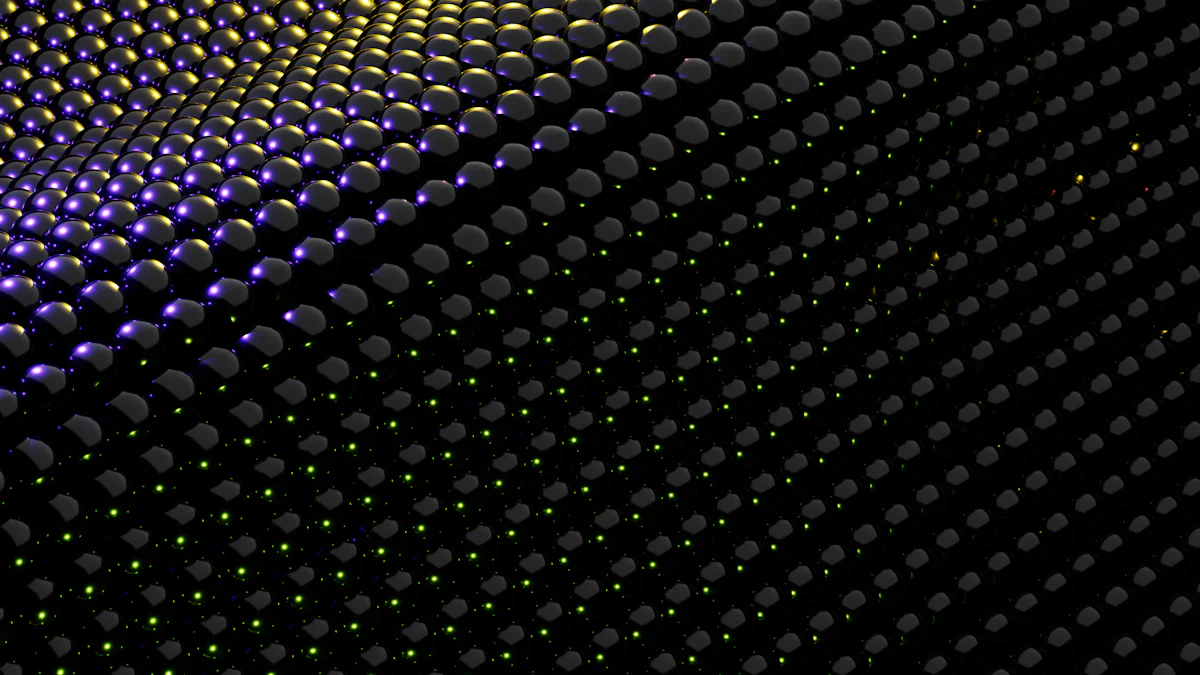
Trockene Kohlenstofffasern sind ein revolutionäres Material, das aus vorimprägnierten Kohlenstoffplatten hergestellt wird. Seine einzigartige Zusammensetzung gewährleistet eine außergewöhnliche Festigkeit und ein geringes Gewicht, was es in Branchen wie der Automobil- und Luftfahrtindustrie unverzichtbar macht. Automobilhersteller verwenden sie beispielsweise, um das Gewicht von Fahrzeugen um bis zu 50% zu reduzieren und so die Kraftstoffeffizienz und Leistung erheblich zu verbessern. Bei der Herstellung von Trockenkohle liegt der Schwerpunkt auf Präzision, um eine gleichmäßige Harzverteilung und Faserausrichtung zu gewährleisten. Dieser sorgfältige Ansatz führt zu einem Material, das herkömmliche Alternativen in Bezug auf Qualität und Zuverlässigkeit übertrifft und den Anforderungen modernster Anwendungen gerecht wird.
Wichtigste Erkenntnisse
Trockene Kohlefaser ist ein leichtes und starkes Material, das sich ideal für Hochleistungsanwendungen in Branchen wie der Automobil- und Luftfahrtindustrie eignet.
Bei der Herstellung von Trockenkohle liegt der Schwerpunkt auf Präzision, um eine gleichmäßige Harzverteilung und Faserausrichtung zu gewährleisten und so eine hervorragende Qualität zu erzielen.
Die Verwendung von vorimprägnierten Materialien (Pre-Pregs) ermöglicht eine bessere Harzkontrolle, reduziert den Abfall und verbessert die mechanischen Eigenschaften des Endprodukts.
Das Aushärtungsverfahren im Autoklaven verfestigt den trockenen Kohlenstoff durch Anwendung von Hitze und Druck, was zu einer makellosen Oberfläche und verbesserter Haltbarkeit führt.
Das außergewöhnliche Verhältnis zwischen Festigkeit und Gewicht von trockenem Kohlenstoff ermöglicht die Konstruktion von Bauteilen, die die Kraftstoffeffizienz und Leistung von Fahrzeugen und Flugzeugen verbessern.
Die Wahl von trockenen Kohlenstofffasern unterstützt nachhaltige Herstellungspraktiken, indem sie den Materialabfall minimiert und die Umweltbelastung reduziert.
Fortgeschrittene Techniken wie das Wickeln von Filamenten ermöglichen die Herstellung spezieller Strukturen, die genau den Anforderungen von Hochleistungsanwendungen entsprechen.
Was ist trockene Kohlefaser?
Definition und einzigartige Eigenschaften
Trockene Kohlenstofffasern sind ein hochmodernes Material, das für seine Stärke, sein geringes Gewicht und seine Präzision bekannt ist. Im Gegensatz zu herkömmlichen Materialien wird es aus vorimprägnierten Kohlenstoffplatten hergestellt, bei denen das Harz vor dem Aushärten gleichmäßig auf den Fasern verteilt wird. Dies gewährleistet eine gleichmäßige Struktur ohne Unregelmäßigkeiten und verbessert die mechanischen Eigenschaften.
Eine der herausragenden Eigenschaften von trockenem Kohlenstoff ist die Fähigkeit, einen höheren Faservolumenanteil zu erreichen. Das bedeutet, dass mehr Kohlenstofffasern in das Material gepackt werden, was zu einer höheren Steifigkeit, Festigkeit und Ermüdungsbeständigkeit führt. Außerdem wird durch die kontrollierte Harzimprägnierung der Abfall auf ein Minimum reduziert, was das Material zu einer umweltbewussten Wahl macht. Branchen wie die Luft- und Raumfahrt und die Automobilindustrie nutzen diese einzigartigen Eigenschaften, um Bauteile herzustellen, bei denen sowohl Haltbarkeit als auch geringes Gewicht gefragt sind.
Unterschiede zwischen trockener und nasser Kohlefaser
Der Hauptunterschied zwischen trockenen und nassen Kohlenstofffasern liegt in den Herstellungsverfahren. Bei trockenen Kohlenstofffasern werden vorimprägnierte Materialien verwendet, die oft als "Pre-Preg" bezeichnet werden, bei denen das Harz bereits in das Kohlenstoffgewebe eingearbeitet ist. Diese Methode gewährleistet eine präzise Kontrolle des Harzes und macht die manuelle Aufbringung überflüssig. Im Gegensatz dazu wird bei Nasskohle das Harz während der Produktion manuell auf die Kohlefaserplatten aufgetragen, was zu einer ungleichmäßigen Verteilung und schwächeren strukturellen Integrität führen kann.
Trockener Kohlenstoff wird in einem Autoklaven, einer Hochdruck- und Hochtemperaturkammer, ausgehärtet. Durch diesen Prozess wird das Material gestärkt und alle Unvollkommenheiten werden beseitigt. Nasskohle hingegen härtet bei Raumtemperatur oder unter weniger kontrollierten Bedingungen aus, wodurch ein dickeres und weniger feines Produkt entsteht. Der komplizierte Prozess der Herstellung von Trockenkohle macht sie dünner, leichter und fester als ihr nasses Gegenstück. Diese Eigenschaften machen Trockenkohle zur bevorzugten Wahl für Hochleistungsanwendungen.
Materialien, die bei der Herstellung von trockenen Kohlenstofffasern verwendet werden
Vorläufer für Kohlenstofffasern
Der Weg zur Herstellung von trockenem Kohlenstoff beginnt mit der Auswahl des richtigen Vorprodukts. Ein Precursor dient als Ausgangsmaterial für die Herstellung von Kohlenstofffasern. Polyacrylnitril (PAN) ist das am häufigsten verwendete Vorprodukt, da es sehr leistungsfähige Ergebnisse liefert. PAN wird einem Prozess namens Karbonisierung unterzogen, bei dem es bei extrem hohen Temperaturen in einer sauerstofffreien Umgebung erhitzt wird. In diesem Schritt wird das Ausgangsmaterial in reine Kohlenstofffasern umgewandelt, die das Rückgrat des trockenen Kohlenstoffs bilden.
Andere Ausgangsstoffe wie Rayon und Pech wurden ebenfalls erforscht. Rayon war eines der ersten Materialien, das zur Herstellung von Kohlenstofffasern verwendet wurde, während Pech eine kostengünstige Alternative darstellt. Aufgrund seiner überlegenen mechanischen Eigenschaften bleibt PAN jedoch der Industriestandard. Die Wahl des Vorprodukts wirkt sich direkt auf die Festigkeit, Steifigkeit und Haltbarkeit des Endprodukts aus. Durch die sorgfältige Auswahl und Verarbeitung dieser Materialien stellen die Hersteller sicher, dass die Kohlenstofffasern den strengen Anforderungen von Branchen wie der Luft- und Raumfahrt oder der Automobilindustrie gerecht werden.
Vorimprägnierte Materialien und Harzsysteme
Vorimprägnierte Materialien, so genannte Pre-Pregs, spielen bei der Herstellung von Trockenkohle eine entscheidende Rolle. Diese Materialien bestehen aus Kohlenstofffaserplatten oder -geweben, die mit Harz vorimprägniert sind. Das Harz wird gleichmäßig über die Fasern verteilt, so dass es bei der Herstellung nicht mehr manuell aufgetragen werden muss. Dies gewährleistet eine gleichmäßige Struktur des Materials und verbessert seine Gesamtqualität.
Die in Prepregs verwendeten Harzsysteme sind speziell formuliert, um eine optimale Leistung zu erzielen. Epoxidharze sind aufgrund ihrer hervorragenden Bindungseigenschaften und ihrer Beständigkeit gegen Umwelteinflüsse die häufigste Wahl. Während des Aushärtungsprozesses härtet das Harz aus, wodurch die Kohlenstofffasern miteinander verbunden werden und ein starker, leichter Verbundstoff entsteht.
Prepregs werden in einem Autoklaven, einer Hochdruck- und Hochtemperaturkammer, ausgehärtet. In diesem Schritt werden Verunreinigungen entfernt und das Material wird gestärkt. Der kontrollierte Harzgehalt in Pre-Pregs ermöglicht eine präzise Faserausrichtung, was zu einem dünneren und gleichmäßigeren Produkt führt. Dieser sorgfältige Prozess verbessert nicht nur die mechanischen Eigenschaften des Materials, sondern reduziert auch den Abfall, was Dry Carbon zu einer umweltfreundlichen Option macht.
Schritt-für-Schritt-Herstellungsprozess von Trockenkohle
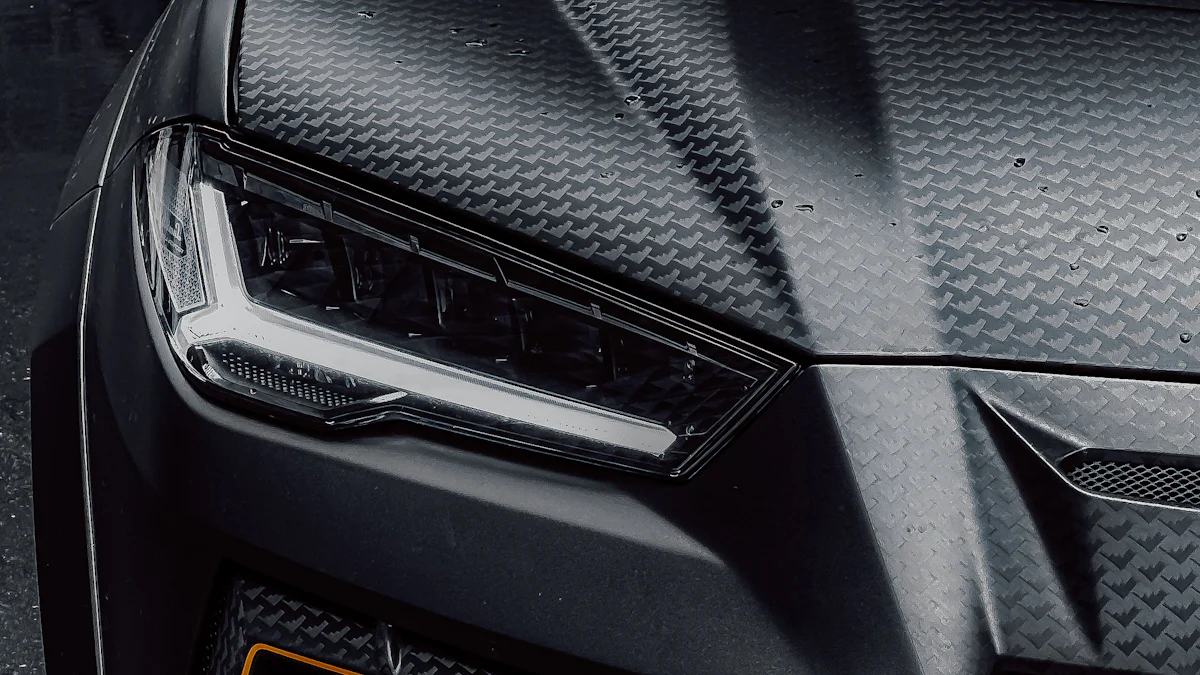
Schichtung von Kohlefaserplatten
Der Herstellungsprozess beginnt mit der Schichtung von Kohlenstofffaserplatten. Diese Platten, die oft als Trockenfasertextilien bezeichnet werden, kommen als Rollenware an. Automatisierte Schneidemaschinen, die von CAD-Daten gesteuert werden, schneiden das Gewebe präzise in bestimmte Formen. So wird sichergestellt, dass jede Lage perfekt in das endgültige Design passt. Anschließend stapeln Sie diese vorgeschnittenen Lagen in einer Form und richten sie sorgfältig aus, um die gewünschte Faserausrichtung zu erreichen. Die korrekte Ausrichtung ist von entscheidender Bedeutung, da sie sich direkt auf die Festigkeit und Steifigkeit des Endprodukts auswirkt. Indem Sie diesen Schritt kontrollieren, stellen Sie die strukturelle Integrität und Leistungsfähigkeit des Materials sicher.
Anwendung von Wärme und Druck
Sobald die Schichten aufgebracht sind, werden im nächsten Schritt Hitze und Druck angewendet. In dieser Phase wird das Harz in den vorimprägnierten Kohlenstoffplatten aktiviert. Das Harz, das bereits in die Fasern eingearbeitet ist, beginnt unter Hitzeeinwirkung zu erweichen. Der Druck sorgt dafür, dass die Schichten fest miteinander verbunden werden, so dass Lufteinschlüsse und Hohlräume vermieden werden. Durch die Kombination von Hitze und Druck entsteht eine gleichmäßige Struktur, die die mechanischen Eigenschaften des Materials verbessert. Sie müssen diesen Prozess genau überwachen, um die Konsistenz zu erhalten und Fehler zu vermeiden. Die Präzision dieses Arbeitsschritts unterscheidet Trockenkohle von anderen Materialien und gewährleistet höchste Qualität.
Aushärtung im Autoklaven
Der letzte Schritt ist das Aushärten des Materials in einem Autoklaven. Ein Autoklav funktioniert wie ein Hightech-Dampfkochtopf, in dem das Harz bei hohen Temperaturen und unter hohem Druck verfestigt wird. Während dieses Prozesses werden Verunreinigungen entfernt, und das Harz härtet aus und bindet die Kohlenstofffasern zusammen. Dieser Schritt stärkt nicht nur das Material, sondern sorgt auch für eine glatte, makellose Oberfläche. Die kontrollierte Umgebung des Autoklaven ermöglicht es Ihnen, die genauen Spezifikationen zu erreichen, die für Hochleistungsanwendungen erforderlich sind. Am Ende dieses Prozesses ist der trockene Kohlenstoff ein leichtes, haltbares und präzisionsgefertigtes Material, das sofort einsatzbereit ist.
Fortgeschrittene Techniken der trockenen Kohlenstofffaserproduktion
Pre-Preg-Verfahren zur Harzkontrolle
Das Pre-Preg-Verfahren ist ein Eckpfeiler bei der Herstellung von trockenem Kohlenstoff. Bei dieser Technik werden die Kohlenstofffaserplatten vor Beginn des Herstellungsprozesses mit Harz vorimprägniert. Mit dieser Methode lässt sich der Harzgehalt im Material genau steuern. Dadurch wird sichergestellt, dass das Harz gleichmäßig über die Fasern verteilt wird, wodurch Unregelmäßigkeiten, die das Endprodukt schwächen könnten, vermieden werden.
Vorimprägnierte Materialien werden strengen Qualitätskontrollen unterzogen, um ihre Einheitlichkeit zu gewährleisten. Die Hersteller lagern diese Materialien bei niedrigen Temperaturen, um ein vorzeitiges Aushärten zu verhindern. Bei der Verwendung von Prepregs kann ein höherer Faservolumenanteil erzielt werden, was sich direkt auf die Festigkeit und Steifigkeit des Materials auswirkt. Dieses Verfahren reduziert auch den Abfall, da die benötigte Harzmenge bereits in die Fasern eingearbeitet ist. Forschungsergebnissen zufolge verbessern optimierte Herstellungsverfahren wie das Vorimprägnieren nicht nur die mechanischen Eigenschaften von Trockenkohlenstoff, sondern senken auch die Produktionskosten, was sie zu einer nachhaltigen Wahl für die Industrie macht.
Filament Winding für spezielle Strukturen
Eine weitere fortschrittliche Technik bei der Herstellung von trockenem Kohlenstoff ist das Filament-Winding. Bei dieser Methode werden endlose Kohlenstofffasern um einen rotierenden Dorn gewickelt, um zylindrische oder rohrförmige Strukturen zu erzeugen. Sie können diese Technik zur Herstellung von Komponenten wie Druckbehältern, Rohren und Teilen für die Luft- und Raumfahrt verwenden, die eine hohe Festigkeit und Präzision erfordern.
Das Verfahren beginnt mit harzbeschichteten Kohlenstofffasern, die sorgfältig in bestimmten Mustern auf einen Dorn gewickelt werden. Die Ausrichtung der Fasern spielt eine entscheidende Rolle bei der Bestimmung der Festigkeit und Leistung des Endprodukts. Nach Abschluss der Wicklung wird die Struktur in einem Autoklaven ausgehärtet, um das Harz zu verfestigen und die Fasern miteinander zu verbinden.
Das Wickeln von Filamenten bietet mehrere Vorteile. Es ermöglicht die Herstellung leichter und dennoch haltbarer Strukturen mit minimalem Materialabfall. Durch die Möglichkeit, die Faserausrichtung individuell anzupassen, wird sichergestellt, dass das fertige Produkt genau den Anforderungen der jeweiligen Anwendung entspricht. Forscher haben diese Technik als eine Schlüsselinnovation in der Trockenkohlenstoffproduktion hervorgehoben, die die Herstellung von Spezialbauteilen für Hochleistungsindustrien ermöglicht.
Vorteile der Verwendung von trockenen Kohlenstofffasern
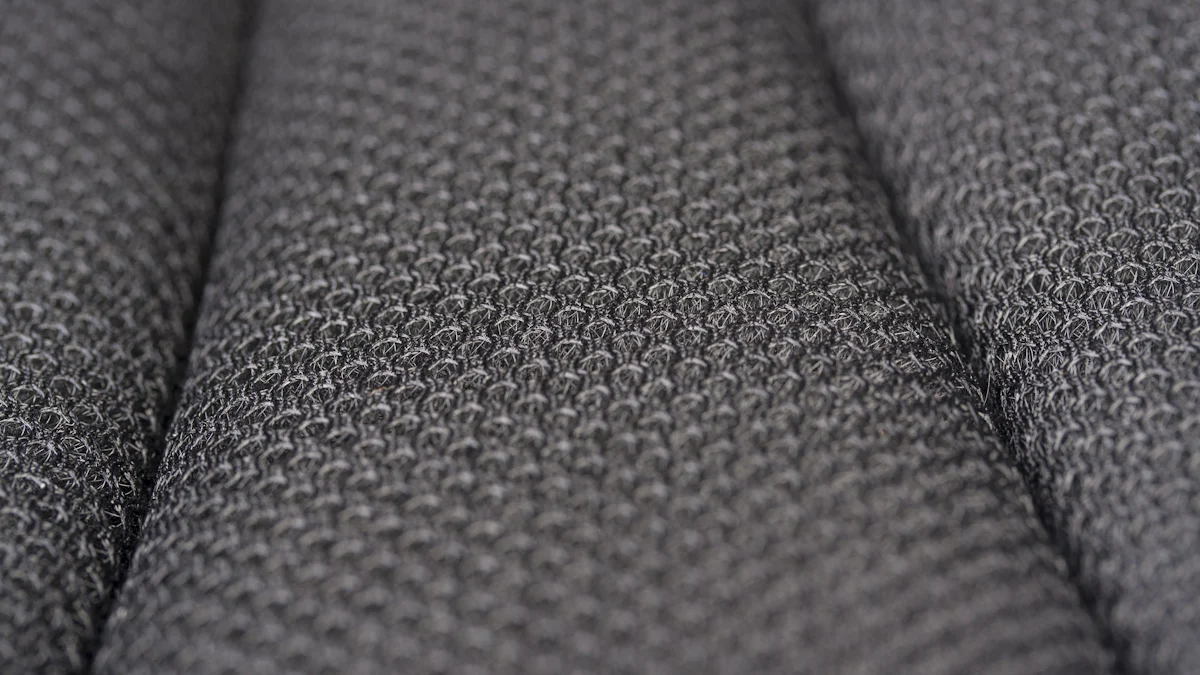
Hervorragendes Verhältnis von Stärke zu Gewicht
Trockener Kohlenstoff bietet ein außergewöhnliches Verhältnis zwischen Festigkeit und Gewicht, was ihn zu einem bevorzugten Material für Hochleistungsanwendungen macht. Sie erhalten ein Material, das unglaublich stark ist und gleichzeitig leicht bleibt. Diese Ausgewogenheit ermöglicht die Konstruktion von Bauteilen, die erheblichen Belastungen standhalten können, ohne unnötig an Gewicht zuzunehmen. In der Luft- und Raumfahrtindustrie beispielsweise führt eine Gewichtsreduzierung direkt zu einer verbesserten Treibstoffeffizienz und Leistung. Auch im Automobilbau hilft die Verwendung von trockenem Kohlenstoff bei der Entwicklung von Fahrzeugen, die schneller und wendiger sind.
Der hohe Faservolumenanteil von trockenem Kohlenstoff trägt zu seiner hervorragenden strukturellen Integrität bei. Indem Sie mehr Kohlenstofffasern in das Material packen, erreichen Sie eine höhere Steifigkeit und Verformungsbeständigkeit. Diese Eigenschaft sorgt dafür, dass das Material auch unter anspruchsvollen Bedingungen zuverlässig funktioniert. Ob Sie nun Flugzeugteile oder Komponenten für Sportwagen konstruieren, das Verhältnis von Festigkeit zu Gewicht von Dry Carbon verschafft Ihnen einen Wettbewerbsvorteil.
Verbesserte Langlebigkeit und Präzision
Trockenkohle zeichnet sich durch ihre Haltbarkeit und Präzision aus. Die kontrollierte Harzverteilung in vorimprägnierten Materialien gewährleistet eine gleichmäßige Struktur ohne Schwachstellen oder Unregelmäßigkeiten. Diese Präzision verbessert die mechanischen Eigenschaften des Materials, so dass Sie sich bei Anwendungen, die eine langfristige Leistung erfordern, auf dieses Material verlassen können. Aus trockenem Kohlenstoff hergestellte Bauteile sind selbst in rauen Umgebungen verschleißfest.
Die Aushärtung im Autoklaven stärkt das Material zusätzlich. Durch die Anwendung von Hitze und Druck werden Lufteinschlüsse und Unvollkommenheiten beseitigt, was zu einer makellosen Oberfläche führt. Dieser sorgfältige Prozess stellt sicher, dass jedes Stück Trockenkohle genau den Spezifikationen entspricht. Wenn Sie Trockenkohle verwenden, profitieren Sie von einem Material, das Langlebigkeit mit Präzision verbindet und sich daher ideal für Branchen wie die Luft- und Raumfahrt, die Automobilindustrie und die Sportgeräteherstellung eignet.
Weniger Materialabfall und geringere Umweltbelastung
Bei der Herstellung von Trockenkohle wird der Materialabfall minimiert, was sie zu einer umweltfreundlichen Wahl macht. Das Vorimprägnierverfahren gewährleistet eine präzise Harzkontrolle, reduziert überschüssiges Harz und verbessert die Verteilung. Diese Effizienz bedeutet, dass Sie nur die notwendige Menge an Material verwenden und Abfall vermeiden. Im Vergleich zu Nasslegeverfahren fällt bei der Herstellung von Trockenkohle deutlich weniger Abfall an, was zu einer nachhaltigen Produktionsweise beiträgt.
Wenn Sie sich für Trockenkohle entscheiden, reduzieren Sie auch die Umweltauswirkungen Ihrer Projekte. Die effiziente Nutzung von Materialien senkt nicht nur die Produktionskosten, sondern steht auch im Einklang mit umweltfreundlichen Zielen. Die Industrie legt zunehmend Wert auf Nachhaltigkeit, und Trockenkohle hilft Ihnen, diese Anforderungen zu erfüllen, ohne Kompromisse bei Qualität oder Leistung einzugehen. Die reduzierte Abfallmenge und die ressourceneffiziente Produktion machen sie zu einer verantwortungsvollen Wahl für die moderne Fertigung.
Der Prozess der Herstellung von Trockenkohle umfasst präzise Schritte, die eine außergewöhnliche Qualität gewährleisten. Von der Schichtung der Kohlefaserplatten bis zur Aushärtung im Autoklaven - jeder Schritt verbessert die Festigkeit und Haltbarkeit. Sie profitieren von einem Material, das aufgrund der aufwändigen Produktionsmethoden dünner, leichter und stärker ist als Nasskohle. Seine einzigartigen Eigenschaften, wie die hervorragende Harzkontrolle und das hohe Faservolumen, machen es ideal für anspruchsvolle Anwendungen. Mit der fortschreitenden Innovation in der Industrie wird sich die Rolle von Trockenkohlenstoff ausweiten und nachhaltige und leistungsstarke Lösungen für die Zukunft bieten.