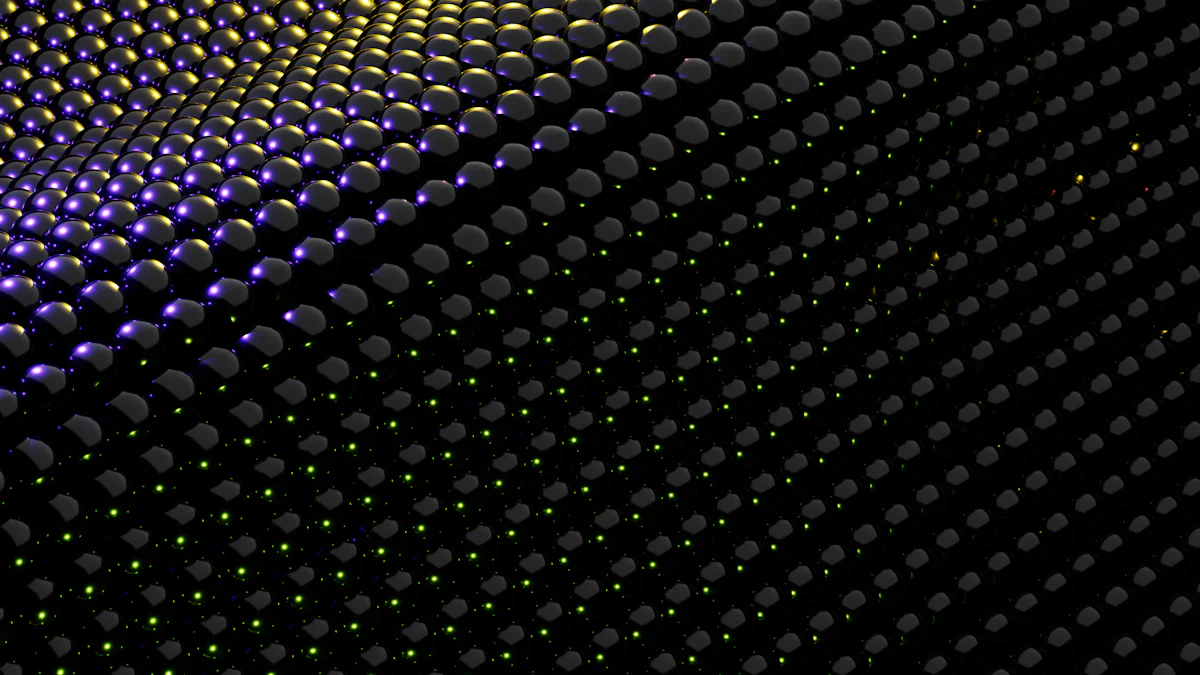
La fibre de carbone sèche est un matériau révolutionnaire fabriqué à partir de feuilles de carbone pré-imprégnées. Sa composition unique garantit une résistance et une légèreté exceptionnelles, ce qui la rend indispensable dans des secteurs tels que l'automobile et l'aérospatiale. Par exemple, les constructeurs automobiles l'utilisent pour réduire le poids des véhicules jusqu'à 50%, ce qui améliore considérablement le rendement énergétique et les performances. Le processus de fabrication du carbone sec met l'accent sur la précision, garantissant une distribution cohérente de la résine et un alignement des fibres. Cette approche méticuleuse permet d'obtenir un matériau qui surpasse les alternatives traditionnelles en termes de qualité et de fiabilité, répondant ainsi aux exigences des applications de pointe.
Principaux enseignements
La fibre de carbone sèche est un matériau léger et résistant, idéal pour les applications de haute performance dans les secteurs de l'automobile et de l'aérospatiale.
Le processus de fabrication du carbone sec donne la priorité à la précision, assurant une distribution cohérente de la résine et un alignement des fibres pour une qualité supérieure.
L'utilisation de matériaux pré-imprégnés (pré-imprégnés) permet de mieux contrôler la résine, de réduire les déchets et d'améliorer les propriétés mécaniques du produit final.
Le processus de durcissement en autoclave renforce le carbone sec en appliquant de la chaleur et de la pression, ce qui permet d'obtenir une finition impeccable et une meilleure durabilité.
Le rapport exceptionnel entre la résistance et le poids du carbone sec permet de concevoir des composants qui améliorent le rendement énergétique et les performances des véhicules et des avions.
Le choix d'une fibre de carbone sèche favorise les pratiques de fabrication durables en minimisant les déchets de matériaux et en réduisant l'impact sur l'environnement.
Des techniques avancées telles que l'enroulement filamentaire permettent de créer des structures spécialisées, répondant aux exigences précises des applications de haute performance.
Qu'est-ce que la fibre de carbone sèche ?
Définition et propriétés uniques
La fibre de carbone sèche est un matériau de pointe connu pour sa résistance, sa légèreté et sa précision. Contrairement aux matériaux traditionnels, elle est fabriquée à partir de feuilles de carbone pré-imprégnées, où la résine est répartie uniformément sur les fibres avant le début du processus de durcissement. Cela permet d'obtenir une structure cohérente, exempte d'irrégularités, et d'améliorer ses propriétés mécaniques.
L'une des principales caractéristiques du carbone sec est sa capacité à atteindre une fraction volumique de fibre plus élevée. Cela signifie qu'il y a plus de fibres de carbone dans le matériau, ce qui se traduit par une rigidité, une solidité et une résistance à la fatigue supérieures. En outre, l'imprégnation contrôlée de la résine minimise les déchets, ce qui en fait un choix respectueux de l'environnement. Des industries telles que l'aérospatiale et l'automobile s'appuient sur ces propriétés uniques pour créer des composants qui exigent à la fois durabilité et réduction du poids.
Différences entre la fibre de carbone sèche et la fibre de carbone humide
La principale distinction entre la fibre de carbone sèche et la fibre de carbone humide réside dans leur processus de fabrication. Le carbone sec utilise des matériaux pré-imprégnés, souvent appelés "pre-preg", où la résine est déjà infusée dans le tissu de carbone. Cette méthode garantit un contrôle précis de la résine et élimine la nécessité d'une application manuelle. En revanche, le carbone humide implique l'application manuelle de résine sur les feuilles de carbone au cours de la production, ce qui peut entraîner une distribution inégale et une intégrité structurelle plus faible.
Le carbone sec est soumis à un processus de durcissement dans un autoclave, une chambre à haute pression et à haute température. Ce processus renforce le matériau et élimine les imperfections. Le carbone humide, quant à lui, durcit à température ambiante ou dans des conditions moins contrôlées, ce qui donne un produit plus épais et moins raffiné. Le processus complexe de création du carbone sec le rend plus fin, plus léger et plus résistant que son homologue humide. Ces qualités font du carbone sec le choix privilégié pour les applications de haute performance.
Matériaux utilisés dans la fabrication de fibres de carbone sèches
Précurseurs de la fibre de carbone
La création de carbone sec commence par la sélection du bon précurseur. Un précurseur sert de matière première pour la production de fibres de carbone. Le polyacrylonitrile (PAN) est le précurseur le plus couramment utilisé en raison de sa capacité à fournir des résultats très performants. Le PAN subit un processus appelé carbonisation, au cours duquel il est chauffé à des températures extrêmement élevées dans un environnement sans oxygène. Cette étape transforme le précurseur en fibres de carbone pures, qui constituent l'ossature du carbone sec.
D'autres précurseurs, tels que la rayonne et le brai, ont également été étudiés. La rayonne a été l'un des premiers matériaux utilisés pour créer des fibres de carbone, tandis que le brai offre une alternative économique. Cependant, le PAN reste la norme dans l'industrie en raison de ses propriétés mécaniques supérieures. Le choix du précurseur a un impact direct sur la résistance, la rigidité et la durabilité du produit final. En sélectionnant et en traitant soigneusement ces matériaux, les fabricants s'assurent que les fibres de carbone répondent aux exigences rigoureuses d'industries telles que l'aérospatiale et l'automobile.
Matériaux pré-imprégnés et systèmes de résine
Les matériaux pré-imprégnés, ou préimprégnés, jouent un rôle crucial dans la production de carbone sec. Ces matériaux sont constitués de feuilles ou de tissus de fibres de carbone préinfusés avec de la résine. La résine, répartie uniformément sur les fibres, élimine la nécessité d'une application manuelle au cours de la fabrication. Cela garantit la cohérence de la structure du matériau et améliore sa qualité globale.
Les systèmes de résine utilisés dans les pré-imprégnés sont spécialement formulés pour offrir des performances optimales. Les résines époxy sont le choix le plus courant en raison de leurs excellentes propriétés d'adhérence et de leur résistance aux facteurs environnementaux. Au cours du processus de polymérisation, la résine durcit, liant les fibres de carbone entre elles et créant un composite solide et léger.
Les pré-imprégnés sont durcis dans un autoclave, une chambre à haute pression et à haute température. Cette étape permet d'éliminer les impuretés et de renforcer le matériau. Le contrôle de la teneur en résine des préimprégnés permet un alignement précis des fibres, ce qui se traduit par un produit plus fin et plus uniforme. Ce processus méticuleux permet non seulement d'améliorer les propriétés mécaniques du matériau, mais aussi de réduire les déchets, ce qui fait du carbone sec une option respectueuse de l'environnement.
Processus de fabrication étape par étape du charbon sec
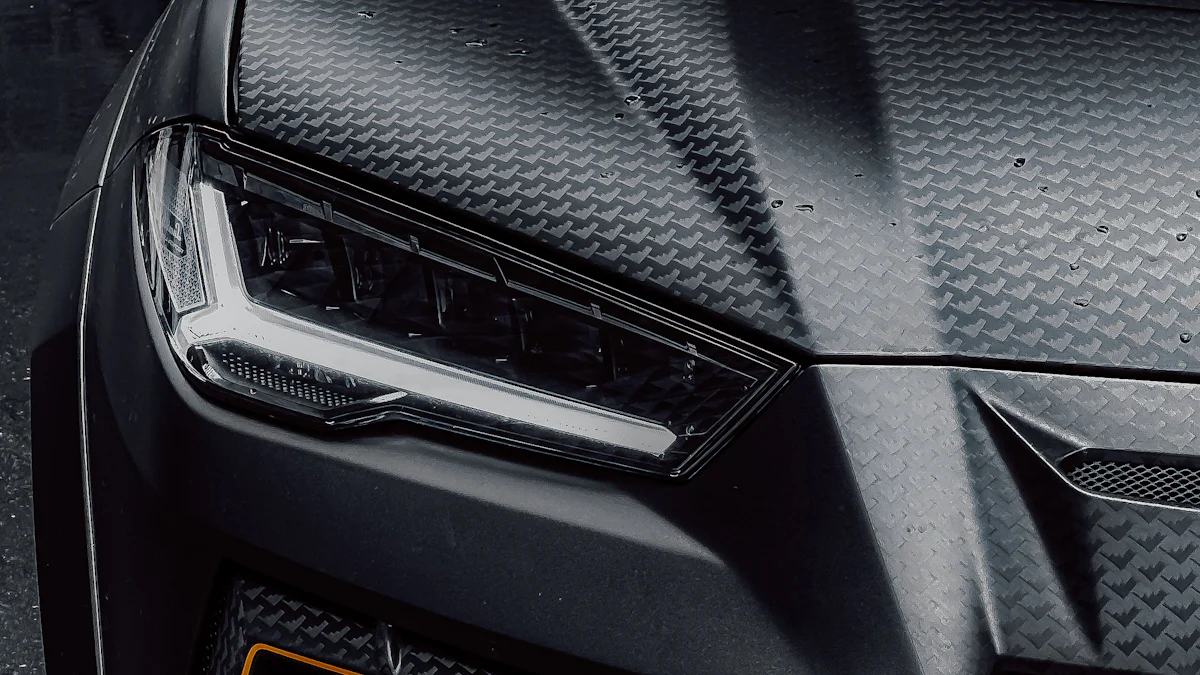
Superposition de feuilles de fibres de carbone
Le processus de fabrication commence par la superposition de feuilles de fibre de carbone. Ces feuilles, souvent appelées textiles à fibres sèches, sont livrées sous forme de rouleaux de tissu. Des machines de coupe automatisées, guidées par des données de CAO, découpent précisément le tissu dans des formes spécifiques. Cela permet de s'assurer que chaque couche s'intègre parfaitement dans la conception finale. Ces couches prédécoupées sont ensuite empilées dans un moule et soigneusement alignées pour obtenir l'orientation souhaitée des fibres. Un alignement correct est crucial car il a un impact direct sur la résistance et la rigidité du produit fini. En contrôlant cette étape, vous garantissez l'intégrité structurelle et les performances du matériau.
Application de la chaleur et de la pression
Une fois les couches en place, l'étape suivante consiste à appliquer de la chaleur et de la pression. Cette étape active la résine dans les feuilles de carbone pré-imprégnées. La résine, déjà infusée dans les fibres, commence à se ramollir sous l'effet de la chaleur. La pression assure une liaison étroite entre les couches, éliminant ainsi les poches d'air et les vides. La combinaison de la chaleur et de la pression crée une structure uniforme qui améliore les propriétés mécaniques du matériau. Vous devez surveiller de près ce processus pour maintenir la cohérence et éviter les défauts. La précision de cette étape distingue le carbone sec des autres matériaux et garantit une qualité supérieure.
Processus de polymérisation en autoclave
L'étape finale consiste à durcir le matériau dans un autoclave. L'autoclave fonctionne comme une cocotte-minute de haute technologie, utilisant des températures et des pressions élevées pour solidifier la résine. Au cours de ce processus, les impuretés sont éliminées et la résine durcit, liant les fibres de carbone entre elles. Cette étape permet non seulement de renforcer le matériau, mais aussi d'obtenir une finition lisse et impeccable. L'environnement contrôlé de l'autoclave permet d'obtenir les spécifications exactes requises pour les applications de haute performance. Au terme de ce processus, le carbone sec se présente sous la forme d'un matériau léger, durable et conçu avec précision, prêt à l'emploi.
Techniques avancées de production de fibres de carbone à sec
Procédé de pré-imprégnation pour le contrôle des résines
Le procédé de pré-imprégnation est la pierre angulaire de la production de carbone sec. Cette technique consiste à pré-imprégner les feuilles de fibres de carbone de résine avant le début du processus de fabrication. Cette méthode permet de contrôler avec précision la teneur en résine du matériau. La résine est ainsi répartie uniformément sur les fibres, ce qui élimine les incohérences susceptibles d'affaiblir le produit final.
Les matériaux pré-imprégnés font l'objet de contrôles de qualité stricts afin d'en préserver l'uniformité. Les fabricants stockent ces matériaux à basse température pour éviter un durcissement prématuré. L'utilisation de pré-imprégnés permet d'obtenir une fraction volumique de fibres plus élevée, ce qui améliore directement la résistance et la rigidité du matériau. Ce procédé permet également de réduire les déchets, car la quantité exacte de résine nécessaire est déjà infusée dans les fibres. Selon la recherche, les processus de fabrication optimisés tels que le préimprégné améliorent non seulement les propriétés mécaniques du carbone sec, mais réduisent également les coûts de production, ce qui en fait un choix durable pour les industries.
Enroulement filamentaire pour structures spécialisées
L'enroulement filamentaire est une autre technique avancée utilisée dans la production de carbone sec. Cette méthode consiste à enrouler des fibres de carbone continues autour d'un mandrin rotatif pour créer des structures cylindriques ou tubulaires. Vous pouvez utiliser cette technique pour produire des composants tels que des réservoirs sous pression, des tuyaux et des pièces aérospatiales qui nécessitent une résistance et une précision élevées.
Le processus commence par des fibres de carbone enduites de résine, qui sont soigneusement enroulées sur le mandrin selon des schémas spécifiques. L'orientation des fibres joue un rôle essentiel dans la détermination de la résistance et des performances du produit final. Une fois l'enroulement terminé, la structure est durcie dans un autoclave pour solidifier la résine et lier les fibres entre elles.
L'enroulement filamentaire offre plusieurs avantages. Il permet de créer des structures à la fois légères et durables, avec un minimum de pertes de matériaux. La possibilité de personnaliser l'orientation des fibres garantit que le produit fini répond exactement aux exigences de son application. Les chercheurs considèrent cette technique comme une innovation clé dans la production de carbone sec, permettant la création de composants spécialisés pour les industries de haute performance.
Avantages de l'utilisation de la fibre de carbone sèche
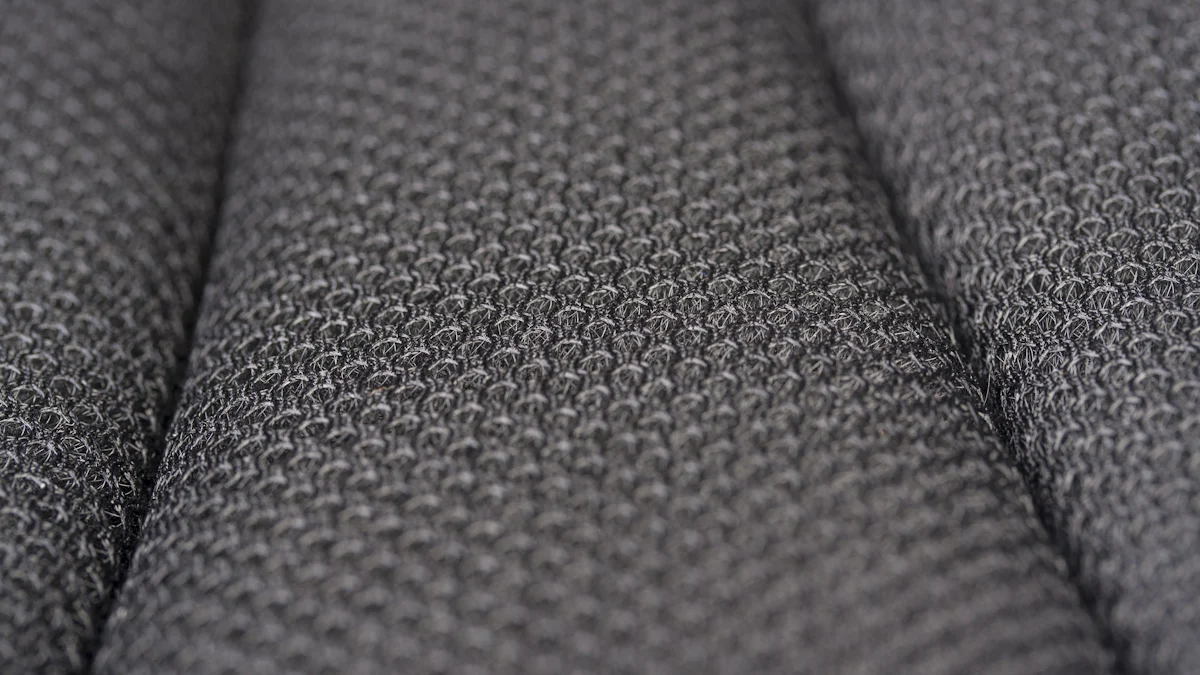
Rapport résistance/poids supérieur
Le carbone sec offre un rapport résistance/poids exceptionnel, ce qui en fait un matériau de choix pour les applications de haute performance. Vous obtenez un matériau incroyablement résistant tout en restant léger. Cet équilibre permet de concevoir des composants capables de résister à des contraintes importantes sans ajouter de poids inutile. Par exemple, dans l'industrie aérospatiale, la réduction du poids améliore directement le rendement énergétique et les performances. De même, dans l'industrie automobile, l'utilisation du carbone sec permet de créer des véhicules plus rapides et plus agiles.
La fraction volumique élevée des fibres dans le carbone sec contribue à son intégrité structurelle supérieure. En insérant davantage de fibres de carbone dans le matériau, on obtient une plus grande rigidité et une meilleure résistance à la déformation. Cette propriété garantit la fiabilité du matériau dans des conditions exigeantes. Que vous conceviez des pièces d'avion ou des composants de voitures de sport, le rapport résistance/poids du carbone sec vous donne un avantage concurrentiel.
Durabilité et précision accrues
Le carbone sec se distingue par sa durabilité et sa précision. La distribution contrôlée de la résine dans les matériaux pré-imprégnés garantit une structure uniforme, exempte de points faibles ou d'incohérences. Cette précision renforce les propriétés mécaniques du matériau, ce qui vous permet de compter sur lui pour des applications exigeant des performances à long terme. Les composants fabriqués à partir de carbone sec résistent à l'usure, même dans des environnements difficiles.
Le processus de durcissement en autoclave renforce encore le matériau. En appliquant la chaleur et la pression, vous éliminez les poches d'air et les imperfections, ce qui permet d'obtenir une finition impeccable. Ce processus méticuleux garantit que chaque pièce de carbone sec répond exactement aux spécifications. Lorsque vous utilisez du carbone sec, vous bénéficiez d'un matériau qui allie durabilité et précision, ce qui le rend idéal pour des industries telles que l'aérospatiale, l'automobile et la fabrication d'équipements sportifs.
Réduction des déchets de matériaux et de l'impact sur l'environnement
La production de carbone sec minimise les déchets de matériaux, ce qui en fait un choix respectueux de l'environnement. Le processus de pré-imprégnation assure un contrôle précis de la résine, réduisant l'excès de résine et améliorant la distribution. Cette efficacité permet de n'utiliser que la quantité nécessaire de matériau et d'éviter les déchets. Comparé aux procédés de stratification humide, le carbone sec génère beaucoup moins de déchets, ce qui contribue à des pratiques de fabrication durables.
En choisissant le carbone sec, vous réduisez également l'impact environnemental de vos projets. L'utilisation efficace des matériaux permet non seulement de réduire les coûts de production, mais aussi de s'aligner sur les objectifs écologiques. Les industries accordent de plus en plus d'importance au développement durable, et le carbone sec vous aide à répondre à ces exigences sans compromettre la qualité ou les performances. La réduction des déchets et l'utilisation efficace des ressources en font un choix responsable pour la fabrication moderne.
Le processus de fabrication du carbone sec comporte des étapes précises qui garantissent une qualité exceptionnelle. De la superposition des feuilles de fibres de carbone au durcissement en autoclave, chaque étape renforce la résistance et la durabilité du matériau. Vous bénéficiez d'un matériau plus fin, plus léger et plus résistant que le carbone humide grâce à ses méthodes de production complexes. Ses propriétés uniques, comme le contrôle supérieur de la résine et le volume élevé des fibres, en font un matériau idéal pour les applications exigeantes. À mesure que les industries continuent d'innover, le rôle du carbone sec s'élargira, offrant des solutions durables et performantes pour l'avenir.