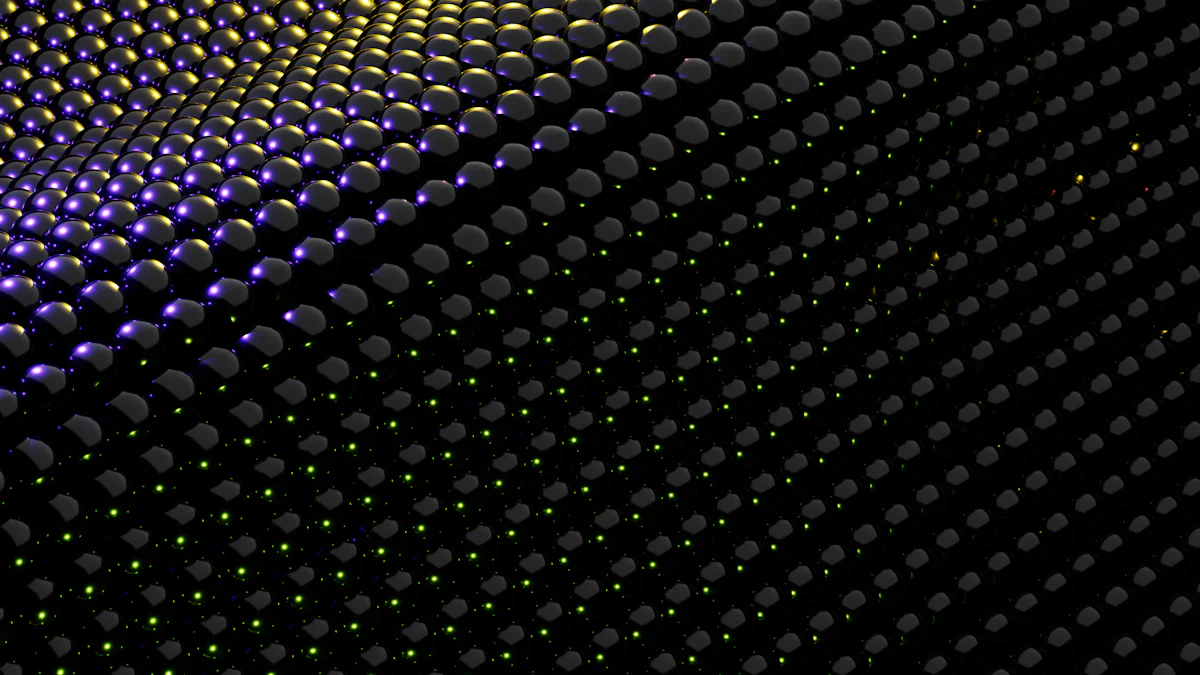
Dry carbon fiber stands out as a revolutionary material crafted from pre-impregnated carbon sheets. Its unique composition ensures exceptional strength and lightweight properties, making it indispensable in industries like automotive and aerospace. For instance, automotive manufacturers use it to reduce vehicle weight by up to 50%, significantly enhancing fuel efficiency and performance. The manufacturing process of dry carbon prioritizes precision, ensuring consistent resin distribution and fiber alignment. This meticulous approach results in a material that surpasses traditional alternatives in quality and reliability, meeting the demands of cutting-edge applications.
Key Takeaways
Dry carbon fiber is a lightweight and strong material, ideal for high-performance applications in industries like automotive and aerospace.
The manufacturing process of dry carbon prioritizes precision, ensuring consistent resin distribution and fiber alignment for superior quality.
Using pre-impregnated materials (pre-pregs) allows for better resin control, reducing waste and enhancing the mechanical properties of the final product.
The autoclave curing process strengthens dry carbon by applying heat and pressure, resulting in a flawless finish and improved durability.
Dry carbon’s exceptional strength-to-weight ratio enables the design of components that enhance fuel efficiency and performance in vehicles and aircraft.
Choosing dry carbon fiber supports sustainable manufacturing practices by minimizing material waste and reducing environmental impact.
Advanced techniques like filament winding allow for the creation of specialized structures, meeting the exact requirements of high-performance applications.
What Is Dry Carbon Fiber?
Definition and Unique Properties
Dry carbon fiber represents a cutting-edge material known for its strength, lightweight nature, and precision. Unlike traditional materials, it is crafted using pre-impregnated carbon sheets, where the resin is evenly distributed across the fibers before the curing process begins. This ensures a consistent structure, free from irregularities, and enhances its mechanical properties.
One of the standout features of dry carbon is its ability to achieve a higher fiber volume fraction. This means more carbon fibers are packed into the material, resulting in superior stiffness, strength, and fatigue resistance. Additionally, the controlled resin impregnation minimizes waste, making it an environmentally conscious choice. Industries like aerospace and automotive rely on these unique properties to create components that demand both durability and reduced weight.
Differences Between Dry and Wet Carbon Fiber
The primary distinction between dry and wet carbon fiber lies in their manufacturing processes. Dry carbon uses pre-impregnated materials, often referred to as “pre-preg,” where the resin is already infused into the carbon fabric. This method ensures precise resin control and eliminates the need for manual application. In contrast, wet carbon involves applying resin manually to the carbon sheets during production, which can lead to uneven distribution and weaker structural integrity.
Dry carbon undergoes curing in an autoclave, a high-pressure and high-temperature chamber. This process strengthens the material and removes any imperfections. Wet carbon, however, cures at room temperature or under less controlled conditions, resulting in a thicker and less refined product. The intricate process of creating dry carbon makes it thinner, lighter, and stronger than its wet counterpart. These qualities make dry carbon the preferred choice for high-performance applications.
Materials Used in Dry Carbon Fiber Manufacturing
Carbon Fiber Precursors
The journey of creating dry carbon begins with selecting the right precursor. A precursor serves as the raw material for producing carbon fibers. Polyacrylonitrile (PAN) is the most commonly used precursor due to its ability to deliver high-performance results. PAN undergoes a process called carbonization, where it is heated at extremely high temperatures in an oxygen-free environment. This step transforms the precursor into pure carbon fibers, which form the backbone of dry carbon.
Other precursors, such as rayon and pitch, have also been explored. Rayon was one of the first materials used to create carbon fibers, while pitch offers a cost-effective alternative. However, PAN remains the industry standard because of its superior mechanical properties. The choice of precursor directly impacts the strength, stiffness, and durability of the final product. By carefully selecting and processing these materials, manufacturers ensure that the carbon fibers meet the rigorous demands of industries like aerospace and automotive.
Pre-Impregnated Materials and Resin Systems
Pre-impregnated materials, or pre-pregs, play a crucial role in the production of dry carbon. These materials consist of carbon fiber sheets or fabrics that are pre-infused with resin. The resin, evenly distributed across the fibers, eliminates the need for manual application during manufacturing. This ensures consistency in the material’s structure and enhances its overall quality.
The resin systems used in pre-pregs are specially formulated to provide optimal performance. Epoxy resins are the most common choice due to their excellent bonding properties and resistance to environmental factors. During the curing process, the resin hardens, binding the carbon fibers together and creating a strong, lightweight composite.
Pre-pregs are cured in an autoclave, a high-pressure and high-temperature chamber. This step removes impurities and strengthens the material. The controlled resin content in pre-pregs allows for precise fiber alignment, resulting in a thinner and more uniform product. This meticulous process not only improves the material’s mechanical properties but also reduces waste, making dry carbon an environmentally friendly option.
Step-by-Step Manufacturing Process of Dry Carbon
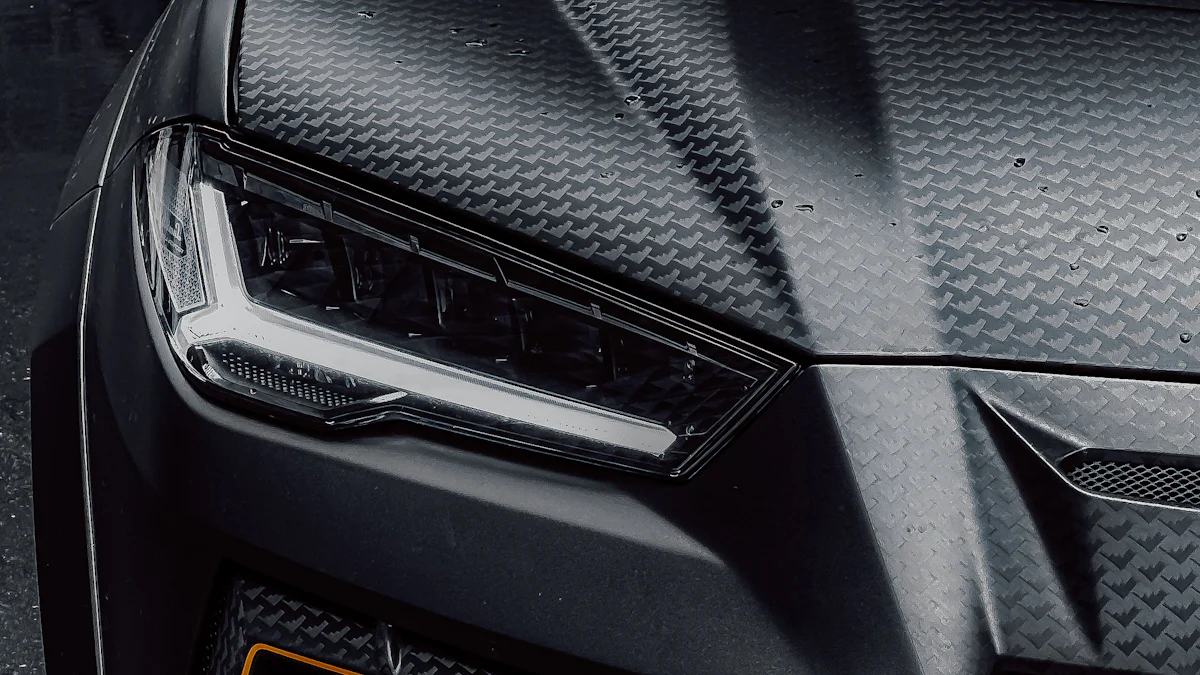
Layering Carbon Fiber Sheets
The manufacturing process begins with layering carbon fiber sheets. These sheets, often referred to as dry fiber textiles, arrive in rolls of fabric. Automated cutting machines, guided by CAD data, precisely cut the fabric into specific shapes. This ensures that each layer fits perfectly into the final design. You then stack these pre-cut layers in a mold, carefully aligning them to achieve the desired fiber orientation. Proper alignment is crucial because it directly impacts the strength and stiffness of the finished product. By controlling this step, you ensure the material’s structural integrity and performance.
Application of Heat and Pressure
Once the layers are in place, the next step involves applying heat and pressure. This stage activates the resin within the pre-impregnated carbon sheets. The resin, already infused into the fibers, begins to soften under heat. Pressure ensures that the layers bond tightly, eliminating air pockets and voids. This combination of heat and pressure creates a uniform structure, enhancing the material’s mechanical properties. You must monitor this process closely to maintain consistency and avoid defects. The precision of this step sets dry carbon apart from other materials, ensuring superior quality.
Autoclave Curing Process
The final step is curing the material in an autoclave. An autoclave functions like a high-tech pressure cooker, using elevated temperatures and pressures to solidify the resin. During this process, impurities are removed, and the resin hardens, binding the carbon fibers together. This step not only strengthens the material but also ensures a smooth, flawless finish. The controlled environment of the autoclave allows you to achieve the exact specifications required for high-performance applications. By the end of this process, the dry carbon emerges as a lightweight, durable, and precision-engineered material ready for use.
Advanced Techniques in Dry Carbon Fiber Production
Pre-Preg Process for Resin Control
The pre-preg process stands as a cornerstone in the production of dry carbon. This technique involves pre-impregnating carbon fiber sheets with resin before the manufacturing process begins. By using this method, you gain precise control over the resin content in the material. This ensures that the resin is evenly distributed across the fibers, eliminating inconsistencies that could weaken the final product.
Pre-preg materials undergo strict quality checks to maintain uniformity. Manufacturers store these materials at low temperatures to prevent premature curing. When you use pre-pregs, you can achieve a higher fiber volume fraction, which directly enhances the strength and stiffness of the material. This process also reduces waste, as the exact amount of resin required is already infused into the fibers. According to research, optimized fabrication processes like pre-pregging not only improve the mechanical properties of dry carbon but also lower production costs, making it a sustainable choice for industries.
Filament Winding for Specialized Structures
Filament winding is another advanced technique used in the production of dry carbon. This method involves winding continuous carbon fibers around a rotating mandrel to create cylindrical or tubular structures. You can use this technique to produce components like pressure vessels, pipes, and aerospace parts that require high strength and precision.
The process begins with carbon fibers coated in resin, which are carefully wound onto the mandrel in specific patterns. The orientation of the fibers plays a critical role in determining the strength and performance of the final product. Once the winding is complete, the structure undergoes curing in an autoclave to solidify the resin and bond the fibers together.
Filament winding offers several advantages. It allows you to create lightweight yet durable structures with minimal material waste. The ability to customize fiber orientation ensures that the finished product meets the exact requirements of its application. Researchers have highlighted this technique as a key innovation in dry carbon production, enabling the creation of specialized components for high-performance industries.
Benefits of Using Dry Carbon Fiber
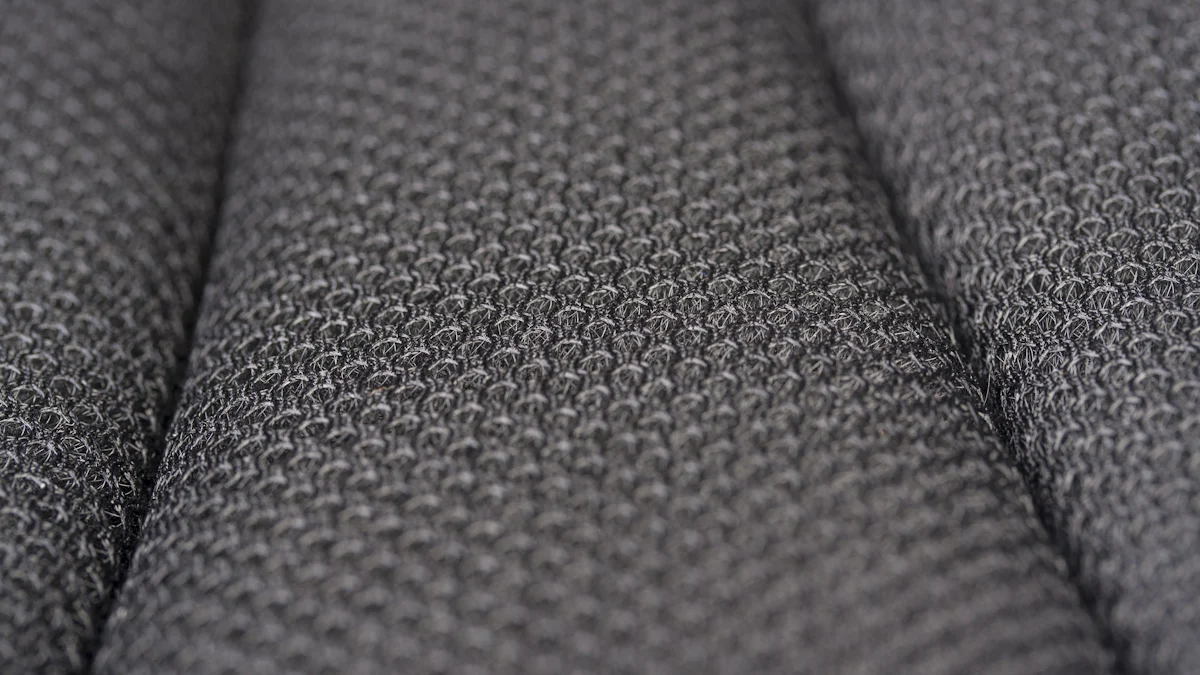
Superior Strength-to-Weight Ratio
Dry carbon offers an exceptional strength-to-weight ratio, making it a preferred material for high-performance applications. You get a material that is incredibly strong while remaining lightweight. This balance allows you to design components that can withstand significant stress without adding unnecessary weight. For example, in the aerospace industry, reducing weight directly improves fuel efficiency and performance. Similarly, in automotive manufacturing, using dry carbon helps you create vehicles that are faster and more agile.
The high fiber volume fraction in dry carbon contributes to its superior structural integrity. By packing more carbon fibers into the material, you achieve greater stiffness and resistance to deformation. This property ensures that the material performs reliably under demanding conditions. Whether you are designing aircraft parts or sports car components, the strength-to-weight ratio of dry carbon gives you a competitive edge.
Enhanced Durability and Precision
Dry carbon stands out for its durability and precision. The controlled resin distribution in pre-impregnated materials ensures a uniform structure, free from weak spots or inconsistencies. This precision enhances the material’s mechanical properties, allowing you to rely on it for applications that demand long-term performance. Components made from dry carbon resist wear and tear, even in harsh environments.
The autoclave curing process further strengthens the material. By applying heat and pressure, you eliminate air pockets and imperfections, resulting in a flawless finish. This meticulous process ensures that every piece of dry carbon meets exact specifications. When you use dry carbon, you benefit from a material that combines durability with precision, making it ideal for industries like aerospace, automotive, and sports equipment manufacturing.
Reduced Material Waste and Environmental Impact
Dry carbon production minimizes material waste, making it an environmentally friendly choice. The pre-preg process ensures precise resin control, reducing excess resin and improving distribution. This efficiency means you use only the necessary amount of material, avoiding waste. Compared to wet layup processes, dry carbon generates significantly less waste, contributing to sustainable manufacturing practices.
By choosing dry carbon, you also reduce the environmental impact of your projects. The efficient use of materials not only lowers production costs but also aligns with eco-friendly goals. Industries increasingly prioritize sustainability, and dry carbon helps you meet these demands without compromising on quality or performance. Its reduced waste and resource-efficient production make it a responsible choice for modern manufacturing.
The process of manufacturing dry carbon involves precise steps that ensure exceptional quality. From layering carbon fiber sheets to curing in an autoclave, every stage enhances its strength and durability. You benefit from a material that is thinner, lighter, and stronger than wet carbon due to its intricate production methods. Its unique properties, like superior resin control and high fiber volume, make it ideal for demanding applications. As industries continue to innovate, dry carbon’s role will expand, offering sustainable and high-performance solutions for the future.