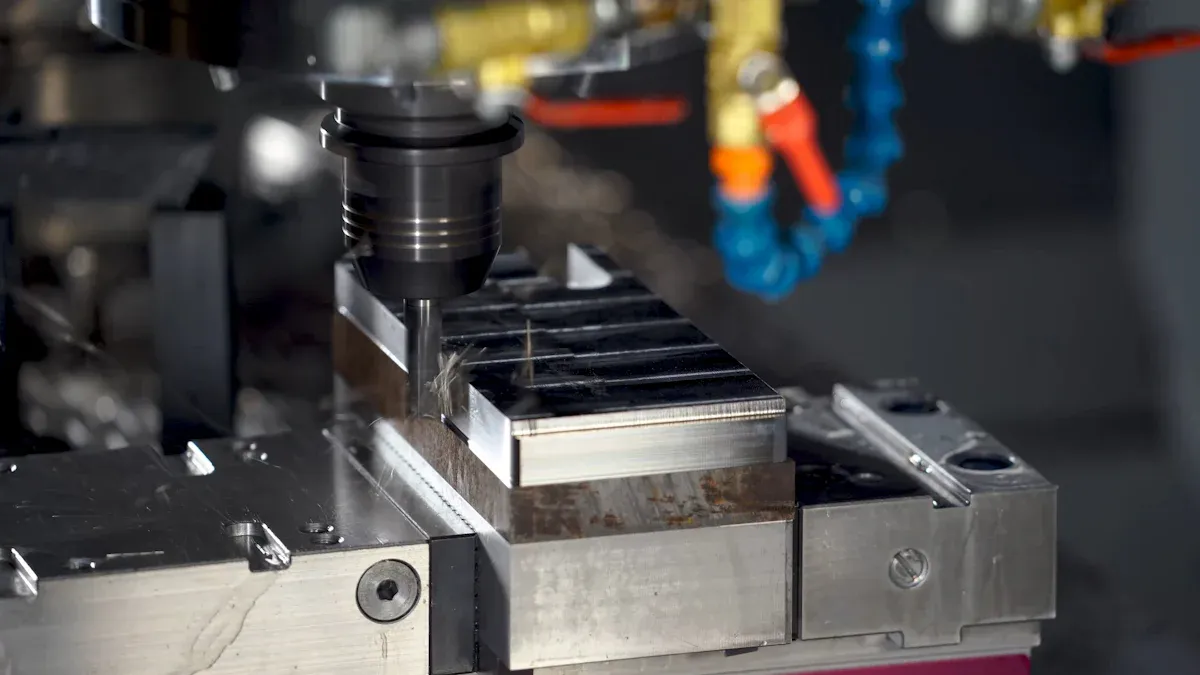
Titanium alloys have revolutionized modern engineering with their exceptional properties. These materials combine strength and lightweight characteristics, making them indispensable in industries like aerospace, automotive, and medical. Their corrosion resistance ensures durability in harsh environments, while biocompatibility supports safe use in medical implants.
The global demand for titanium continues to rise, driven by its high strength-to-weight ratio and adaptability across diverse industrial applications. From forming intricate shapes for aerospace components to maintaining structural integrity under extreme conditions, titanium alloys remain a cornerstone of innovation in advanced technologies.
Wichtigste Erkenntnisse
Titanium alloys are light but strong, perfect for planes, cars, and medicine.
They resist rust, lasting longer even in tough conditions.
Titanium is safe for the body, so it works well in implants.
Adding titanium to cars saves fuel and cuts pollution, helping the planet.
New tech like 3D printing will create more uses for titanium alloys.
Aerospace Applications of Titanium Alloys

The aerospace industry relies heavily on titanium alloys due to their exceptional properties. These materials provide the perfect balance of strength and weight, making them indispensable for modern aerospace designs.
Lightweight and High-Strength Materials
Aircraft Components
Titanium alloys are widely used in aircraft manufacturing. Their strength-to-weight ratio surpasses that of aluminum and steel, making them ideal for reducing aircraft weight without compromising structural integrity. For example:
Titanium alloys offer the strength of steel at nearly half the weight.
They are about 45% lighter than steel, which enhances fuel efficiency and payload capacity.
This weight reduction is critical for improving the performance of commercial and military aircraft. Titanium components, such as landing gear, wing structures, and fasteners, contribute to safer and more efficient designs.
Spacecraft Applications
In spacecraft, titanium alloys play a vital role in ensuring durability and performance in extreme conditions. Their lightweight nature allows engineers to optimize payloads, while their high strength ensures structural stability during launch and re-entry. Titanium’s corrosion resistance also protects spacecraft from the harsh environment of space, including exposure to radiation and temperature fluctuations.
Resistance to Extreme Temperatures
Jet Engine Parts
Jet engines operate under extreme heat, often exceeding 1,000 degrees Celsius (1,832 degrees Fahrenheit). Titanium alloys maintain their structural integrity in these conditions, thanks to their high melting point of approximately 1,660 degrees Celsius (3,020 degrees Fahrenheit). This makes them ideal for critical components like compressor blades and casings, where both strength and heat resistance are essential.
Heat Shields and Thermal Barriers
Titanium alloys are also used in heat shields and thermal barriers to protect aerospace vehicles from intense heat during atmospheric re-entry. Their phase stability ensures they retain their properties despite rapid temperature changes, making them a reliable choice for these demanding applications.
The aerospace industry’s reliance on titanium alloys highlights their unmatched versatility. Their unique combination of lightweight, high strength, and temperature resistance continues to drive innovation in aerospace engineering.
Medical Applications of Titanium Alloys
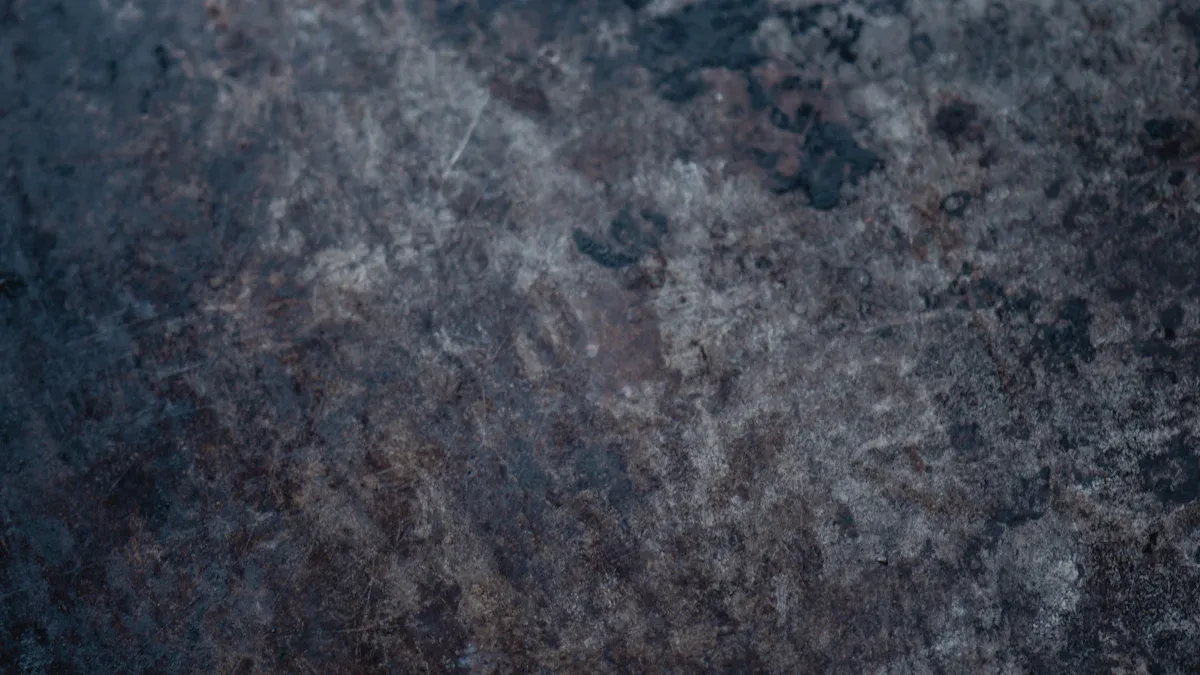
Titanium alloys have transformed the medical field with their unique properties. Their biocompatibility, corrosion resistance, and durability make them essential for various medical applications, particularly in implants and surgical instruments.
Biocompatibility and Corrosion Resistance
Implants and Prosthetics
Titanium alloys are widely used in medical implants due to their biologically compatible nature. These materials integrate seamlessly with human tissue, ensuring long-term safety and effectiveness. Titanium is inert and resists corrosion from body fluids, preventing harmful reactions or rust particles. This makes it ideal for critical devices such as:
Bone and joint replacements, including artificial hips and knees.
Dental implants for tooth restoration.
Maxillofacial and craniofacial treatments.
Cardiovascular devices like pacemaker cases and heart valves.
The high fatigue strength of titanium components ensures they can endure the repetitive stresses of daily movement, extending the lifespan of these medical device components.
Surgical Instruments
Surgical instruments crafted from titanium alloys offer unmatched precision and reliability. Their lightweight nature reduces hand fatigue for surgeons during lengthy procedures. Additionally, titanium’s resistance to corrosion ensures these tools remain sterile and functional even after repeated sterilization cycles. Common examples include forceps, scissors, and clamps used in delicate surgeries.
Durability in Medical Devices
Dental Applications
Titanium alloys play a crucial role in dental applications. Dental implants made from titanium provide a stable foundation for artificial teeth. Their ability to osseointegrate, or bond with bone, ensures a secure and long-lasting fit. This property, combined with their corrosion resistance, makes them a preferred choice for dentists worldwide.
Orthopedic Tools
Orthopedic tools benefit from the durability and strength of titanium alloys. These tools, such as bone screws and plates, support the healing of fractures and other injuries. Their lightweight design minimizes patient discomfort, while their mechanical properties ensure reliable performance under stress.
The use of titanium alloys in medical applications demonstrates their versatility and importance across industries. Their biologically compatible nature, combined with their strength and resistance to corrosion, continues to drive advancements in medical technology.
Automotive Applications of Titanium Alloys
Titanium alloys have become a game-changer in the automotive industry. Their unique properties, such as a high strength-to-weight ratio and corrosion resistance, make them ideal for high-performance applications. These materials contribute to improved fuel efficiency, durability, and environmental sustainability.
Lightweight for Fuel Efficiency
High-Performance Car Components
Titanium components are widely used in high-performance vehicles. Their lightweight nature reduces overall vehicle weight, which directly improves fuel efficiency. Additionally, titanium’s high specific strength enhances the durability of critical parts. Key advantages include:
Reduced inertia mass of moving parts, leading to better acceleration and handling.
Superior corrosion resistance, ensuring longevity in harsh environments.
Lower emissions and reduced ownership costs due to improved efficiency.
For example, titanium alloys are used in suspension springs, which are significantly lighter than steel. This weight reduction can save up to 13.6 kg in a typical family car, further enhancing fuel economy.
Electric Vehicle (EV) Applications
Titanium alloys play a vital role in electric vehicles. Reducing vehicle weight is crucial for extending battery range and improving energy efficiency. Titanium’s corrosion resistance eliminates the need for protective coatings, reducing environmental impact. A 10% reduction in vehicle weight can decrease fuel consumption by 7% and exhaust emissions by 10%, making titanium an environmentally friendly choice for EVs.
Stärke und Langlebigkeit
Engine Parts
Titanium alloys are ideal for engine components like connecting rods and valves. These parts benefit from titanium’s high strength-to-weight ratio, which reduces engine mass by up to 20%. This reduction minimizes friction, increases engine speed, and enhances overall performance. Titanium’s high-temperature resistance also ensures reliability under extreme conditions.
Exhaust Systems
Exhaust systems made from titanium alloys offer superior durability and corrosion resistance. These properties allow them to withstand high temperatures and exposure to exhaust gases. Titanium’s lightweight nature further reduces the overall weight of the vehicle, contributing to better fuel efficiency and lower emissions.
The automotive industry’s adoption of titanium alloys highlights their versatility and importance. These materials not only improve vehicle performance but also support sustainability efforts, making them indispensable in modern automotive design.
Marine Applications of Titanium Alloys
Titanium alloys play a critical role in marine industries due to their exceptional corrosion resistance and durability. These properties make them indispensable for applications in saltwater environments and equipment requiring long service life with minimal maintenance.
Corrosion Resistance in Saltwater Environments
Shipbuilding Components
Titanium alloys are highly valued in shipbuilding for their ability to withstand the corrosive effects of seawater. They form a stable oxide layer that protects against oxidation, ensuring long-term durability. This corrosion resistance is particularly beneficial for components like hulls, pipelines, and ballast tanks, which are constantly exposed to aerated and chloride-rich waters. Unlike traditional materials, titanium alloys resist pitting and stress corrosion cracking, making them a reliable choice for marine vessels.
Submarine Applications
Submarines benefit significantly from the use of titanium alloys. These materials provide not only corrosion resistance but also high strength-to-weight ratios, which are essential for underwater operations. Manufacturing titanium components for submarines can be challenging due to the material’s reactivity at high temperatures. However, advancements in welding techniques, such as friction stir and laser welding, have improved fabrication efficiency and quality. These innovations ensure that titanium remains a preferred material for critical submarine structures.
Longevity and Low Maintenance
Offshore Drilling Equipment
Offshore drilling equipment often operates in harsh marine environments where durability is paramount. Titanium alloys extend the service life of components, reducing maintenance frequency and costs. Their resistance to biofouling and corrosion ensures longer operational periods, even in aggressive conditions. However, careful design is necessary to address challenges like stress corrosion cracking and galvanic corrosion in mixed-metal systems. Proper material selection and engineering strategies mitigate these risks, ensuring reliable performance.
Marine Propellers
Marine propellers made from titanium alloys offer unmatched durability and efficiency. Their corrosion resistance eliminates the need for frequent repairs, reducing maintenance costs over time. Titanium’s ability to resist biofouling further enhances operational efficiency, as propellers remain clean and functional for extended periods. Although the initial cost of titanium is higher than traditional materials, its long-term benefits, including fewer inspections and repairs, make it a cost-effective solution for marine propulsion systems.
The use of corrosion-resistant titanium alloys in marine applications highlights their importance in industrial applications. Their unique properties, including corrosion resistance and longevity, continue to drive innovation in marine engineering.
Power Generation and Chemical Processing Applications
Titanium alloys play a vital role in power generation and chemical processing industries. Their durability and corrosion resistance make them indispensable for equipment operating in aggressive environments.
Durability in Aggressive Environments
Pressure Vessels
Pressure vessels in power plants and chemical facilities often face extreme conditions. Titanium alloys are ideal for these applications due to their ability to withstand high pressures and temperatures. They maintain structural integrity even in environments with corrosive chemicals or fluctuating thermal conditions. This durability ensures a longer operational life, reducing maintenance costs and downtime.
Heat Exchangers
Heat exchangers made from titanium alloys excel in demanding settings like refineries and power plants. These components endure extreme temperatures and harsh chemical exposure without degrading. Titanium’s corrosion resistance ensures reliable performance, even in environments containing seawater or industrial chemicals. This makes titanium heat exchangers a preferred choice for industries requiring efficient and long-lasting thermal management systems.
Titanium alloys resist chemical degradation, ensuring consistent heat transfer efficiency.
They are widely used in distillation columns and other critical chemical processing equipment.
Corrosion Resistance in Chemical Processing
Reactors
Chemical reactors often operate in environments with highly reactive substances. Titanium alloys provide superior corrosion resistance, preventing oxidation and rust. This property ensures the safe and efficient operation of reactors, even when exposed to aggressive chemicals. Their performance surpasses traditional materials like stainless steel and aluminum, making them a reliable choice for chemical processing industries.
Processing Equipment
Processing equipment benefits significantly from titanium’s unique properties. Components like pumps, valves, and piping systems resist chemical wear and tear, ensuring longevity. The table below highlights why titanium alloys outperform other materials in these applications:
Eigentum | Beschreibung |
---|---|
Korrosionsbeständigkeit | Titanium alloys resist oxidation, rust, and chemical degradation. |
Leistungsvergleich | They outperform traditional metals like stainless steel and aluminum. |
Application Areas | Suitable for marine, aerospace, medical, and chemical processing industries. |
The use of titanium alloys in power generation and chemical processing demonstrates their versatility. Their ability to endure extreme conditions while maintaining performance makes them a cornerstone of industrial applications.
Sports and Consumer Applications of Titanium Alloys
Titanium alloys have become a staple in sports and consumer products due to their lightweight, high strength, and aesthetic appeal. These materials enhance performance and durability, making them a preferred choice in competitive sports and luxury goods.
Lightweight and High Performance
Bicycle Frames
Titanium bicycle frames offer a perfect balance of strength and weight. Cyclists benefit from reduced wind resistance and improved speed during races. Titanium’s fatigue resistance ensures durability, even under prolonged stress. Riders also experience greater comfort due to the material’s ability to absorb vibrations. These advantages make titanium frames a top choice for professional and recreational cyclists alike.
Golf Clubs and Tennis Rackets
Golf clubs made from titanium improve performance significantly. The lightweight nature of titanium allows for larger clubheads, which enhance swing speed and hitting distance. Golfers also enjoy more forgiveness on off-center hits, thanks to titanium’s strength. Tennis rackets crafted from titanium alloys provide better hitting force and rebound, giving players an edge during matches.
Sportgeräte | Material Used | Vorteile |
---|---|---|
Tennisschläger | Pure titanium and titanium alloy | Enhances hitting force and rebound when striking the ball. |
Golfschläger | Titanium | Lighter ball heads improve batting average by 20% compared to steel. |
Fahrräder | Titanium and titanium alloys | Reduces weight and wind resistance, improving race speed. |
Aesthetic Appeal and Durability
High-End Watches and Sunglasses
Titanium alloys are highly valued in luxury watches and sunglasses. Their unique silver-grey color and deep luster create a modern, sophisticated appearance. Watchmakers use titanium to craft elegant timepieces that are lightweight yet durable. Similarly, titanium eyewear frames combine sleek design with exceptional strength, appealing to fashion-conscious consumers.
Aesthetic Advantage | Beschreibung |
---|---|
Unique Color | Titanium alloys have a distinctive silver-grey color that can be polished or brushed. |
Modern Appearance | They are favored by luxury watchmakers for creating high-end timepieces with sophistication. |
Deep, Dark Luster | Titanium offers a deep, dark luster that enhances the elegance of eyewear frames. |
Outdoor-Ausrüstung
Outdoor enthusiasts rely on titanium for its durability and lightweight properties. Titanium camping gear, such as cookware and tent stakes, resists corrosion and withstands harsh conditions. These products are easy to carry and maintain, making them ideal for hiking, camping, and other outdoor activities.
Titanium alloys continue to revolutionize sports and consumer industries. Their unique properties enhance performance, durability, and aesthetic appeal, solidifying their role in modern applications.
Titanium alloys represent a breakthrough in material science, offering unmatched versatility across diverse industries. Their strength, lightweight nature, and resistance to extreme conditions make them essential in aerospace, medical, automotive, and renewable energy applications. The titanium alloy market is projected to grow at a CAGR of 5.4% from 2024 to 2031, driven by increasing demand for lightweight, high-performance materials. Emerging technologies, such as 3D printing and nanotechnology, promise to expand their industrial applications further. Additionally, titanium’s corrosion resistance and energy-efficient production methods contribute to sustainability, reducing maintenance needs and environmental impact. As industries evolve, titanium alloys will continue to shape the future of innovation.