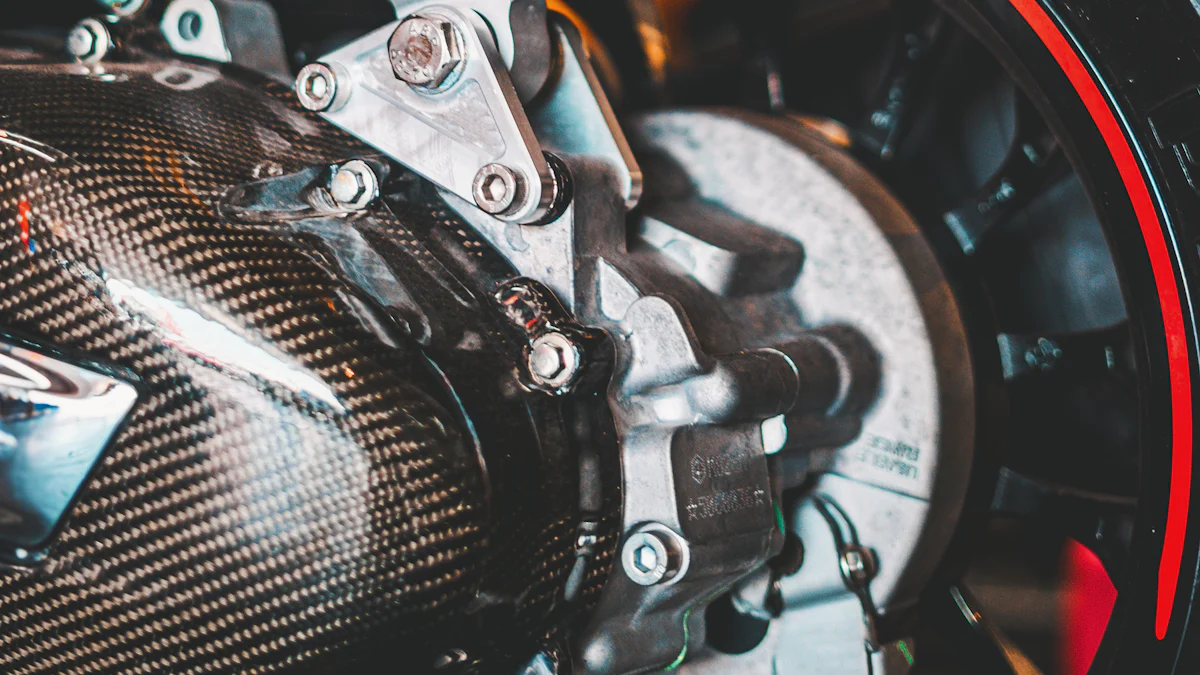
Have you ever wanted to create something lightweight, durable, and completely unique? A carbon fiber kit lets you do just that. With its incredible strength and sleek appearance, carbon fiber has become a favorite material for high-performance applications like aerospace and sports cars. Now, you can bring that same innovation into your DIY carbon fiber projects. Whether you want to make carbon fiber parts for your car, bike, or even custom tools, this material offers endless possibilities. It’s not just about functionality—it’s about crafting something that looks and feels professional. Ready to build your own carbon fiber masterpiece?
Wichtigste Erkenntnisse
Start with small projects to build confidence and familiarize yourself with carbon fiber techniques.
Gather essential materials like carbon fiber fabric, epoxy resin, and safety gear to ensure a smooth crafting process.
Always prioritize safety by wearing gloves, goggles, and a respirator when working with carbon fiber and resin.
Follow a step-by-step guide for mold preparation, fabric layering, and resin application to achieve professional results.
Practice proper curing techniques and workspace cleanliness to avoid imperfections in your final product.
Experiment with different fabric weaves and advanced techniques like vacuum bagging to enhance the quality of your projects.
Finish your parts with sanding, polishing, and a clear coat for a sleek, durable, and professional appearance.
Materials and Tools Needed for DIY Carbon Fiber Projects
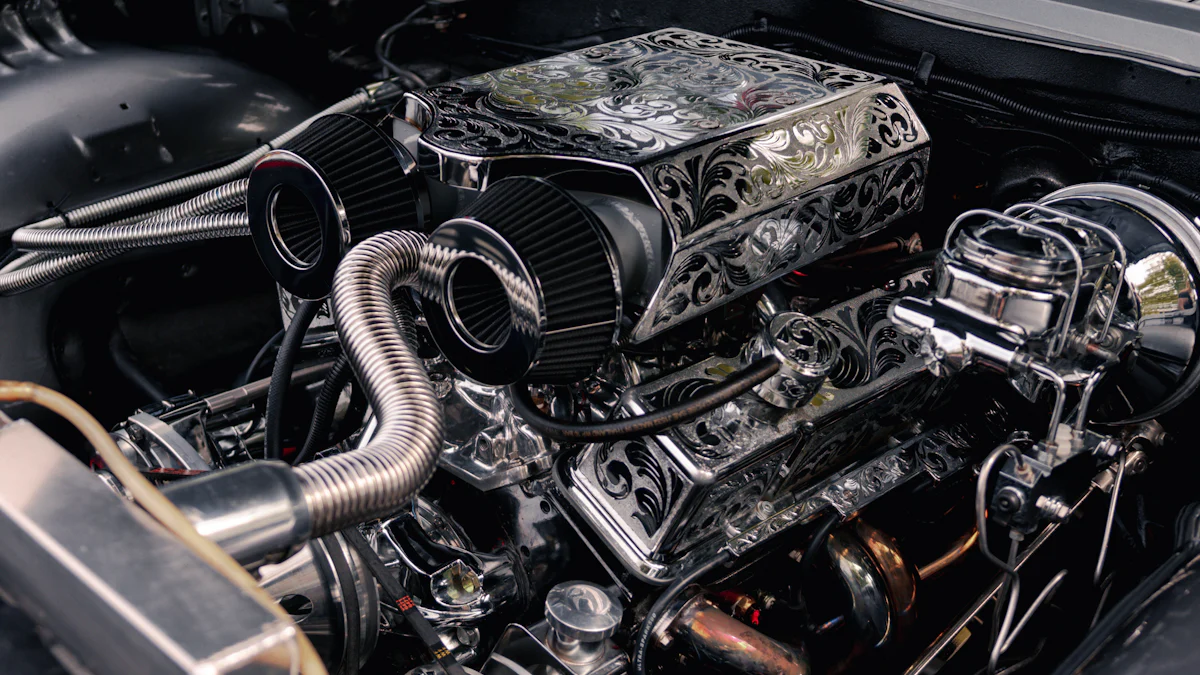
Creating custom parts with carbon fiber starts with gathering the right materials and tools. Having everything ready ensures a smoother process and better results. Let’s break it down into essentials you’ll need to get started.
Wesentliche Materialien
Carbon fiber fabric
The foundation of your project is the carbon fiber fabric. This material provides the strength and lightweight properties that make carbon fiber so popular. You can find it in various weaves and thicknesses, depending on your project’s needs. For beginners, a plain weave is easier to work with, while advanced users might explore twill or other patterns for a more refined look.
Epoxy resin and hardener
To bond the fabric and create a solid structure, you’ll need a two-part epoxy system. This includes a resin and a hardener. Look for a high-strength epoxy designed for use with composite materials. Following the manufacturer’s mixing ratio is crucial to ensure the resin cures properly and delivers the durability you’re aiming for.
Mold release agent
A mold release agent prevents your carbon fiber part from sticking to the mold. It’s an essential step that saves you from damaging your project during removal. Spray or apply it evenly across the mold’s surface before starting the layup process.
Sandpaper and polishing tools
Once your part is cured, you’ll need sandpaper to smooth out imperfections. Start with coarse grit to remove rough edges, then move to finer grits for a polished finish. Polishing tools or compounds can help you achieve a professional-grade shine.
Required Tools
Mixing containers and stir sticks
You’ll need disposable mixing containers and stir sticks to prepare your resin. These tools help you mix the resin and hardener thoroughly, ensuring a consistent application. Avoid reusing containers, as leftover residue can affect the curing process.
Brushes or rollers for resin application
Brushes or rollers are essential for applying resin evenly over the carbon fiber fabric. Use a brush for smaller, detailed areas and a roller for larger surfaces. This ensures the resin saturates the fabric without leaving dry spots.
Vacuum bagging equipment (optional for advanced projects)
For those looking to take their projects to the next level, vacuum bagging equipment can help. This technique compresses the carbon fiber sheets and removes excess resin, resulting in a stronger and lighter part. While optional, it’s worth considering if you want a professional finish.
Safety gear (gloves, goggles, respirator)
Safety should always come first. Wear gloves to protect your skin from resin, goggles to shield your eyes, and a respirator to avoid inhaling harmful fumes. Working with Verbundwerkstoffe can be hazardous without proper precautions, so don’t skip this step.
Pro Tip: If you’re new to working with carbon fiber cloth, practice on a small project first. This helps you get comfortable with cutting, layering, and applying resin before tackling more complex designs.
With these materials and tools, you’re ready to dive into your DIY carbon fiber project. Preparation is key, so take the time to gather everything you need before starting. The right setup makes all the difference in achieving a high-quality result.
Safety Precautions When Using a Carbon Fiber Kit
Working with carbon fiber can be exciting, but safety should always come first. The materials and tools involved can pose risks if not handled properly. By following these precautions, you’ll protect yourself and create a safer workspace.
Personal Protective Equipment (PPE)
Importance of wearing gloves to avoid skin contact with resin
Epoxy resin is a key component in carbon fiber projects, but it can irritate your skin. Always wear gloves when handling resin to prevent direct contact. Nitrile gloves work best because they resist chemicals and provide a snug fit. Skipping this step could lead to rashes or long-term sensitivity.
Using a respirator to prevent inhalation of harmful fumes
Resin fumes and carbon fiber dust can harm your lungs. A proper respirator protects you from inhaling these particles. Choose a respirator designed for paint or chemical work, as it filters out toxic fumes effectively. Even if the resin doesn’t have a strong smell, it’s better to stay safe than risk respiratory issues.
Profi-Tipp: When cutting or sanding carbon fiber, always wear a respirator and safety glasses. Tiny fibers can float in the air and irritate your throat, lungs, and eyes.
Workspace Preparation
Ensuring proper ventilation in the work area
Good airflow is essential when working with carbon fiber. Resin fumes and airborne fibers can accumulate in closed spaces, making them hazardous. Set up your workspace in a well-ventilated area, like a garage with open windows or an outdoor shed. If ventilation is limited, use a fan or an exhaust system to keep the air moving.
Keeping the workspace clean and free of dust
Carbon fiber dust can stick to surfaces and linger in the air. Keep your workspace clean by vacuuming regularly and wiping down surfaces. A clean area not only reduces health risks but also ensures better results for your project. Dust-free conditions help the resin bond smoothly with the fabric.
Quick Reminder: Use a vacuum cleaner with a HEPA filter to trap fine carbon fibers. Standard vacuums may release the particles back into the air.
Handling Carbon Fiber Materials
Avoiding direct contact with carbon fiber strands to prevent skin irritation
Carbon fiber strands are strong but can splinter easily. These tiny splinters can pierce your skin and cause irritation. Handle the fabric carefully and avoid touching it with bare hands. If a splinter gets under your skin, it won’t dissolve and could lead to infection. Gloves are your best defense against this risk.
Proper disposal of waste materials
Disposing of carbon fiber waste requires care. Don’t throw scraps or dust into regular trash bins. Place them in sealed bags to prevent fibers from spreading. Check local regulations for disposing of composite materials, as some areas may have specific guidelines. Proper disposal keeps your workspace safe and protects the environment.
Wussten Sie schon? Carbon fiber dust can cling to your clothes and spread to other areas. Change out of your work clothes before entering your home to avoid contamination.
By taking these precautions, you’ll minimize risks and enjoy a smoother experience with your carbon fiber projects. Safety isn’t just about following rules—it’s about ensuring you can keep creating without harm.
Step-by-Step Guide to Creating Carbon Fiber Parts
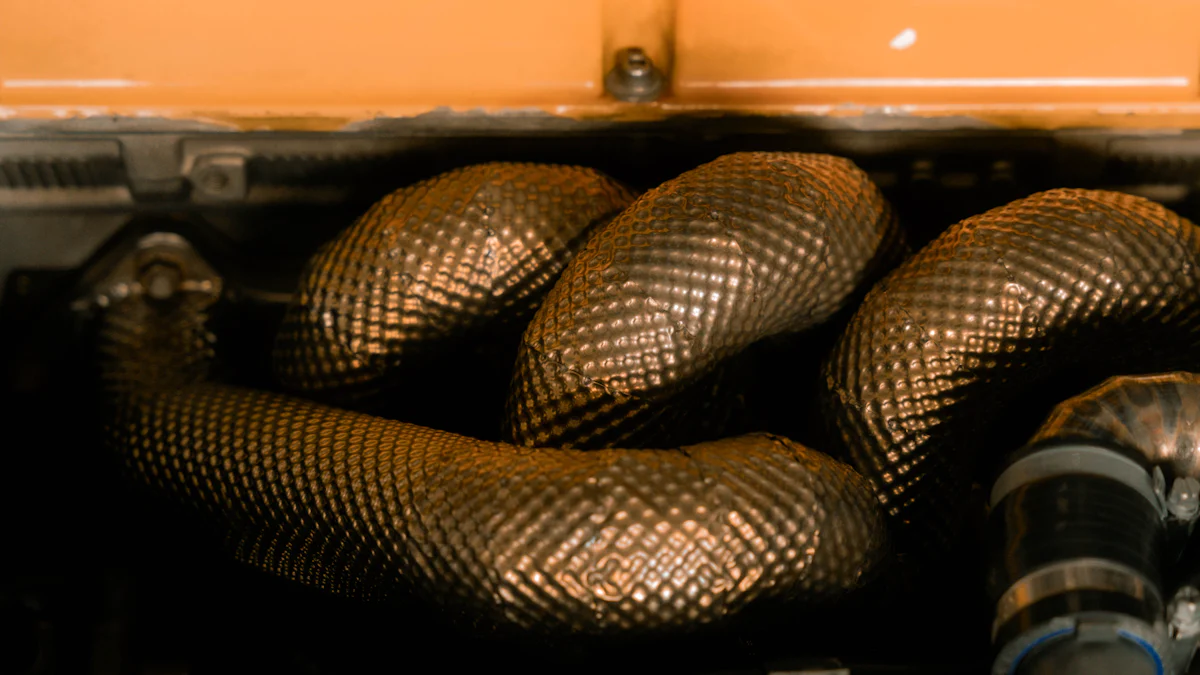
Creating carbon fiber parts may seem complex, but breaking it into clear steps makes the process manageable. Follow this guide to turn your ideas into reality with a carbon fiber kit.
Mold Preparation
Choosing or creating a mold for the desired part
The mold is the foundation of your project. It determines the shape and precision of your final piece. You can either purchase a pre-made mold or create one yourself using materials like fiberglass, wood, or even 3D-printed plastic. For beginners, starting with a simple mold for carbon fiber is a smart choice. Ensure the mold is sturdy and smooth, as imperfections will transfer to your finished part.
Profi-Tipp: If you’re making something like carbon fiber fenders or panels, use an existing part as a template to create your mold. This ensures accuracy and saves time.
Applying mold release agent to prevent sticking
Before you begin the layup process, apply a mold release agent generously. This step prevents the carbon fiber from sticking to the mold during curing. Use a brush or spray to coat the mold evenly. Missing this step could result in a ruined part or damage to your mold. Take your time to ensure full coverage.
Carbon Fiber Preparation
Cutting the fabric to the required size and shape
Cutting the carbon fiber fabric is a critical step. Use sharp scissors or a rotary cutter to achieve clean edges and prevent fraying. Measure carefully and cut the fabric slightly larger than the mold to allow for adjustments during the layup. For intricate designs, consider cutting smaller pieces and layering them strategically.
Kurzer Tipp: If you’re planning to make carbon fiber fenders or other curved parts, cut the fabric into strips or sections that can conform to the shape more easily.
Arranging the layers for optimal strength and appearance
Layering the fabric correctly ensures both strength and aesthetics. Alternate the direction of the weave in each layer to maximize durability. For a sleek, professional look, place a single layer of twill weave on top. This creates the signature carbon fiber pattern that enthusiasts love. Plan your layers carefully before moving to the next step.
Fabric Layup
Applying resin to the mold and first layer of fabric
The wet lay-up technique is the most common method for DIY projects. Start by mixing the epoxy resin and hardener according to the instructions in your carbon fiber kit. Apply a thin layer of resin to the mold using a brush or roller. Place the first layer of fabric onto the mold and press it gently to remove air bubbles. Then, saturate the fabric with resin, ensuring even coverage.
Wussten Sie schon? Wet lay-up is ideal for beginners because it requires minimal equipment. However, advanced users might explore prepreg lamination for more precise results.
Adding additional layers and ensuring even resin distribution
Continue adding layers of fabric, applying resin between each one. Use a squeegee or roller to spread the resin evenly and remove excess. This step is crucial for achieving a strong bond and avoiding weak spots. For projects like carbon fiber fenders, aim for at least three to five layers, depending on the desired thickness and strength.
Profi-Tipp: If you’re aiming for a professional finish, consider laminating techniques like vacuum bagging. This compresses the layers and removes excess resin, resulting in a lighter and stronger part.
By following these steps, you can make carbon fiber parts that are both functional and visually stunning. Whether you’re crafting custom panels, tools, or decorative pieces, attention to detail during the layup process ensures success.
Curing the Part
Allowing the resin to cure at room temperature or using heat for faster results
Once you’ve layered the carbon fiber and resin, curing solidifies your work into a durable, finished part. The curing process depends on the type of resin you’re using. Most resins cure effectively at room temperature. Place your project in a clean, dust-free area and let it sit undisturbed. This step can take anywhere from 24 to 48 hours, so patience is key.
If you’re short on time or want to enhance the resin’s strength, consider using heat. A heat gun or curing oven speeds up the process. Follow the resin manufacturer’s guidelines for the ideal temperature. Keep an eye on the part to avoid overheating, which could cause warping or bubbles. Heat curing works especially well for projects requiring extra durability, like car panels or bike components.
Profi-Tipp: If you’re curing in a garage or workshop, ensure the space stays free of dust and debris. Even tiny particles can stick to the resin and ruin the finish.
Removing the part from the mold and inspecting for imperfections
After curing, it’s time to unveil your creation. Carefully remove the part from the mold. Start by loosening the edges with a plastic wedge or similar tool. Avoid using metal tools, as they can scratch or damage the surface. If the mold release agent was applied correctly, the part should come out smoothly.
Once removed, inspect the part for imperfections. Look for air bubbles, uneven resin distribution, or rough edges. Minor flaws can often be fixed during the finishing stage. If you notice significant issues, reflect on what went wrong. Did you apply enough resin? Was the mold properly prepared? Learning from these mistakes will improve your future projects.
Quick Reminder: Handle the cured part gently during removal. Carbon fiber is strong, but the edges can still chip if you’re not careful.
Der letzte Schliff
Sanding and polishing the part for a smooth finish
Sanding transforms your raw carbon fiber part into a sleek, professional-looking piece. Start with coarse-grit sandpaper (around 120 grit) to remove rough edges and imperfections. Work your way up to finer grits, such as 400 or 600, for a smoother surface. Always sand in a well-ventilated area and wear a respirator to avoid inhaling fine dust particles.
After sanding, polish the surface to bring out the carbon fiber’s signature shine. Use a polishing compound and a soft cloth or buffing tool. This step enhances the part’s appearance and gives it that high-performance, showroom-quality look. Polishing also helps smooth out any remaining micro-scratches from sanding.
Wussten Sie schon? Car enthusiasts love carbon fiber for its sleek aesthetic. Polished carbon fiber panels, spoilers, and hoods not only look stunning but also outperform traditional materials like fiberglass and sheet metal.
Applying a clear coat for added durability and shine
A clear coat adds the final layer of protection to your carbon fiber part. It seals the surface, making it more resistant to scratches, UV rays, and general wear. Choose a high-quality automotive-grade clear coat for the best results. Apply it evenly using a spray gun or brush, following the manufacturer’s instructions.
Allow the clear coat to dry completely before handling the part. This step not only enhances durability but also amplifies the glossy finish, making the carbon fiber weave pop. A well-applied clear coat can make your DIY project look like it came straight from a professional workshop.
Profi-Tipp: For an ultra-smooth finish, lightly sand the clear coat with fine-grit sandpaper (around 1000 grit) between coats. This technique creates a flawless, glass-like surface.
By taking the time to cure, sand, polish, and coat your part, you’ll achieve a result that’s both functional and visually impressive. Whether you’re crafting lightweight car components or custom tools, these finishing touches elevate your project to the next level.
Tips for Success with DIY Carbon Fiber Projects
Embarking on a DIY carbon fiber journey can feel overwhelming at first, but with the right approach, you’ll find it both rewarding and enjoyable. Whether you’re a beginner or looking to refine your skills, these tips will help you achieve better results and avoid common pitfalls.
Practical Advice for Beginners
Start with small, simple projects to build confidence
If you’re new to working with carbon fiber, start small. Tackling a large or intricate project right away can lead to frustration. Begin with something manageable, like a flat panel or a decorative piece. This allows you to familiarize yourself with the materials and processes without feeling overwhelmed. Small projects also give you a chance to experiment with cutting, layering, and applying resin, which are essential skills in manufacturing carbon fiber parts.
Profi-Tipp: Use leftover scraps of carbon fiber fabric for practice. This way, you won’t waste valuable materials while learning.
Practice cutting and layering fabric before working on the final piece
Cutting and layering carbon fiber fabric requires precision. Uneven edges or poorly aligned layers can weaken the structure and affect the appearance of your finished part. Before starting your main project, practice cutting clean edges with sharp scissors or a rotary cutter. Experiment with layering techniques to understand how different weaves interact and how to achieve optimal strength.
Kurzer Tipp: When layering, alternate the direction of the weave for maximum durability. This technique ensures your part can handle stress from multiple angles.
Common Mistakes to Avoid
Using too much or too little resin
Applying the correct amount of resin is crucial in manufacturing carbon fiber parts. Too much resin adds unnecessary weight and reduces the strength of the composite. Too little resin leaves dry spots, compromising the bond between layers. Follow the manufacturer’s instructions for mixing and applying resin. Use a brush or roller to distribute it evenly, ensuring every layer is fully saturated without excess pooling.
Wussten Sie schon? Vacuum bagging can help remove excess resin and improve the strength-to-weight ratio of your part. While not essential for beginners, it’s a technique worth exploring as you gain experience.
Skipping safety precautions or rushing the curing process
Safety and patience are non-negotiable in DIY carbon fiber projects. Skipping protective gear like gloves and respirators can expose you to harmful chemicals and fine fibers. Rushing the curing process often leads to weak or warped parts. Allow the resin to cure fully, whether at room temperature or with heat, as recommended by the manufacturer. A properly cured part not only looks better but also performs better under stress.
Reminder: Always work in a well-ventilated area and follow all safety guidelines. Your health and safety should never take a backseat to speed.
Advanced Techniques to Explore
Using vacuum bagging for a professional finish
Vacuum bagging is a game-changer for those looking to elevate their DIY carbon fiber projects. This technique compresses the layers of fabric and resin, removing air bubbles and excess resin. The result is a lighter, stronger, and more uniform part. While it requires additional equipment, such as a vacuum pump and bagging film, the investment pays off in the quality of your finished product.
Profi-Tipp: If you’re serious about manufacturing carbon fiber parts, consider incorporating vacuum bagging into your workflow. It’s a staple in professional composite manufacturing.
Experimenting with different fabric weaves and resins
Once you’ve mastered the basics, don’t be afraid to experiment. Different carbon fiber weaves, such as twill or unidirectional, offer unique properties and aesthetics. Similarly, various resins can enhance the performance of your parts, especially in high-temperature or high-stress environments. Prepreg carbon fiber, which comes pre-impregnated with resin, is another option for achieving a flawless surface finish with less effort.
Wussten Sie schon? Prepreg carbon fiber is widely used in aerospace and automotive manufacturing due to its superior strength and ease of use. It’s an excellent choice for advanced DIYers aiming for professional-grade results.
By following these tips, you’ll not only improve your skills but also enjoy the process of creating custom carbon fiber parts. Remember, every project is an opportunity to learn and grow. With practice and patience, you’ll soon be crafting parts that rival professionally manufactured ones.
Why Use a Carbon Fiber Kit for DIY Projects?
When it comes to creating custom parts, a carbon fiber kit offers unmatched advantages. Whether you’re a hobbyist or a seasoned DIYer, this material opens up a world of possibilities. Let’s explore why it’s the go-to choice for so many creators.
Leicht und langlebig
Ideal for high-performance applications
Carbon fiber stands out for its incredible strength-to-weight ratio. It’s no wonder industries like aerospace and motorsports rely on it for high-performance applications. You can create lightweight products that don’t compromise on durability. Imagine crafting a bike frame or car panel that’s both feather-light and tough enough to handle stress. This combination of properties makes carbon fiber perfect for projects where performance matters most.
Spaßfaktor: Carbon fiber is five times stronger than steel but weighs only a fraction of it. That’s why it’s a favorite for building parts that need to be both strong and light.
Customizable and Versatile
Suitable for a wide range of DIY projects
A carbon fiber kit gives you the freedom to design parts tailored to your needs. From automotive components to home decor, the possibilities are endless. You can experiment with different shapes, sizes, and finishes to suit your project. For beginners, starting with simple designs like flat panels or decorative pieces is a great way to build confidence. As you gain experience, you’ll find yourself tackling more complex creations.
Profi-Tipp: Cut your carbon fiber fabric slightly larger than needed. This allows room for adjustments during the layup process. With practice, you’ll get better at cutting precise shapes for each project.
Professional-Looking Results
Achieve a sleek, modern aesthetic
One of the most appealing aspects of using a carbon fiber kit is the professional finish it delivers. The signature weave pattern of carbon fiber adds a sleek, modern aesthetic to any project. Whether you’re making a custom car spoiler or a stylish phone case, the end result looks polished and high-end. Adding a clear coat enhances the shine and protects the surface, giving your work a showroom-quality appearance.
Anecdote: A DIY enthusiast once shared how their first carbon fiber project—a simple flat panel—turned out so well that friends thought it was professionally made. With the right tools and techniques, you can achieve similar results.
By choosing a carbon fiber kit, you’re not just building parts—you’re creating something that combines functionality, durability, and style. It’s an investment in quality and creativity that pays off with every project you complete.
Creating carbon fiber parts is an exciting and rewarding process. By following the steps—preparing your mold, layering the fabric, applying resin, curing, and finishing—you can craft lightweight, durable, and professional-grade components. These projects not only save costs but also allow you to customize designs to fit your needs. The versatility of carbon fiber opens up endless possibilities, from automotive upgrades to unique home decor. Now’s the time to dive in, experiment, and bring your ideas to life. With a little patience and practice, you’ll master the art of crafting with carbon fiber kits.
FAQ
What is the best way to start working with carbon fiber as a beginner?
Starting small is the key. Choose a simple project like a flat panel or a decorative piece. This helps you get familiar with cutting, layering, and applying resin without feeling overwhelmed. Practice on scrap pieces of carbon fiber fabric to refine your skills before moving on to more complex designs. Remember, every project is a learning experience, so take your time and enjoy the process.
Tipp: Use sharp scissors or a rotary cutter for clean cuts. This prevents fraying and makes the fabric easier to handle.
How do I choose the right carbon fiber fabric for my project?
The choice depends on your project’s requirements. For beginners, a plain weave fabric is easier to work with and provides a clean look. If you want a more refined appearance, consider a twill weave. For strength-focused projects, unidirectional fabric works best. Experimenting with different weaves can help you understand their unique properties and aesthetics.
Profi-Tipp: Always cut your fabric slightly larger than needed. This gives you room to adjust during the layup process.
Do I need special tools for carbon fiber manufacturing?
You don’t need advanced tools to get started. Basic tools like mixing containers, stir sticks, brushes, and sandpaper are enough for most DIY projects. If you want a professional finish, consider investing in vacuum bagging equipment. This compresses the layers and removes excess resin, resulting in a stronger and lighter part.
Wussten Sie schon? Vacuum bagging is a common technique in professional carbon fiber manufacturing and can elevate the quality of your DIY projects.
How can I avoid air bubbles during the resin application?
Air bubbles often form when resin isn’t applied evenly. Use a brush or roller to spread the resin smoothly across the fabric. Press gently to remove trapped air. For larger projects, a squeegee can help distribute the resin more effectively. If you’re using vacuum bagging, it will naturally eliminate most air bubbles.
Kurzer Tipp: Work slowly and methodically. Rushing the process increases the chances of air bubbles forming.
Is it safe to work with carbon fiber at home?
Yes, but safety precautions are essential. Always wear gloves, goggles, and a respirator to protect yourself from resin fumes and carbon fiber dust. Work in a well-ventilated area to minimize exposure to harmful particles. Keeping your workspace clean also reduces risks and ensures better results.
Erinnerung: Carbon fiber dust can cling to your clothes. Change out of your work attire before entering your home to avoid spreading it.
How long does it take for the resin to cure?
Curing time depends on the type of resin you’re using. Most resins cure at room temperature within 24 to 48 hours. If you’re in a hurry, heat curing can speed up the process. Follow the manufacturer’s guidelines for the ideal temperature and duration. Avoid disturbing the part during curing to ensure a smooth finish.
Profi-Tipp: Keep your curing area dust-free. Even tiny particles can stick to the resin and ruin the surface.
Can I reuse molds for multiple projects?
Yes, molds can be reused if they’re properly maintained. Apply a mold release agent before each use to prevent sticking. After removing your part, clean the mold thoroughly to remove any residue. High-quality molds last longer and provide consistent results.
Spaßfaktor: Many DIY enthusiasts use existing parts, like car panels, as templates to create molds. This saves time and ensures accuracy.
What should I do if my carbon fiber part has imperfections?
Minor imperfections like air bubbles or rough edges can be fixed during the finishing stage. Sand the surface with coarse-grit sandpaper to remove flaws, then switch to finer grits for a smooth finish. Polishing compounds can enhance the shine and hide micro-scratches. For major issues, reflect on what went wrong and adjust your process for the next attempt.
Remember: Every mistake is an opportunity to learn and improve your skills.
Can I paint or coat my carbon fiber part?
Yes, you can apply a clear coat to enhance durability and shine. A high-quality automotive-grade clear coat works best. If you prefer a colored finish, use paint designed for composite materials. Always sand the surface lightly before applying any coating to ensure proper adhesion.
Profi-Tipp: Apply multiple thin coats instead of one thick layer. This prevents drips and creates a flawless finish.
How do I dispose of carbon fiber waste?
Dispose of carbon fiber scraps and dust responsibly. Place them in sealed bags to prevent fibers from spreading. Check local regulations for composite material disposal, as some areas have specific guidelines. Proper disposal keeps your workspace safe and protects the environment.
Wussten Sie schon? Carbon fiber waste can cling to surfaces and linger in the air. Regular cleaning with a vacuum equipped with a HEPA filter helps maintain a safe workspace.