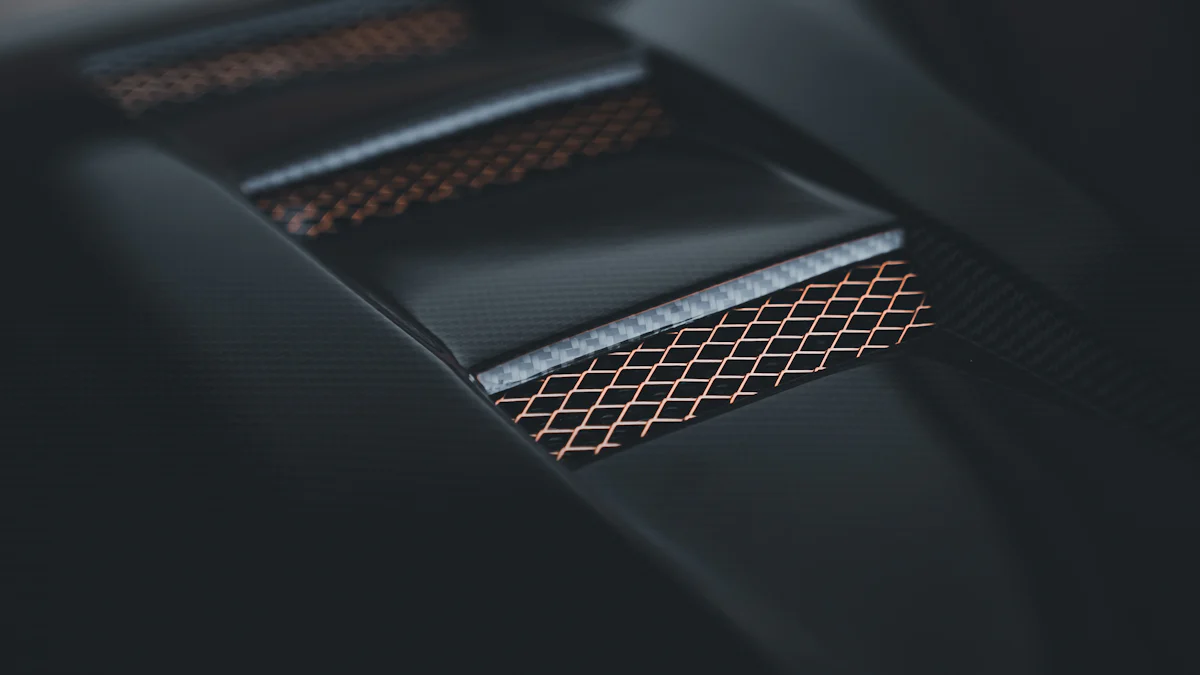
Lamborghini hat den Bau von Supersportwagen durch die Beherrschung der Kohlefasertechnologie revolutioniert. Der Weg des Unternehmens lässt sich bis ins Jahr 1983 zurückverfolgen, als Lamborghini mit Unterstützung von Boeing erstmals Kohlefaser einsetzte. Diese Innovation führte zum Countach Evoluzione, dem ersten Straßenauto mit Karbonfaser-Chassis. Die Fortschritte von Lamborghini hörten damit nicht auf. Im Jahr 2009 führte Lamborghini die Forged-Composites-Technologie ein, die die Entwicklung des Sesto Elemento, eines Leichtbauwunders, ermöglichte. Das Kohlefaser-Monocoque des Aventador wiegt nur 506 Pfund und ist ein Beispiel für das Engagement des Unternehmens, das Gewicht zu reduzieren, ohne die Festigkeit zu beeinträchtigen. Lamborghinis Kohlefaser-Innovationen setzen weiterhin Maßstäbe in Sachen Leistung und Sicherheit, wie der FIA-zertifizierte Überrollkäfig des Essenza SCV12 zeigt.
Die Partnerschaft von Lamborghini mit der University of Washington und Boeing hat das Know-how des Unternehmens weiter verfeinert und gewährleistet, dass die Supersportwagen von Lamborghini auch weiterhin an der Spitze der technischen Entwicklung stehen.
Wichtigste Erkenntnisse
Lamborghini leistete Pionierarbeit bei der Verwendung von Karbonfasern in Supersportwagen, beginnend mit dem Countach Evoluzione im Jahr 1983, der einen Standard für leichte und leistungsstarke Fahrzeuge setzte.
Die Einführung der Forged Composites-Technologie revolutionierte die Karbonfaserproduktion und ermöglichte eine schnellere Herstellung und eine einzigartige Ästhetik, die sowohl die Leistung als auch das Design verbesserte.
Nachhaltigkeit ist eine Priorität für Lamborghini. Die Bemühungen konzentrieren sich auf das Recycling von Materialien und die Reduzierung des Energieverbrauchs, um die Innovationen mit den globalen Umweltzielen in Einklang zu bringen.
Lamborghinis Carbonfaser-Innovationen verbessern die Leistung des Fahrzeugs, einschließlich der Beschleunigung und des Fahrverhaltens, und erhöhen gleichzeitig die Sicherheit durch überlegene Crash-Resistenz.
Die Individualisierungsoptionen für Kohlefaserelemente ermöglichen es Lamborghini-Besitzern, ihre Fahrzeuge zu personalisieren und Luxus mit modernster Technologie zu kombinieren.
Lamborghinis Geschichte mit Kohlefaser
Frühe Annahme und Meilensteine
Der Countach Evoluzione und die erste Verwendung von Kohlefaser
Der Weg von Lamborghini zur Kohlefaser geht auf das Jahr 1983 zurück, als das Unternehmen in Zusammenarbeit mit Boeing die Abteilung Esperienza Materiali Compositi gründete. Dies markierte den Beginn der Erforschung leichter Materialien. Der Countach Evoluzione, ein Prototyp, der als Prüfstand für neue Technologien entwickelt wurde, war der erste Lamborghini, der mit Kohlefaser ausgestattet war. Der Countach Evoluzione verwendete fortschrittliche Materialien wie Kevlar und Kohlefaser und setzte damit einen Präzedenzfall für zukünftige Supersportwagen. Diese Innovation demonstrierte das Engagement von Lamborghini, die Grenzen des Automobilbaus zu erweitern.
Lamborghinis Engagement für leichte Materialien seit den 1980er Jahren
Seit den 1980er Jahren setzt Lamborghini konsequent auf leichte Materialien. Zu den wichtigsten Meilensteinen gehören:
1983: Der Prototyp des Countach Evoluzione führte die Kohlefaser in die Designphilosophie von Lamborghini ein.
2007: Eine Partnerschaft mit der University of Washington hat die Verbundstofftechnologie weiterentwickelt und den Weg für das Monocoque des Aventador geebnet.
2008: Die Zusammenarbeit mit Boeing führte zu bahnbrechenden Forschungen über das Crashverhalten von Verbundwerkstoffen.
2011: Der Aventador LP 700-4 debütiert mit einem Kohlefaser-Monocoque, das nur 229,5 kg wiegt und Lamborghinis Kompetenz im Leichtbau unter Beweis stellt.
Diese Meilensteine verdeutlichen, wie Lamborghini mit seinen Carbonfaser-Innovationen die Leistungs- und Sicherheitsstandards in der Supersportwagenbranche immer wieder neu definiert hat.
Einrichtung des Labors für fortgeschrittene Verbundwerkstoff-Strukturen (ACSL)
Die Rolle von ACSL bei der Pionierarbeit in der Kohlenstofffaserforschung
Lamborghini gründete das Advanced Composite Structures Laboratory (ACSL), um die Forschung im Bereich der Leichtbauwerkstoffe zu leiten. Diese Einrichtung mit Sitz in Seattle konzentriert sich auf die Entwicklung von Spitzentechnologien wie geschmiedeten Verbundwerkstoffen. Durch die Zusammenarbeit mit Boeing ist das ACSL zu einem Zentrum für Innovationen geworden, das sicherstellt, dass Lamborghini bei der Entwicklung von Kohlefasern an vorderster Front steht. Die Arbeit des Labors verbessert sowohl die Leistung als auch die Ästhetik der Supersportwagen von Lamborghini und festigt den Ruf des Unternehmens als führendes Unternehmen in der Materialwissenschaft.
Die wichtigsten Errungenschaften, darunter die Kohlefaserstruktur des Aventador
Das ACSL hat bemerkenswerte Meilensteine in der Kohlenstofffaserentwicklung erreicht. Zu den bemerkenswerten Errungenschaften gehören:
Entwicklung und Zertifizierung des Monocoques des Aventador mit von der Luft- und Raumfahrt inspirierten Methoden.
Entwicklung von Flüssigharz-Infusionsverfahren für die Herstellung außerhalb des Autoklaven.
Einführung der marmorierten Kohlefaserästhetik, wie sie in Modellen wie dem Sesto Elemento und dem Huracán Performante zu sehen ist.
Pionierarbeit im 3D-Druck für technische und künstlerische Prototypen.
Diese Innovationen haben die Lamborghini Kohlefasertechnologie verbessert und die Entwicklung von Supercars ermöglicht, die leichter, stärker und optisch beeindruckender sind.
Die wichtigsten Innovationen in der Lamborghini Kohlefasertechnologie
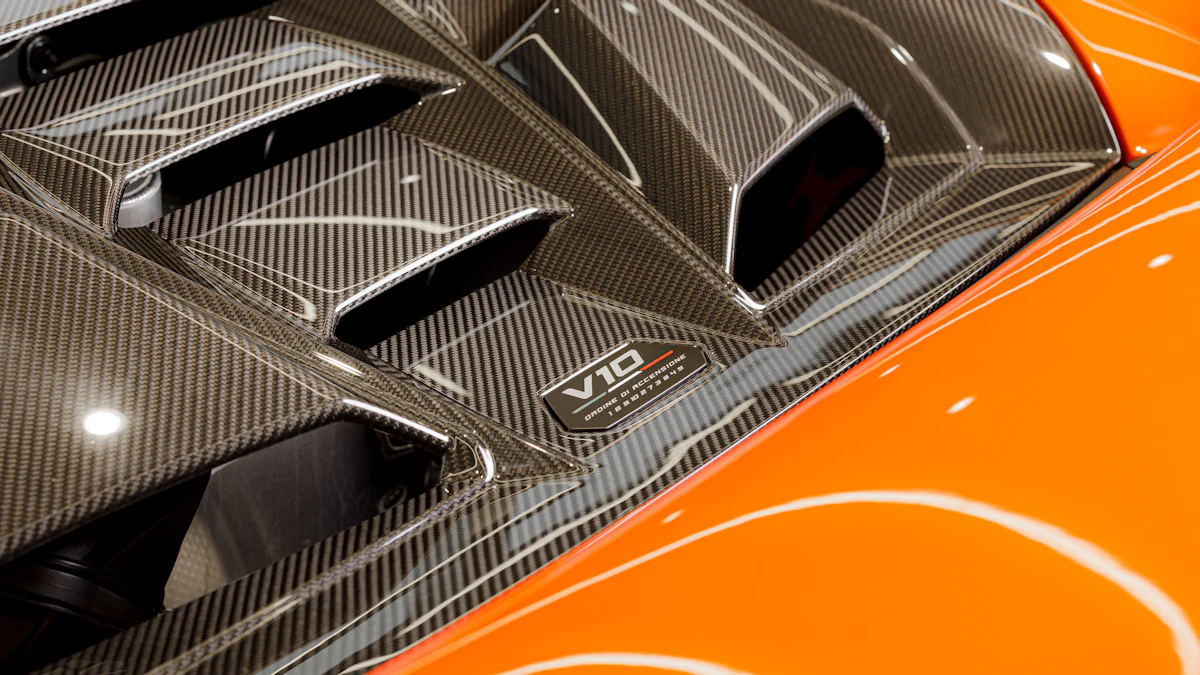
Technologie für geschmiedete Verbundwerkstoffe
Wie Forged Composites die Verwendung von Kohlenstofffasern revolutioniert hat
Die Forged Composites-Technologie stellt einen bahnbrechenden Wandel in der Nutzung von Kohlenstofffasern dar. Im Gegensatz zu herkömmlichen Methoden, die auf geschichteten und gewebten Fasern beruhen, werden bei diesem Verfahren Millionen winziger Kohlenstofffasern zu einer festen Struktur verdichtet. Dieser innovative Ansatz macht ein präzises Schneiden und Verlegen der Materialien überflüssig, was die Produktion schneller und effizienter macht. Jedes mit Forged Composites hergestellte Bauteil weist aufgrund der zufälligen Ausrichtung der Fasern eine einzigartige Ästhetik auf, die sich von den gleichmäßigen Mustern herkömmlicher Kohlenstofffasern abhebt.
Merkmal | Technologie für geschmiedete Verbundwerkstoffe | Traditionelle Kohlenstofffaser-Methoden |
---|---|---|
Faserausrichtung | Zufällig orientierte Fasern | Geschichtete und gewebte Fasern |
Herstellungsprozess | Hergestellt aus einer Paste oder winzigen gehackten Fasern | Geschichtet und geformt |
Ästhetische Variation | Jedes Produkt ist aufgrund der zufälligen Ausrichtung einzigartig | Konsistente Muster aufgrund der gewebten Struktur |
Vorteile bei Festigkeit, Gewicht und Produktionseffizienz
Forged Composites bietet außergewöhnliche Vorteile in mehreren Dimensionen:
Stärke: Sein hohes Verhältnis von Festigkeit zu Gewicht verbessert die Haltbarkeit und Widerstandsfähigkeit.
Gewichtsreduzierung: Das geringe Gewicht verbessert die Leistung und die Kraftstoffeffizienz.
Produktionseffizienz: Das Formpressen reduziert die Produktionszeit und die Kosten.
Schlagzähigkeit: Sie absorbiert und zerstreut die Energie wirksam und erhöht die Sicherheit.
Korrosionsbeständigkeit: Das Material ist widerstandsfähig gegen Umwelteinflüsse und hat eine lange Lebensdauer.
Diese Vorteile machen die geschmiedeten Verbundwerkstoffe zu einem Eckpfeiler der technischen Spitzenleistungen von Lamborghini.
Proprietäre Herstellungsverfahren
Lamborghinis einzigartige Methoden zur Herstellung von Kohlenstofffasern
Lamborghini hat eigene Verfahren zur Rationalisierung der Kohlefaserproduktion entwickelt. Die RTM-Lambo-Technologie des Unternehmens, die in Zusammenarbeit mit der University of Washington entwickelt wurde, macht die manuelle Laminierung und Autoklaven überflüssig. Diese Innovation verkürzt die Produktionszeit erheblich und erhält gleichzeitig die strukturelle Integrität der Bauteile. Darüber hinaus werden bei Lamborghinis Forged Composite-Verfahren kurze Kohlefaserstränge mit unausgehärtetem Kunststoff gemischt, der dann in Formen gepresst wird. Mit dieser Methode werden Teile hergestellt, die genauso leicht und steif sind wie herkömmlich hergestellte Kohlefaserkomponenten, jedoch in einem Bruchteil der Zeit.
Integration von Automatisierung und Feinmechanik
Sie profitieren von Lamborghinis Integration von Automatisierung und Präzisionstechnik in die Carbonfaserproduktion. Durch die Behandlung von Kohlefaser ähnlich wie bei Metallen und Kunststoffen erreicht Lamborghini schnellere Produktionszyklen ohne Qualitätseinbußen. Der Revuelto verfügt beispielsweise über eine vollständig aus Kohlefaser bestehende Frontstruktur, die die Energieabsorption verbessert und das Gewicht reduziert. Dieser Ansatz stellt sicher, dass die Lamborghini-Carbonfaser-Innovationen in Bezug auf Leistung und Effizienz weiterhin führend in der Branche sind.
Nachhaltigkeit bei der Entwicklung von Kohlenstofffasern
Verringerung von Abfall und Umweltbelastung
Lamborghini legt bei der Entwicklung von Carbonfasern größten Wert auf Nachhaltigkeit. Das Unternehmen konzentriert sich auf das Recycling aller Verbundwerkstoffe und die Reduzierung des Energieverbrauchs bei der Produktion. Abfälle werden für andere Anwendungen, wie Fahrzeugkomponenten oder Werbeartikel, wiederverwendet. Diese Bemühungen minimieren die Umweltauswirkungen und maximieren gleichzeitig die Ressourceneffizienz.
Schritt | Beschreibung |
---|---|
1 | Schwerpunkt auf Nachhaltigkeit und Abfallrecycling. |
2 | Senkung des Energieverbrauchs in Produktionsprozessen. |
3 | Wiederverwendung von Verbundwerkstoffabfällen in anderen Anwendungen. |
Künftige Ziele für nachhaltige Materialinnovationen
Lamborghini strebt eine kreislauforientierte Nachhaltigkeit in der Kohlefaserproduktion an. Das Unternehmen hat Technologien eingeführt, die den Energie- und Wasserverbrauch minimieren. Darüber hinaus erforscht Lamborghini neue Materialien, die leichter, haltbarer und umweltfreundlicher sind. Diese Fortschritte verbessern nicht nur die Leistung der Supersportwagen, sondern stehen auch im Einklang mit den globalen Nachhaltigkeitszielen.
Anwendungen von Lamborghini Carbon Fiber in Supersportwagen
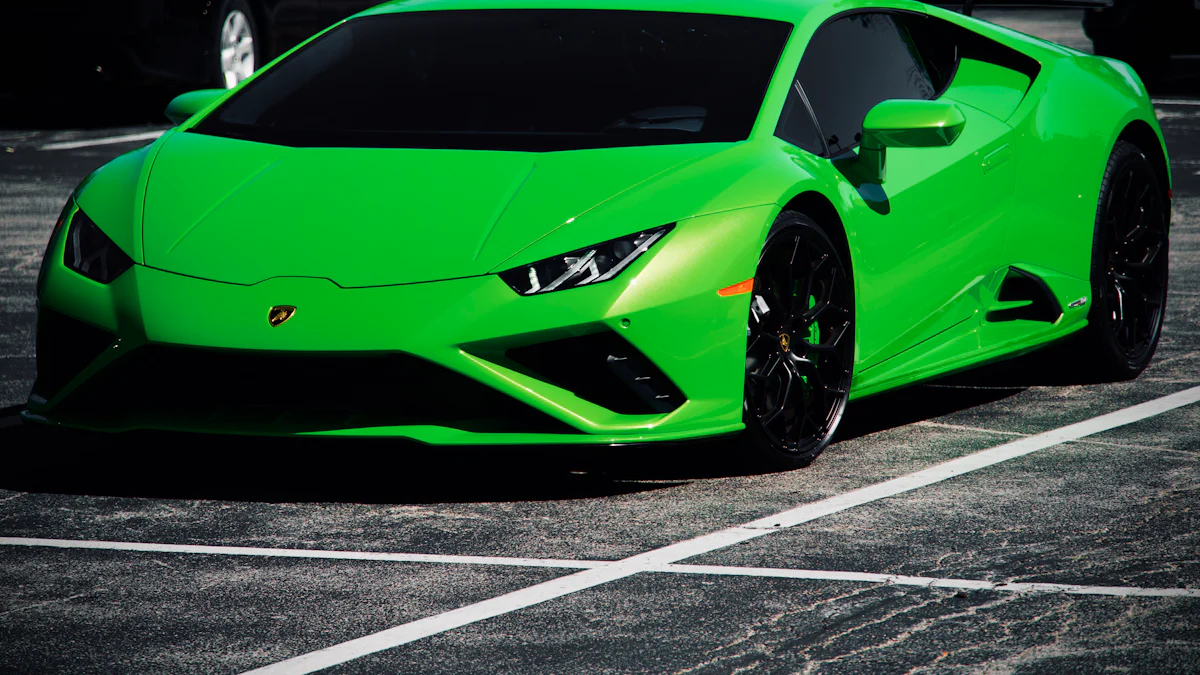
Strukturelle Komponenten
Monocoque-Chassis aus Kohlefaser für Steifigkeit und Sicherheit
Lamborghini hat mit der Verwendung von Karbonfasern für Strukturkomponenten die Konstruktion von Supersportwagen neu definiert. Das Kohlefaser-Monocoque-Chassis, das erstmals im Aventador LP 700-4 eingeführt wurde, ist ein Paradebeispiel dafür. Mit einem Gewicht von nur 324 Pfund maximiert diese einschalige Struktur die Steifigkeit und minimiert gleichzeitig das Gewicht. Ihr Design verbessert das Handling, die Beschleunigung und die Gesamtleistung. Darüber hinaus erhöht die Integration von Epoxidschaum-Komponenten in das Monocoque die Steifigkeit und reduziert Geräusche und Vibrationen, wodurch ein überragendes Fahrerlebnis gewährleistet wird. Die von Lamborghini entwickelte Forged Composite Technologie optimiert die Produktion dieser Komponenten und sorgt für eine hohe Festigkeit und Effizienz.
Beispiele von Modellen wie dem Aventador und Huracán
Die Kompetenz von Lamborghini zeigt sich in Modellen wie dem Aventador und dem Huracán. Das Kohlefaser-Monocoque des Aventador ist ein Beispiel für innovative Leichtbauweise, während der Huracán fortschrittliche Verbundwerkstoffe zur Verbesserung der strukturellen Integrität einsetzt. Der LB744 geht mit seinem vollständig aus Kohlefaser bestehenden Rumpf noch einen Schritt weiter und ist damit der erste Supersportwagen mit einem vollständig aus Kohlefaser bestehenden Vorderwagen. Diese Fortschritte unterstreichen das Engagement von Lamborghini für Sicherheit und Leistung.
Äußeres und aerodynamische Merkmale
Verwendung in Karosserieteilen, Spoilern und Diffusoren
Lamborghini verwendet Kohlefaser in großem Umfang für Außenkomponenten wie Karosserieteile, Spoiler und Diffusoren. Das geringe Gewicht von Carbonfasern verbessert die Geschwindigkeit und das Handling, was für Hochleistungsfahrzeuge entscheidend ist. Der Sesto Elemento beispielsweise verfügt über die Forged Composites-Technologie, die die Herstellung komplexer Formen zur Optimierung der Aerodynamik ermöglicht. Diese Innovation ermöglicht es Lamborghini, die Grenzen des Designs zu verschieben und gleichzeitig das Gewicht niedrig zu halten.
Komponente Beschreibung | Preisspanne |
---|---|
Heckspoiler Flügel | $880 – $2,460 |
Heckstoßstange & Diffusor | $1,380 – $5,260 |
Seitenschweller | $1,020+ |
Ganzkörper-Kit | $5,220+ |
Verbesserung der Aerodynamik und Verringerung des Luftwiderstands
Das Know-how von Lamborghini in Sachen Karbonfasern stellt sicher, dass jedes äußere Merkmal zur Leistung beiträgt. Das Advanced Composite Structures Laboratory konzentriert sich auf die Optimierung dieser Komponenten, um den Luftwiderstand zu reduzieren und den Abtrieb zu verbessern. Dieser Ansatz erhöht nicht nur die Geschwindigkeit, sondern sorgt auch für Stabilität bei hohen Geschwindigkeiten.
Innenraumgestaltung und Personalisierung
Leichte Karbonfaser-Akzente in der Kabine
Im Innenraum setzt Lamborghini leichte Kohlefaserakzente, um sowohl die Ästhetik als auch die Leistung zu verbessern. Die Entwicklung von Carbonskin, einer flexiblen Kohlenstoffmatrix, revolutionierte das Innendesign. Dieses Material ist leichter als herkömmliche Materialien wie Leder und reduziert das Gesamtgewicht des Fahrzeugs. Die aus hochwertiger Karbonfaser gefertigten Verkleidungen verbessern die Agilität und Reaktionsfähigkeit und sorgen gleichzeitig für ein luxuriöses Gefühl.
Personalisierungsoptionen für Kunden
Lamborghini bietet umfangreiche Individualisierungsmöglichkeiten für die Karbonfaserelemente im Innenraum. Sie können aus verschiedenen Oberflächen und Webmustern wählen, wie z. B. matt oder glänzend, um Ihren persönlichen Stil anzupassen. Diese Optionen ermöglichen es Ihnen, ein einzigartiges und exklusives Interieur zu schaffen, das das Design des Fahrzeugs ergänzt.
Vorteile der Lamborghini Carbonfaser-Innovationen
Verbesserte Leistung
Verbesserte Beschleunigung, Handhabung und Höchstgeschwindigkeit
Die Verwendung von Karbonfasern durch Lamborghini steigert direkt die Leistung seiner Supersportwagen. Das geringe Gewicht und die aerodynamischen Eigenschaften von Carbonfasern ermöglichen eine schnellere Beschleunigung und ein besseres Handling. Zum Beispiel:
Das Kohlefaser-Monocoque des Aventador wiegt nur 147,5 kg, wodurch er eine Höchstgeschwindigkeit von 350 km/h erreicht. Er beschleunigt von 0 auf 100 km/h in nur 2,9 Sekunden.
Der Sesto Elemento ist 250 Kilogramm leichter als herkömmliche Modelle und bietet eine unübertroffene Agilität und Reaktionsfähigkeit.
Diese Innovationen sorgen dafür, dass Lamborghini-Supersportwagen auch weiterhin an der Spitze von Geschwindigkeit und Präzision stehen.
Leistungskennzahlen durch Carbonfaser erreicht
Die Lamborghini Kohlefasertechnologie erreicht bemerkenswerte Leistungsdaten. Die Monocoque-Struktur des Aventador wiegt nur 506 Pfund, was zu seiner außergewöhnlichen Geschwindigkeit und Handhabung beiträgt. Der Essenza SCV12 verfügt über einen Überrollkäfig aus Kohlefaser, der für eine Kraft von 12 Tonnen zertifiziert ist und Sicherheit ohne Leistungseinbußen gewährleistet. Der Sesto Elemento, dessen Chassis zu 75% aus CFK gefertigt ist, wiegt nur 999 Kilogramm und zeigt das Potenzial von Verbundwerkstoffen, den Bau von Supersportwagen neu zu definieren.
Gewichtsreduzierung
Bedeutung von Leichtbauwerkstoffen für die Konstruktion von Supersportwagen
Leichte Materialien wie Kohlefaser sind für die Konstruktion von Supersportwagen unerlässlich. Sie verbessern die Geschwindigkeit, die Kraftstoffeffizienz und die Sicherheit. Durch die Gewichtsreduzierung benötigen Lamborghini-Supercars weniger Energie für den Antrieb, was die Gesamtleistung verbessert. Die Vielseitigkeit von Karbonfasern ermöglicht außerdem innovative Designs, die Funktionalität und Ästhetik miteinander verbinden.
Wie Gewichtsreduzierung die Kraftstoffeffizienz und Agilität verbessert
Die Gewichtsreduzierung spielt eine entscheidende Rolle bei der Verbesserung der Kraftstoffeffizienz und Agilität. Zum Beispiel:
Die Leichtbauweise des Sesto Elemento verbessert die Beschleunigung und das Handling und macht ihn auf der Straße noch agiler.
Ein geringeres Gewicht bedeutet, dass weniger Leistung benötigt wird, was zu einem niedrigeren Kraftstoffverbrauch und einer Reduzierung der CO2-Emissionen um 20% führt.
Diese Fortschritte stellen sicher, dass Lamborghini-Supersportwagen sowohl aufregende Leistung als auch Umweltfreundlichkeit bieten.
Langlebigkeit und Sicherheit
Das Verhältnis von Festigkeit zu Gewicht und die Widerstandsfähigkeit von Carbonfasern bei Unfällen
Kohlefaser bietet ein außergewöhnliches Verhältnis zwischen Festigkeit und Gewicht und ist daher ideal für den Bau von Supersportwagen. Sie absorbiert Energie, indem sie bei Kollisionen bricht und so die auf den Innenraum übertragene Aufprallenergie reduziert. Zum Beispiel:
Das Kohlefaser-Monocoque des Aventador wiegt nur 506 Pfund, was sowohl die Festigkeit als auch die Crashsicherheit erhöht.
Crashtests zeigen, dass Kohlefaser die Aufprallenergie effektiv absorbiert und so die Sicherheit der Passagiere gewährleistet.
Die einzigartigen Eigenschaften dieses Materials bieten Ihnen ein sichereres Fahrerlebnis, ohne dass Sie Kompromisse bei der Leistung eingehen müssen.
Praktische Beispiele für Sicherheitsvorteile in Lamborghini-Modellen
Lamborghini-Supersportwagen demonstrieren die Sicherheitsvorteile von Karbonfasern in der Praxis.
Der Essenza SCV12 verfügt über den weltweit ersten FIA-zertifizierten Überrollkäfig aus Kohlefaser, der einer Kraft von 12 Tonnen standhalten kann. Diese Innovation sorgt für mehr Sicherheit in Situationen mit hohem Aufprall.
Das Kohlefaser-Monocoque wurde mehr als 20 statischen Tests unterzogen, einschließlich dynamischer Crashtests mit Geschwindigkeiten von bis zu 14 Metern/Sekunde, um hohe Sicherheitsstandards zu gewährleisten.
Diese Beispiele verdeutlichen das Engagement von Lamborghini, Sie zu schützen und gleichzeitig eine unvergleichliche Leistung zu bieten.
Wie Lamborghini sich bei der Karbonfaser-Innovation abhebt
Führend in der Industrie
Der Einfluss von Lamborghini auf die Verwendung von Kohlefasern in der Automobilindustrie
Die führende Rolle von Lamborghini im Bereich der Kohlefaserinnovation zeigt sich in den bahnbrechenden Beiträgen des Unternehmens zur Automobilindustrie. 1983 gründete Lamborghini in Zusammenarbeit mit Boeing die Abteilung Esperienza Materiali Compositi, die zur Entwicklung des Countach Evoluzione führte, dem ersten Prototyp eines Straßenfahrzeugs mit Kohlefaserchassis. Diese frühe Einführung legte den Grundstein für jahrzehntelange Weiterentwicklungen. Im Jahr 2007 ging Lamborghini eine Partnerschaft mit der University of Washington ein, um die RTM-Technologie zu entwickeln, die in das Monocoque des Aventador integriert wurde. Die Einführung der Forged Composites-Technologie im Jahr 2009 revolutionierte die Kohlefaserherstellung weiter und ermöglichte eine schnellere Produktion und größere Designflexibilität.
Auszeichnungen und Anerkennung für Materialinnovationen
Die Errungenschaften von Lamborghini im Bereich der Kohlenstofffasern haben weltweite Anerkennung gefunden. Auf der JEC Composites Exhibition 2016 erhielt Lamborghini den Innovation Award für sein Kohlefaserpaket, das für den Huracán entwickelt wurde. Diese Auszeichnung unterstreicht das Engagement von Lamborghini, die Grenzen der Materialwissenschaft und der technischen Exzellenz zu erweitern.
Auszeichnung | Jahr | Veranstaltung | Beschreibung |
---|---|---|---|
Innovationspreis | 2016 | JEC Composites Ausstellung | Anerkannt für das Kohlefaserpaket, das für den Lamborghini Huracán entwickelt wurde. |
Vergleich mit Wettbewerbern
Wie Lamborghinis Kohlefasertechnologie die Konkurrenz übertrifft
Die Kohlefasertechnologie von Lamborghini ist der Konkurrenz stets voraus. Die Partnerschaft des Unternehmens mit der University of Washington führte zur Entwicklung des Harztransferpressens außerhalb des Autoklavs, einem Verfahren, das die Effizienz und Präzision erhöht. Im Gegensatz zu herkömmlichen Methoden werden mit dem Forged Composite-Verfahren von Lamborghini leichte und stabile Komponenten in Minuten statt in Stunden hergestellt. Diese Innovation ermöglicht Ihnen den Zugang zu Supersportwagen, die nicht nur schneller, sondern auch haltbarer sind.
Einzigartige Merkmale, die Lamborghini auszeichnen
Lamborghinis Umgang mit Karbonfasern ist unübertroffen. Der Sesto Elemento zum Beispiel ist ein Beispiel für den umfassenden Einsatz von Verbundwerkstoffen, der zu einem Fahrzeug führt, das sowohl leicht als auch unglaublich agil ist. Das von Lamborghini entwickelte Forged Composite-Material, das aus zufällig orientierten Kohlenstofffasern besteht, ermöglicht eine schnellere Produktion ohne Leistungseinbußen. Diese Fortschritte stellen sicher, dass Lamborghini Carbonfasern als Maßstab in der Industrie beibehält.
Vision für die Zukunft
Kohlenstofffaseranwendungen der nächsten Generation
Lamborghini erforscht weiterhin neue Grenzen der Kohlefasertechnologie. Im Jahr 2019 testete das Unternehmen Verbundwerkstoffe im Weltraum, um ihre Leistung unter extremen Bedingungen zu bewerten. Diese Experimente ebnen den Weg für künftige Anwendungen in den Bereichen Automobil und Medizin. Das 2016 gegründete Lamborghini Advanced Composite Structures Laboratory bleibt an der Spitze der Forschung und stellt sicher, dass Sie von den neuesten Innovationen in der Materialwissenschaft profitieren.
Die Rolle der Kohlefaser in den Hybrid- und Elektro-Supercars von Lamborghini
Kohlefaser spielt eine zentrale Rolle beim Übergang von Lamborghini zu Hybrid- und Elektro-Supersportwagen. Der LB744 verfügt über einen von der Luftfahrt inspirierten Monofaser-Rumpfrahmen, der die Festigkeit und Torsionssteifigkeit erhöht und gleichzeitig das Gewicht reduziert. Auch der Revuelto verfügt über ein Kohlefaser-Monocoque-Chassis, das sowohl die Leistung als auch die Kraftstoffeffizienz verbessert. Diese Fortschritte zeigen das Engagement von Lamborghini für Nachhaltigkeit und Spitzentechnologie.
Das Know-how von Lamborghini in der Kohlefasertechnologie hat die Supersportwagenbranche verändert. Sie profitieren von dem unermüdlichen Streben nach Innovation, das fortschrittliche Materialien, effiziente Fertigung und nachhaltige Praktiken kombiniert. Diese bahnbrechenden Neuerungen sorgen für unübertroffene Leistung, Exklusivität und Sicherheit in jedem Modell. Die Carbonfaser-Innovationen von Lamborghini setzen weiterhin Maßstäbe und prägen die Zukunft von Hochleistungsfahrzeugen. Da Lamborghini die Grenzen immer weiter hinausschiebt, können Sie davon ausgehen, dass ihre technischen Spitzenleistungen das Mögliche im Automobildesign neu definieren werden.
FAQ
Was macht die Kohlefasertechnologie von Lamborghini so einzigartig?
Lamborghini verwendet proprietäre Verfahren wie Forged Composites und RTM-Lambo-Technologie. Diese Verfahren verkürzen die Produktionszeit bei gleichbleibender Festigkeit und Präzision. Sie profitieren von leichten, langlebigen Komponenten, die Leistung und Sicherheit verbessern.
Wie verbessert Kohlefaser die Leistung von Lamborghini-Supercars?
Kohlefaser reduziert das Gewicht und verbessert die Beschleunigung, das Handling und die Höchstgeschwindigkeit. Das Verhältnis von Festigkeit zu Gewicht verbessert die strukturelle Steifigkeit und die Crash-Resistenz. Sie erleben mehr Agilität und Sicherheit, ohne auf Luxus oder Design verzichten zu müssen.
Ist die Kohlefaserproduktion von Lamborghini nachhaltig?
Ja, Lamborghini legt Wert auf Nachhaltigkeit, indem es Verbundwerkstoffe recycelt und den Energieverbrauch reduziert. Abfallmaterialien werden wiederverwendet, und das Unternehmen erforscht umweltfreundliche Innovationen, um sich an den globalen Umweltzielen zu orientieren.
Welche Lamborghini-Modelle weisen Innovationen aus Kohlefaser auf?
Modelle wie der Aventador, Huracán und Sesto Elemento sind Beispiele für die Verwendung von Kohlefaser. Der LB744 verfügt über einen vollständig aus Kohlefaser gefertigten Rumpf und setzt damit neue Maßstäbe in Sachen Leichtbau und Leistung.
Kann man Kohlefaserelemente in einem Lamborghini individuell gestalten?
Ganz genau. Lamborghini bietet Individualisierungsoptionen für Innen- und Außenkomponenten aus Kohlefaser. Sie können Oberflächen, Muster und Akzente wählen, um ein individuelles, exklusives Design zu schaffen.