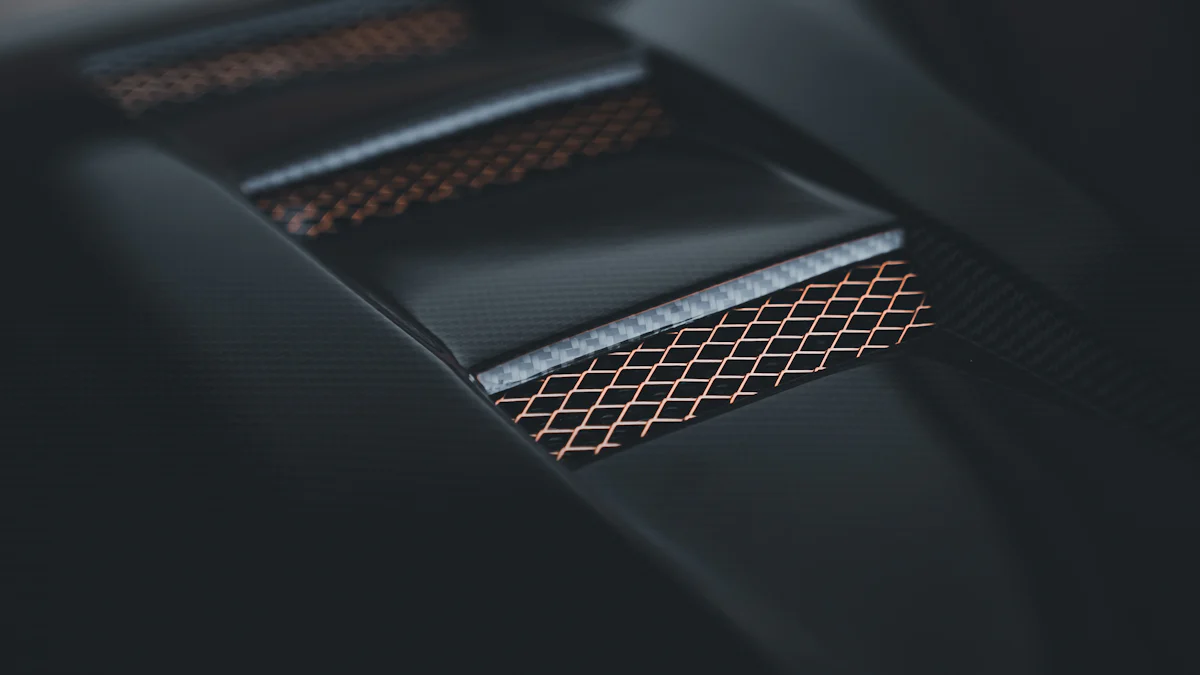
Lamborghini has revolutionized supercar engineering by mastering carbon fiber technology. You can trace their journey back to 1983 when they first adopted carbon fiber with Boeing’s assistance. This innovation led to the Countach Evoluzione, the first road car with a carbon fiber chassis. Lamborghini’s advancements didn’t stop there. In 2009, they introduced Forged Composites technology, which enabled the creation of the Sesto Elemento, a lightweight marvel. The Aventador’s carbon-fiber monocoque, weighing just 506 pounds, exemplifies their commitment to reducing weight without compromising strength. Lamborghini carbon fiber innovations continue to set benchmarks in performance and safety, as seen in the Essenza SCV12’s FIA-certified roll cage.
Lamborghini’s partnership with the University of Washington and Boeing further refined their expertise, ensuring their supercars remain at the forefront of engineering excellence.
Key Takeaways
Lamborghini pioneered the use of carbon fiber in supercars, starting with the Countach Evoluzione in 1983, setting a standard for lightweight and high-performance vehicles.
The introduction of Forged Composites technology revolutionized carbon fiber production, allowing for faster manufacturing and unique aesthetics, enhancing both performance and design.
Sustainability is a priority for Lamborghini, with efforts focused on recycling materials and reducing energy consumption, aligning their innovations with global environmental goals.
Lamborghini’s carbon fiber innovations significantly improve vehicle performance, including acceleration and handling, while also enhancing safety through superior crash resistance.
Customization options for carbon fiber elements allow Lamborghini owners to personalize their vehicles, combining luxury with cutting-edge technology.
Lamborghini’s History with Carbon Fiber
Early Adoption and Milestones
The Countach Evoluzione and the first use of carbon fiber
You can trace Lamborghini’s journey with carbon fiber back to 1983 when the company established the Esperienza Materiali Compositi department in collaboration with Boeing. This marked the beginning of their exploration into lightweight materials. The Countach Evoluzione, a prototype designed as a testbed for new technologies, became the first Lamborghini to feature carbon fiber. It incorporated advanced materials like Kevlar and carbon fiber, setting a precedent for future supercars. This innovation demonstrated Lamborghini’s commitment to pushing boundaries in automotive engineering.
Lamborghini’s commitment to lightweight materials since the 1980s
Lamborghini’s dedication to lightweight materials has remained unwavering since the 1980s. Key milestones include:
1983: The Countach Evoluzione prototype introduced carbon fiber to Lamborghini’s design philosophy.
2007: A partnership with the University of Washington advanced composite technology, paving the way for the Aventador’s monocoque.
2008: Collaboration with Boeing led to groundbreaking research on crash behavior in composite materials.
2011: The Aventador LP 700-4 debuted with a carbon fiber monocoque, weighing just 229.5 kg, showcasing Lamborghini’s expertise in lightweight construction.
These milestones highlight how Lamborghini carbon fiber innovations have consistently redefined performance and safety standards in the supercar industry.
Establishing the Advanced Composite Structures Laboratory (ACSL)
The role of ACSL in pioneering carbon fiber research
Lamborghini established the Advanced Composite Structures Laboratory (ACSL) to lead research in lightweight materials. This facility, located in Seattle, focuses on developing cutting-edge technologies like Forged Composites. By collaborating with Boeing, the ACSL has become a hub for innovation, ensuring Lamborghini remains at the forefront of carbon fiber advancements. The lab’s work enhances both the performance and aesthetics of Lamborghini’s supercars, solidifying its reputation as a leader in material science.
Key achievements, including the Aventador’s carbon-fiber structure
The ACSL has achieved remarkable milestones in carbon fiber development. Notable accomplishments include:
Designing and certifying the Aventador’s monocoque using aerospace-inspired methods.
Developing liquid resin infusion processes for out-of-autoclave manufacturing.
Introducing the marbled carbon fiber aesthetic seen in models like the Sesto Elemento and Huracán Performante.
Pioneering 3D printing for engineering and artistic prototypes.
These innovations have elevated Lamborghini carbon fiber technology, enabling the creation of supercars that are lighter, stronger, and more visually striking.
Key Innovations in Lamborghini Carbon Fiber Technology
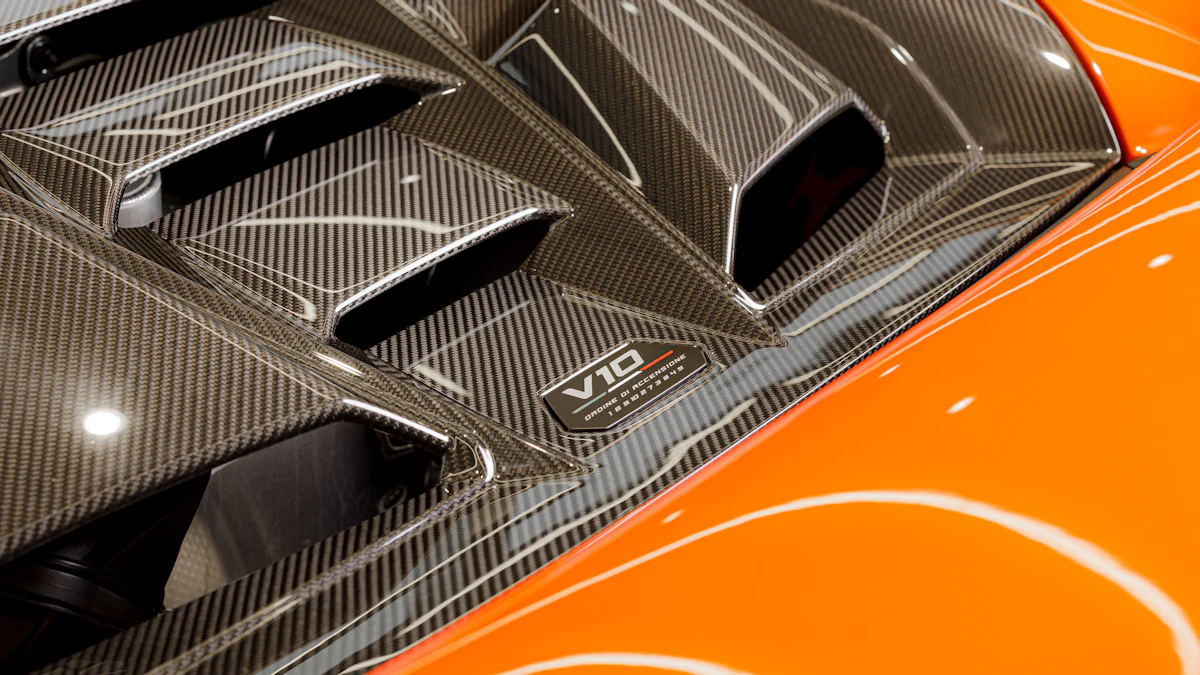
Forged Composites Technology
How Forged Composites revolutionized carbon fiber use
Forged Composites technology represents a groundbreaking shift in how carbon fiber is utilized. Unlike traditional methods that rely on layered and woven fibers, this process compresses millions of tiny carbon fibers into a solid structure. This innovative approach eliminates the need for precise cutting and laying of materials, making production faster and more efficient. Each component crafted with Forged Composites boasts a unique aesthetic due to the random orientation of fibers, setting it apart from the uniform patterns of traditional carbon fiber.
Feature | Forged Composites Technology | Traditional Carbon Fiber Methods |
---|---|---|
Fiber Orientation | Randomly oriented fibers | Layered and woven fibers |
Manufacturing Process | Made from a paste or tiny chopped fibers | Layered and molded |
Aesthetic Variation | Each product is unique due to random orientation | Consistent patterns due to woven structure |
Benefits in strength, weight, and production efficiency
Forged Composites delivers exceptional benefits across multiple dimensions:
Strength: Its high strength-to-weight ratio enhances durability and resilience.
Weight Reduction: The lightweight nature improves performance and fuel efficiency.
Production Efficiency: Compression molding reduces production time and costs.
Impact Resistance: It absorbs and disperses energy effectively, improving safety.
Corrosion Resistance: The material resists environmental wear, extending its lifespan.
These advantages make Forged Composites a cornerstone of Lamborghini’s engineering excellence.
Proprietary Manufacturing Processes
Lamborghini’s unique methods for carbon fiber production
Lamborghini has developed proprietary methods to streamline carbon fiber production. The company’s RTM-Lambo technology, created in partnership with the University of Washington, eliminates the need for manual lamination and autoclaves. This innovation significantly reduces production time while maintaining the structural integrity of components. Additionally, Lamborghini’s Forged Composite process mixes short carbon fiber strands with uncured plastic, which is then pressed into molds. This method produces parts that are as light and stiff as traditionally made carbon fiber components but in a fraction of the time.
Integration of automation and precision engineering
You benefit from Lamborghini’s integration of automation and precision engineering in their carbon fiber production. By treating carbon fiber similarly to metals and plastics, Lamborghini achieves faster production cycles without sacrificing quality. For example, the Revuelto features a fully carbon fiber front structure, which enhances energy absorption and reduces weight. This approach ensures that Lamborghini carbon fiber innovations continue to lead the industry in both performance and efficiency.
Sustainability in Carbon Fiber Development
Reducing waste and environmental impact
Lamborghini prioritizes sustainability in its carbon fiber development. The company focuses on recycling all composite materials and reducing energy consumption during production. Waste materials are repurposed for other applications, such as vehicle components or promotional items. These efforts minimize environmental impact while maximizing resource efficiency.
Step | Description |
---|---|
1 | Focus on sustainability and waste recycling. |
2 | Reduction of energy consumption in production processes. |
3 | Reuse of composite material waste in other applications. |
Future goals for sustainable material innovation
Lamborghini aims to achieve circular sustainability in carbon fiber production. The company has implemented technologies that minimize energy and water usage. Additionally, Lamborghini is exploring new materials that are lighter, more durable, and environmentally friendly. These advancements not only enhance the performance of their supercars but also align with global sustainability goals.
Applications of Lamborghini Carbon Fiber in Supercars
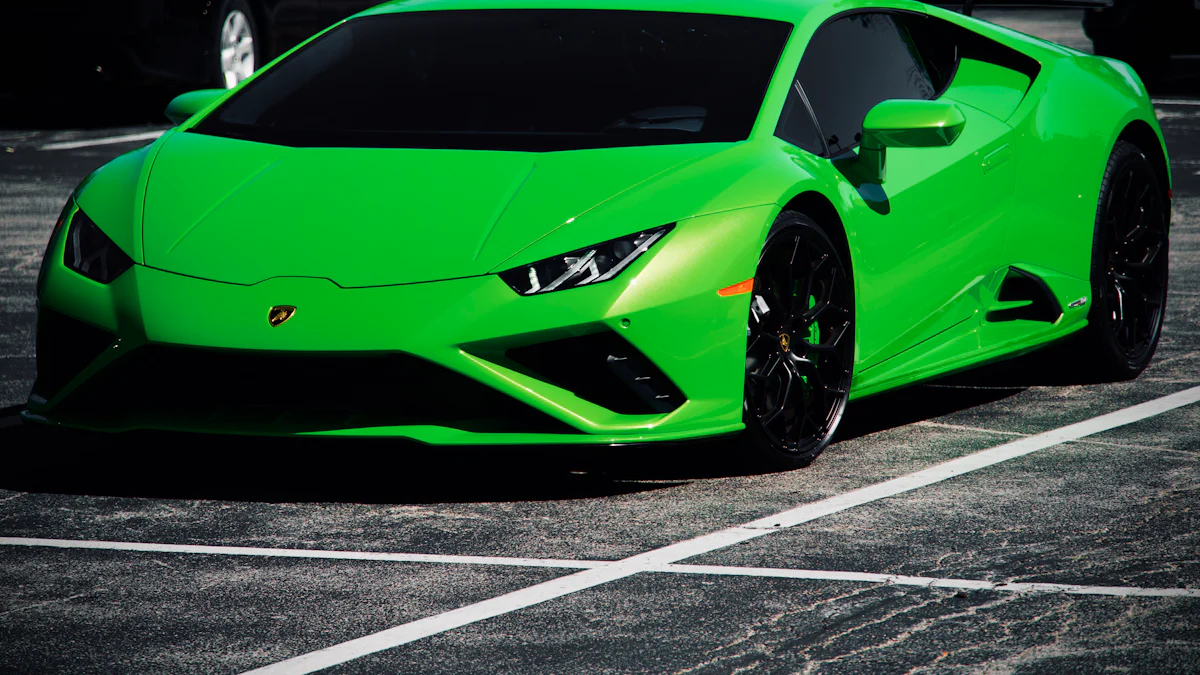
Structural Components
Carbon fiber monocoque chassis for rigidity and safety
Lamborghini’s use of carbon fiber in structural components has redefined supercar engineering. The carbon fiber monocoque chassis, first introduced in the Aventador LP 700-4, is a prime example. Weighing only 324 pounds, this single-shell structure maximizes rigidity while minimizing weight. Its design enhances handling, acceleration, and overall performance. Additionally, the integration of epoxy foam components within the monocoque increases stiffness and reduces noise and vibration, ensuring a superior driving experience. Lamborghini’s Forged Composite technology further streamlines the production of these components, maintaining strength and efficiency.
Examples from models like the Aventador and Huracán
You can see Lamborghini’s expertise in models like the Aventador and Huracán. The Aventador’s carbon fiber monocoque exemplifies lightweight innovation, while the Huracán incorporates advanced composites for improved structural integrity. The LB744 takes this a step further with its all-carbon fiber monofuselage, making it the first supercar with a fully carbon fiber front-end. These advancements highlight Lamborghini’s commitment to safety and performance.
Exterior and Aerodynamic Features
Use in body panels, spoilers, and diffusers
Lamborghini applies carbon fiber extensively to exterior components, including body panels, spoilers, and diffusers. The lightweight nature of carbon fiber enhances speed and handling, critical for high-performance vehicles. For example, the Sesto Elemento features Forged Composites technology, enabling the creation of complex shapes that optimize aerodynamics. This innovation allows Lamborghini to push the boundaries of design while maintaining low weight.
Component Description | Price Range |
---|---|
Rear Spoiler Wing | $880 – $2,460 |
Rear Bumper & Diffuser | $1,380 – $5,260 |
Side Skirts | $1,020+ |
Full Body Kit | $5,220+ |
Enhancing aerodynamics and reducing drag
Lamborghini’s carbon fiber expertise ensures that every exterior feature contributes to performance. The Advanced Composite Structures Laboratory focuses on optimizing these components to reduce drag and improve downforce. This approach not only enhances speed but also ensures stability at high velocities.
Interior Design and Customization
Lightweight carbon fiber accents in the cabin
Inside the cabin, Lamborghini incorporates lightweight carbon fiber accents to enhance both aesthetics and performance. The development of Carbonskin, a flexible carbon matrix, revolutionized interior design. This material is lighter than traditional options like leather, reducing overall vehicle weight. Crafted with high-grade carbon fiber, these trims improve agility and responsiveness while maintaining a luxurious feel.
Personalization options for customers
Lamborghini offers extensive customization options for interior carbon fiber elements. You can choose from various finishes and weave patterns, such as matte or gloss, to match your personal style. These options allow you to create a unique and exclusive interior that complements the vehicle’s design.
Benefits of Lamborghini Carbon Fiber Innovations
Enhanced Performance
Improved acceleration, handling, and top speed
Lamborghini’s use of carbon fiber directly enhances the performance of its supercars. The lightweight and aerodynamic properties of carbon fiber allow you to experience faster acceleration and improved handling. For instance:
The Aventador’s carbon-fiber monocoque weighs only 147.5 kg, enabling it to reach a top speed of 350 km/h. It accelerates from 0 to 100 km/h in just 2.9 seconds.
The Sesto Elemento, 250 kilograms lighter than traditional counterparts, delivers unmatched agility and responsiveness.
These innovations ensure that Lamborghini supercars remain at the pinnacle of speed and precision.
Performance metrics achieved through carbon fiber
Lamborghini carbon fiber technology achieves remarkable performance metrics. The Aventador’s monocoque structure weighs just 506 pounds, contributing to its exceptional speed and handling. The Essenza SCV12 features a carbon fiber roll cage certified to withstand 12 tons of force, ensuring safety without compromising performance. The Sesto Elemento, with 75% of its chassis made from CFRP, weighs only 999 kilograms, showcasing the potential of composites to redefine supercar engineering.
Weight Reduction
Importance of lightweight materials in supercar design
Lightweight materials like carbon fiber are essential in supercar design. They enhance speed, fuel efficiency, and safety. By reducing weight, Lamborghini supercars require less energy for propulsion, improving overall performance. The versatility of carbon fiber also allows for innovative designs that combine functionality with aesthetics.
How weight reduction improves fuel efficiency and agility
Weight reduction plays a critical role in improving fuel efficiency and agility. For example:
The Sesto Elemento’s lightweight construction enhances acceleration and handling, making it more agile on the road.
Reduced weight means less power is needed, leading to lower fuel consumption and a 20% reduction in CO2 emissions.
These advancements ensure that Lamborghini supercars deliver both thrilling performance and environmental responsibility.
Durability and Safety
Carbon fiber’s strength-to-weight ratio and crash resistance
Carbon fiber offers an exceptional strength-to-weight ratio, making it ideal for supercar construction. It absorbs energy by fracturing during collisions, reducing the impact transmitted to the cabin. For instance:
The Aventador’s carbon-fiber monocoque weighs only 506 pounds, enhancing both strength and crash resistance.
Crash tests reveal that carbon fiber effectively absorbs crash energies, ensuring passenger safety.
This material’s unique properties provide you with a safer driving experience without compromising performance.
Real-world examples of safety benefits in Lamborghini models
Lamborghini supercars demonstrate the safety benefits of carbon fiber in real-world scenarios.
The Essenza SCV12 features the world’s first FIA-certified carbon fiber roll cage, capable of withstanding 12 tons of force. This innovation ensures enhanced safety during high-impact situations.
The carbon fiber monocoque undergoes over 20 static tests, including dynamic crash tests at speeds up to 14 meters/second, ensuring high safety standards.
These examples highlight Lamborghini’s commitment to protecting you while delivering unparalleled performance.
How Lamborghini Stands Out in Carbon Fiber Innovation
Industry Leadership
Lamborghini’s influence on the automotive industry’s use of carbon fiber
You can see Lamborghini’s leadership in carbon fiber innovation through its groundbreaking contributions to the automotive industry. In 1983, Lamborghini collaborated with Boeing to establish the Esperienza Materiali Compositi department, which led to the creation of the Countach Evoluzione, the first road car prototype with a carbon fiber chassis. This early adoption set the stage for decades of advancements. In 2007, Lamborghini partnered with the University of Washington to develop RTM technology, which became integral to the Aventador’s monocoque. The introduction of Forged Composites technology in 2009 further revolutionized carbon fiber manufacturing, enabling faster production and greater design flexibility.
Awards and recognition for material innovation
Lamborghini’s achievements in carbon fiber have earned global recognition. At the 2016 JEC Composites Exhibition, Lamborghini received the Innovation Award for its carbon fiber package developed for the Huracán. This accolade highlights Lamborghini’s commitment to pushing the boundaries of material science and engineering excellence.
Award | Year | Event | Description |
---|---|---|---|
Innovation Award | 2016 | JEC Composites Exhibition | Recognized for the carbon fiber package developed for the Lamborghini Huracán. |
Comparison with Competitors
How Lamborghini’s carbon fiber technology surpasses rivals
Lamborghini’s carbon fiber technology consistently outpaces its competitors. The company’s partnership with the University of Washington led to the development of out-of-autoclave resin transfer molding, a process that enhances efficiency and precision. Unlike traditional methods, Lamborghini’s Forged Composite process produces lightweight and strong components in minutes rather than hours. This innovation gives you access to supercars that are not only faster but also more durable.
Unique features that set Lamborghini apart
Lamborghini’s approach to carbon fiber is unmatched. The Sesto Elemento, for example, showcases extensive use of composite materials, resulting in a vehicle that is both lightweight and incredibly agile. Lamborghini’s proprietary Forged Composite material, made from randomly oriented carbon fibers, allows for quicker production without compromising performance. These advancements ensure that Lamborghini carbon fiber remains a benchmark in the industry.
Vision for the Future
Next-generation carbon fiber applications
Lamborghini continues to explore new frontiers in carbon fiber technology. In 2019, the company tested composite materials in space to evaluate their performance under extreme conditions. These experiments pave the way for future applications in both automotive and medical fields. Lamborghini’s Advanced Composite Structures Laboratory, established in 2016, remains at the forefront of research, ensuring that you benefit from the latest innovations in material science.
Role of carbon fiber in Lamborghini’s hybrid and electric supercars
Carbon fiber plays a pivotal role in Lamborghini’s transition to hybrid and electric supercars. The LB744 features an all-carbon fiber monofuselage frame inspired by aeronautics, enhancing strength and torsional stiffness while reducing weight. Similarly, the Revuelto incorporates a carbon fiber monocoque chassis, improving both performance and fuel efficiency. These advancements demonstrate Lamborghini’s commitment to sustainability and cutting-edge engineering.
Lamborghini’s expertise in carbon fiber technology has transformed the supercar industry. You benefit from their relentless pursuit of innovation, which combines advanced materials, efficient manufacturing, and sustainable practices. These breakthroughs ensure unmatched performance, exclusivity, and safety in every model. Lamborghini carbon fiber innovations continue to set benchmarks, shaping the future of high-performance vehicles. As Lamborghini pushes boundaries, you can expect their engineering excellence to redefine what’s possible in automotive design.
FAQ
What makes Lamborghini’s carbon fiber technology unique?
Lamborghini uses proprietary methods like Forged Composites and RTM-Lambo technology. These processes reduce production time while maintaining strength and precision. You benefit from lightweight, durable components that enhance performance and safety.
How does carbon fiber improve Lamborghini supercars’ performance?
Carbon fiber reduces weight, improving acceleration, handling, and top speed. Its strength-to-weight ratio enhances structural rigidity and crash resistance. You experience better agility and safety without compromising luxury or design.
Is Lamborghini’s carbon fiber production sustainable?
Yes, Lamborghini prioritizes sustainability by recycling composite materials and reducing energy consumption. Waste materials are repurposed, and the company explores eco-friendly innovations to align with global environmental goals.
Which Lamborghini models feature carbon fiber innovations?
Models like the Aventador, Huracán, and Sesto Elemento showcase extensive carbon fiber use. The LB744 introduces a fully carbon fiber monofuselage, setting new standards in lightweight construction and performance.
Can you customize carbon fiber elements in a Lamborghini?
Absolutely. Lamborghini offers customization options for interior and exterior carbon fiber components. You can choose finishes, patterns, and accents to create a personalized, exclusive design.