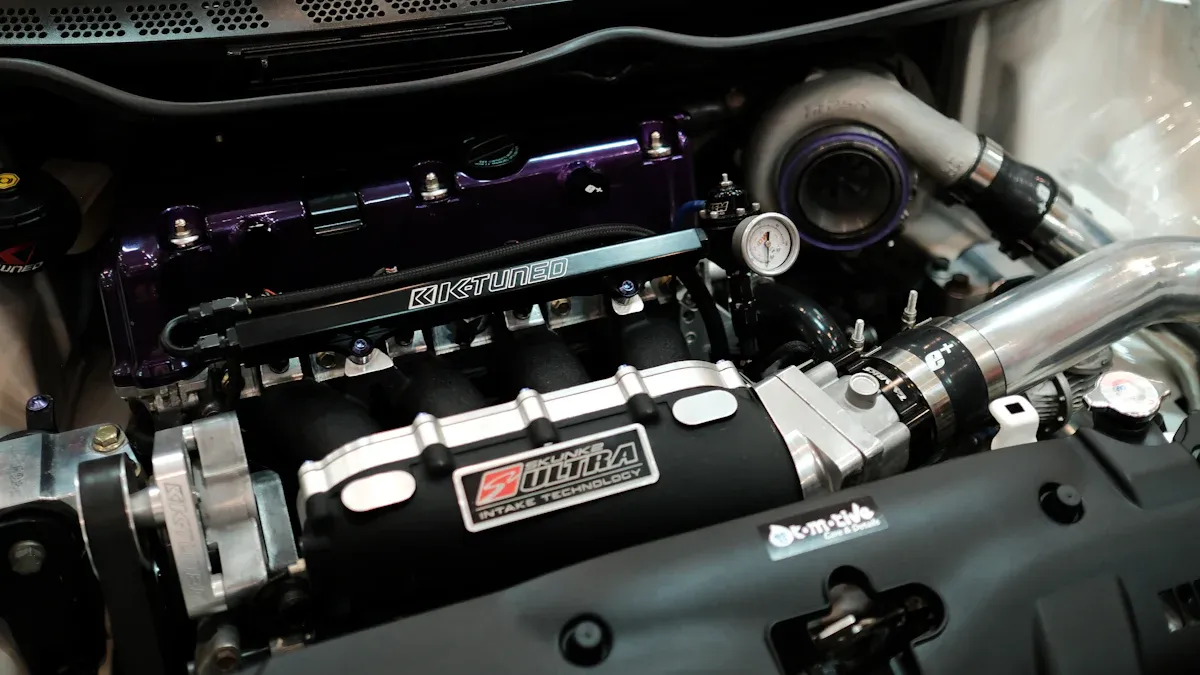
High-Strength Stainless Steel Grades
Enhanced safety and crash resistance
High-strength stainless steel grades play a critical role in ensuring passenger safety during collisions. These materials absorb crash energy effectively, reducing the impact on the passenger compartment. Their ability to harden upon impact enhances energy absorption, making them ideal for safety-critical components. For example, these steels dissipate crash forces, protecting passengers from violent forces during accidents.
Recent advancements in high-strength stainless steel have expanded their use in automotive engineering. These materials maintain strength at temperatures up to 300°C, making them suitable for electric vehicle (EV) components. Their non-magnetic properties also enhance their compatibility with EV systems. By incorporating these advanced alloys for specialized applications, you can improve both safety and performance in modern vehicles.
Durability in extreme conditions
High-strength stainless steel grades exhibit exceptional durability in extreme environments. They resist heat, flame, and mechanical stress, ensuring structural integrity even under challenging conditions. This durability makes them a reliable choice for vehicles operating in harsh climates or demanding applications.
Weight Reduction for Performance
Balancing strength and weight for better fuel economy
Stainless steel offers an excellent strength-to-weight ratio, enabling the production of thinner components without compromising safety. This balance reduces vehicle weight, improving fuel economy and overall performance. For instance, the Forta H-Series stainless steel combines high yield strength with elongation, allowing for lightweight engineering opportunities. By using these materials, you can achieve weight reduction while maintaining structural integrity.
Applications in EV battery enclosures and chassis
Stainless steel’s high strength allows for thinner gauges, reducing weight by up to 40%. This makes it an ideal material for EV battery enclosures and chassis. While denser than aluminum, stainless steel compensates with its ability to form thinner, stronger components. New nickel-free austenitic manganese-chromium materials further enhance its suitability for safety-critical parts. These innovations demonstrate the expanded use of advanced materials in automotive applications.
Corrosion Resistance and Longevity
Longevity in harsh environments
Stainless steel resists corrosion in challenging environments, including those with high chloride concentrations or temperature fluctuations. Higher grades, such as duplex steels, offer superior resistance in chloride-rich conditions. Oxygen availability also helps maintain the protective layer, ensuring long-term durability. This longevity reduces the need for frequent replacements, making stainless steel a cost-effective choice for automotive applications.
Reduced maintenance costs for vehicle owners
The corrosion resistance of stainless steel minimizes maintenance requirements. It reduces the risk of failures caused by environmental factors, lowering downtime and repair costs. Additionally, its long lifespan means fewer replacements, saving vehicle owners money over time. By choosing stainless steel, you ensure durability and cost efficiency for your vehicle.
Integratie met slimme technologieën
IoT-Enabled Stainless Steel Components
Sensors embedded in stainless steel parts
Stainless steel components now integrate seamlessly with IoT (Internet of Things) technology. Manufacturers embed sensors directly into stainless steel parts, enabling vehicles to collect and transmit real-time data. These sensors monitor critical parameters like temperature, pressure, and structural integrity. For example, in electric vehicles, sensors in battery enclosures ensure optimal performance by tracking heat levels and preventing overheating. This innovation enhances safety and reliability, making stainless steel a vital material in modern manufacturing.
Real-time performance monitoring and diagnostics
IoT-enabled stainless steel parts allow you to monitor vehicle performance in real time. This capability ensures early detection of potential issues, reducing the risk of breakdowns. For instance, embedded sensors can alert you to wear and tear in critical components, enabling timely maintenance. This proactive approach minimizes downtime and extends the lifespan of your vehicle. By leveraging IoT technology, stainless steel contributes to smarter, more efficient automotive systems.
AI-Driven Manufacturing Processes
Precision in stainless steel part production
Artificial intelligence (AI) has transformed modern manufacturing by improving precision in stainless steel part production. AI-powered quality control systems analyze every detail during production, ensuring flawless components. These systems detect defects that human inspection might miss, guaranteeing high-quality results. For example, AI algorithms optimize the shaping and cutting of stainless steel, achieving intricate designs with unmatched accuracy. This level of precision supports the production of advanced automotive parts.
Reduced material waste through predictive analytics
AI-driven processes also reduce material waste in stainless steel manufacturing. Predictive analytics tools analyze production data to identify inefficiencies and optimize resource usage. By minimizing waste, you not only save costs but also contribute to sustainable practices. For instance, AI systems can predict the exact amount of stainless steel needed for a specific component, reducing excess material. This approach aligns with the industry’s goals of efficiency and environmental responsibility.
Enhanced Vehicle Functionality
Stainless steel’s role in autonomous vehicle systems
Stainless steel plays a crucial role in the development of autonomous vehicles. Its structural integrity ensures safety in critical areas like battery enclosures, body panels, and frames. The material’s lightweight nature improves the range and efficiency of electric vehicles, which is essential for autonomous systems. Additionally, its thermal conductivity helps maintain optimal battery temperatures, enhancing battery life and overall vehicle performance. Corrosion resistance further ensures the longevity of components, reducing maintenance costs and supporting sustainability.
Improved connectivity and durability in smart vehicles
Smart vehicles rely on durable materials to support advanced technology. Stainless steel’s composition ensures adaptability and longevity, enhancing overall performance. Its high crash energy absorption and corrosion resistance make it ideal for critical components like battery housings and connectors. These properties reduce maintenance costs and prolong the vehicle’s lifespan. By incorporating stainless steel, you improve both the connectivity and durability of modern smart vehicles.
Innovative Surface Finishes and Aesthetic Customization
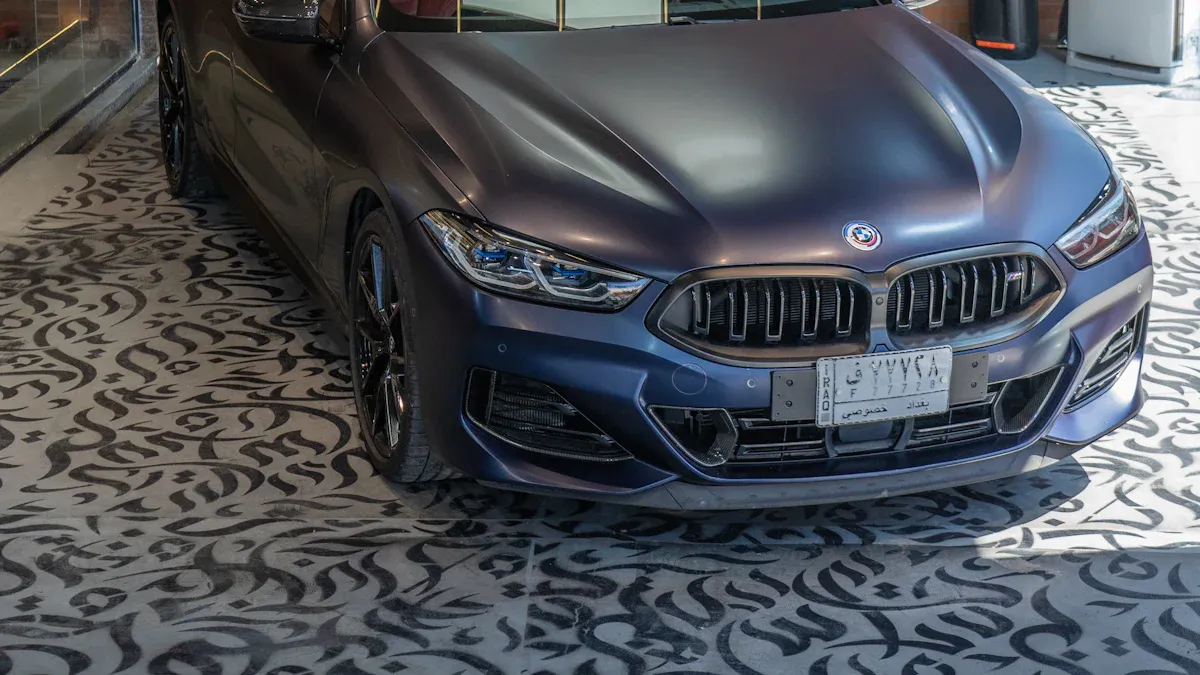
Advanced Coatings for Durability
Scratch-resistant and anti-corrosion finishes
You can rely on stainless steel’s advanced coatings to enhance durability and protect against wear and tear. These coatings utilize a passive layer of chromium oxide (Cr2O3), which forms naturally on the surface, providing excellent corrosion resistance. Passivation processes further thicken this layer, improving its protective properties.
To enhance scratch resistance, manufacturers use surface treatments like:
Polishing: Smooths the surface, reducing the likelihood of scratches.
Sandblasting: Increases surface roughness, making it less prone to visible damage.
Pickling: Removes oxides and impurities, boosting corrosion resistance.
These enhanced finishing techniques ensure that stainless steel components maintain their integrity and appearance, even in challenging environments.
UV-resistant coatings for long-lasting aesthetics
UV-resistant coatings protect stainless steel from discoloration and degradation caused by prolonged sun exposure. These coatings preserve the material’s sleek appearance, ensuring that vehicles retain their aesthetic appeal over time. By incorporating these coatings, you can achieve a balance between functionality and style, making stainless steel an ideal choice for automotive applications.
Design Flexibility and Customization
Unique textures and patterns for luxury vehicles
Stainless steel offers unparalleled design flexibility, allowing you to create unique textures and patterns that elevate the look of luxury vehicles. Techniques like embossing and etching enable intricate designs, adding a touch of sophistication to automotive interiors and exteriors. These customizations not only enhance visual appeal but also align with the growing demand for personalized vehicle designs.
Integration of custom stainless steel profiles in designs
The adaptability of stainless steel in sheet metal fabrication makes it perfect for integrating custom stainless steel profiles into automotive designs. These profiles can be tailored to meet specific requirements, whether for structural components or decorative elements. By leveraging this versatility, you can achieve innovative designs that combine aesthetics with functionality.
Enhancing Brand Identity
Use of stainless steel for premium branding elements
Stainless steel plays a significant role in reinforcing brand identity. Its sleek and modern appearance adds a premium touch to vehicles, while its sustainable nature aligns with eco-conscious branding. For example:
Aspect | Beschrijving |
---|---|
Esthetisch aantrekkelijk | The sleek look of etched stainless steel enhances vehicle sophistication. |
Duurzaamheid | Stainless steel’s recyclability supports environmentally friendly branding. |
Veiligheidsfuncties | Durable components with no sharp edges improve the perception of quality and safety. |
By incorporating stainless steel, you can create a lasting impression of luxury and innovation.
Custom finishes for limited-edition models
Custom finishes, such as brushed or mirror-polished stainless steel, add exclusivity to limited-edition models. These finishes highlight the craftsmanship and attention to detail that define premium vehicles. Additionally, the durability of stainless steel ensures that these finishes remain pristine, reinforcing the value of these exclusive designs.
Rapid Prototyping and Manufacturing Efficiency
3D Printing with Stainless Steel
Faster prototyping of complex parts
3D printing with stainless steel has revolutionized automotive prototyping. You can now create intricate geometries that were once impossible with traditional methods. This technology enables rapid prototyping, allowing you to test and refine designs in a fraction of the time. The high-strength and corrosion-resistant properties of stainless steel ensure that prototypes are not only functional but also durable. Additionally, lightweight designs produced through 3D printing contribute to improved fuel efficiency, aligning with environmental responsibility goals. By adopting this approach, you reduce waste and inventory needs, supporting cleaner production processes.
Cost-effective production of small batches
For small batch production, 3D printing offers unmatched flexibility. It eliminates the need for costly tooling, enabling you to produce custom parts on demand. This process optimization is ideal for low-volume manufacturing, where traditional methods often fall short. The ability to iterate designs quickly further reduces costs and shortens research and development timelines. With selective laser melting (SLM) technology, you can achieve high precision and adaptability, making it a cost-effective solution for producing robust materials like stainless steel.
Laser Cutting and Precision Engineering
High-precision manufacturing of intricate components
Advances in laser cutting technology have set new standards for precision in automotive manufacturing. Laser cutting machines can handle complex shapes, such as curved structures and intricate pipes, without compromising material quality. This ensures that every component meets the highest standards of accuracy and durability. The speed and precision of laser cutting make it indispensable for producing high-spec automotive parts, especially when tight tolerances are required.
Laser cutting delivers exceptional accuracy, meeting the demands of industries like automotive where precision is paramount.
Reduced lead times in production cycles
Laser cutting significantly reduces lead times in stainless steel production. Its efficiency allows for high-volume manufacturing while maintaining material integrity. Minimal heat-affected zones ensure that the quality of stainless steel remains intact, even in intricate designs. Increased automation in laser systems further boosts productivity, enabling faster turnaround times. This makes laser cutting a cornerstone in the future of sheet metal fabrication.
Modular Manufacturing Approaches
Stainless steel’s adaptability in modular designs
Stainless steel’s versatility makes it ideal for modular automotive manufacturing. Its high strength and formability allow you to create thinner, lighter components without sacrificing durability. Applications include protective battery enclosures for electric vehicles, seat structures, and crashboxes. By reducing weight by up to 40%, stainless steel enhances vehicle performance while supporting sustainability efforts.
Streamlining assembly processes for efficiency
Modular designs benefit from stainless steel’s lightweight and formable nature. These properties simplify the production of complex geometries, streamlining assembly processes. You can achieve significant weight reductions while maintaining structural integrity, cutting production time and costs. This approach not only optimizes manufacturing but also aligns with the industry’s commitment to environmental responsibility.
Stainless steel has transformed the automotive industry by offering unmatched durability, sustainability, and adaptability. You see its impact in lightweight designs, corrosion-resistant components, and energy-efficient production methods. Its role in 不锈钢在汽车和运输中的应用 highlights its importance in creating eco-friendly and high-performance vehicles. Emerging trends in stainless steel, such as advanced alloys and smart technologies, continue to shape the future of automotive manufacturing. By embracing these innovations, you contribute to a sustainable and efficient transportation ecosystem. The potential for 不锈钢在汽车和运输中的应用 remains limitless as the industry evolves.
The journey of emerging trends in stainless steel promises a future where vehicles are safer, smarter, and more sustainable.