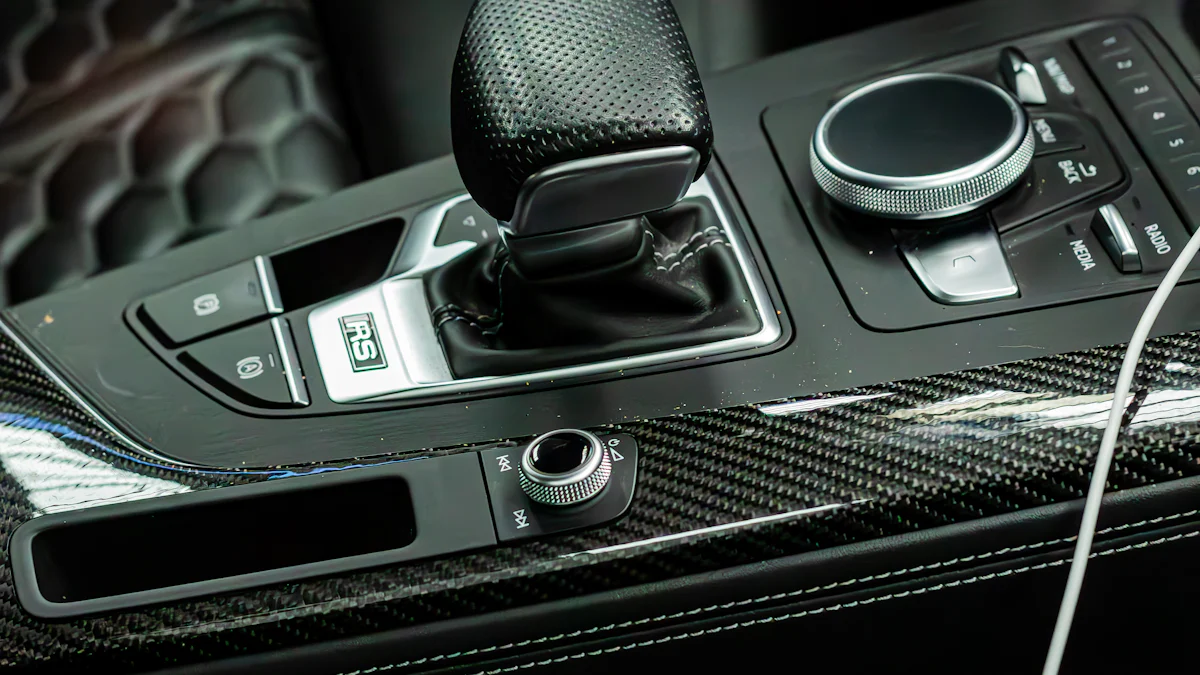
Finding the right carbon fiber for your needs can feel like a puzzle. You want something strong, lightweight, and durable, but the cost can quickly add up. Did you know that carbon fiber price ranges from $15,000 to $28,000 per metric ton? That’s a big investment, so understanding what you’re paying for is crucial. Carbon fiber products stand out because they combine exceptional strength with lightness, outperforming materials like steel and titanium. By learning about the types and characteristics of carbon fiber, you can make smarter choices that fit both your budget and your project.
Key Takeaways
Understand the different types of carbon fiber—Standard, Intermediate, and High Modulus—to choose the right one for your project’s specific needs.
Prioritize application-specific requirements, such as strength and weight, to ensure the carbon fiber you select meets the demands of your project.
Consider the long-term value of carbon fiber; investing in higher-quality materials can save money on maintenance and replacements over time.
Research suppliers thoroughly to ensure you choose reputable manufacturers that adhere to quality standards, avoiding potential pitfalls of low-quality materials.
Balance performance and budget by identifying must-have features and avoiding unnecessary specifications that could inflate costs.
Explore alternative materials, like carbon fiber composites or glass fiber, to achieve cost-effectiveness without compromising on performance.
Utilize carbon fiber prototyping to test designs and optimize material use, reducing waste and ensuring your final product meets performance standards.
Overview of Carbon Fiber Types and Characteristics
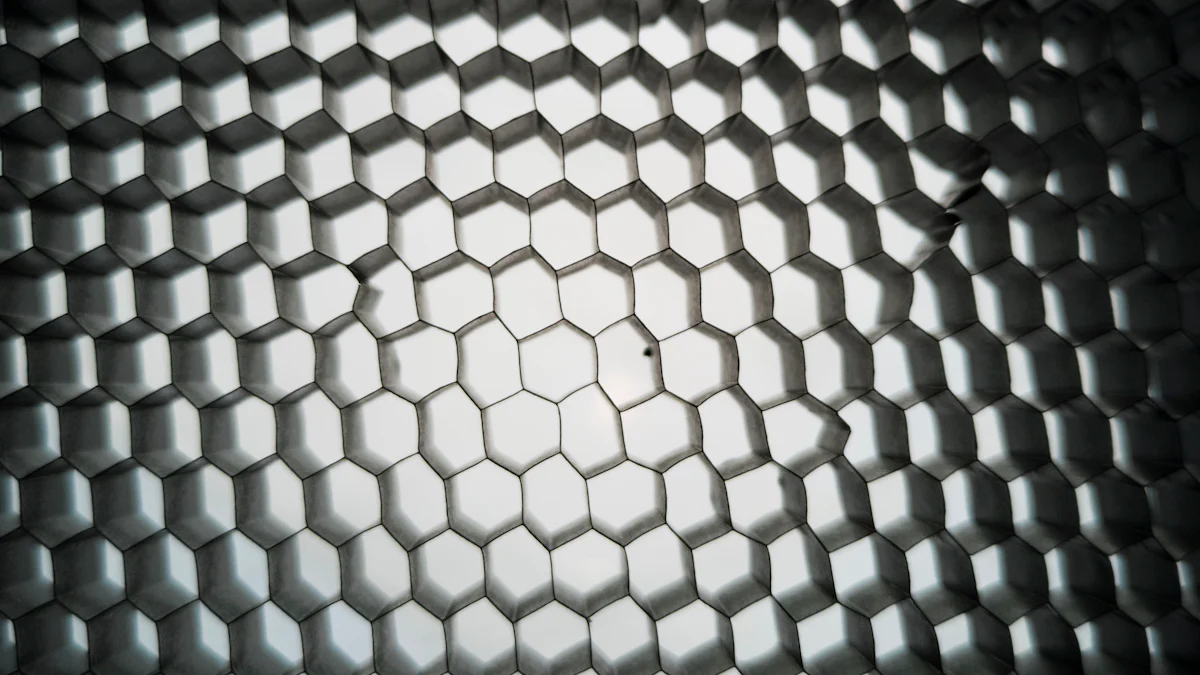
When it comes to choosing the right carbon fiber, understanding its types and characteristics is essential. Each type of carbon fiber offers unique benefits, making it easier for you to find the perfect match for your project. Let’s break it down.
Types of Carbon Fiber
Standard Modulus Carbon Fiber
Standard modulus carbon fiber is the most common type. It provides a balance of strength, stiffness, and affordability. This makes it a popular choice for applications like sports equipment and general-purpose structures. If you’re looking for a reliable material without breaking the bank, this could be your go-to option.
Intermediate Modulus Carbon Fiber
Intermediate modulus carbon fiber offers higher stiffness compared to the standard type. It’s ideal for projects that demand enhanced performance, such as aerospace components or high-end automotive parts. While it costs more, its improved properties make it worth considering for demanding applications.
High Modulus Carbon Fiber
High modulus carbon fiber is the premium option. It delivers exceptional stiffness and is often used in critical applications like satellites or advanced robotics. This type is stronger than steel and incredibly lightweight, but its high cost limits its use to specialized industries. If performance is your top priority, this is the ultimate choice.
Characteristics of Carbon Fiber
Strength-to-Weight Ratio
Carbon fiber stands out for its unmatched strength-to-weight ratio. It’s five times lighter than steel yet ten times stronger than steel. This makes it a game-changer for industries like aerospace and motorsports, where reducing weight without compromising strength is crucial.
Durability and Flexibility
Durability is another key feature of carbon fiber. It resists wear, abrasion, and fatigue, ensuring a long lifespan. Despite its stiffness, carbon fiber fabric can also offer flexibility when woven into specific patterns. This adaptability allows it to meet the needs of various applications, from rigid structures to flexible designs.
Thermal and Chemical Resistance
Carbon fiber fabric excels in extreme conditions. It withstands high temperatures and resists chemical corrosion, making it a reliable material for harsh environments. Whether you’re working on a project exposed to heat or chemicals, carbon fiber ensures durability and performance.
By understanding these types and characteristics, you can make an informed choice. Whether you need a cost-effective solution or a high-performance material, carbon fiber fabrics offer versatility and reliability for any project.
Key Factors to Consider When Choosing Carbon Fiber
Choosing the right carbon fiber involves more than just picking a material. You need to think about how it fits your project’s requirements, its performance, and your budget. Let’s dive into the key factors that can guide your decision.
Application-Specific Requirements
Carbon fiber shines in many industries, but each application has unique demands. Understanding these needs helps you select the most suitable option.
Structural Applications (e.g., Aerospace, Automotive)
For structural projects, strength and stiffness take center stage. Aerospace and automotive industries rely on carbon fiber for its high strength-to-weight ratio. It reduces weight while maintaining durability, which improves fuel efficiency and overall performance. If your project involves load-bearing components, prioritize carbon fiber types that meet these structural demands.
Recreational Applications (e.g., Sports Equipment)
In recreational products like bicycles, tennis rackets, or fishing rods, carbon fiber offers both performance and comfort. Its lightweight nature enhances usability, while its flexibility ensures durability during repeated use. For these applications, you can often balance affordability with performance by choosing intermediate or standard modulus carbon fiber.
Industrial Applications (e.g., Robotics, Manufacturing)
Industrial uses demand materials that can handle stress and resist wear. Carbon fiber’s chemical resistance and low thermal expansion make it ideal for robotics and manufacturing equipment. If your project involves harsh environments or repetitive motion, focus on carbon fiber types designed for durability and long-term reliability.
Performance Metrics
The performance of carbon fiber depends on several critical metrics. These factors determine how well the material will meet your project’s goals.
Strength and Stiffness
Strength and stiffness are the backbone of carbon fiber’s appeal. Whether you’re building a lightweight drone or a high-performance car, these properties ensure the material can handle stress without bending or breaking. Always match the material’s strength and stiffness needs to your project’s requirements.
Weight and Density
Weight plays a crucial role in applications where mobility or speed matters. Carbon fiber’s low density makes it a top choice for projects requiring reduced weight without sacrificing strength. Evaluate your weight requirements carefully to ensure the material aligns with your goals.
Fatigue Resistance
Fatigue resistance measures how well carbon fiber holds up under repeated stress. This is especially important for applications like aircraft wings or sports equipment, where the material faces constant use. Choosing a carbon fiber type with high fatigue resistance ensures long-term performance and safety.
Budget Considerations
Your budget is a key factor when selecting carbon fiber. While the material offers incredible benefits, it’s essential to weigh the cost against your project’s needs.
Carbon Fiber Price and Long-Term Value
Carbon fiber price varies widely based on type and quality. Standard modulus options are more affordable, while high modulus types come with a premium price tag. However, investing in higher-quality carbon fiber can save money in the long run by reducing maintenance and replacement costs. Always consider the material’s long-term value when evaluating its price.
Trade-Offs Between Quality and Affordability
Balancing quality and affordability is a challenge. While it’s tempting to choose the cheapest option, low-quality carbon fiber may not meet your performance needs. On the other hand, overpaying for features you don’t need can strain your budget. Focus on finding a material that offers the best mix of performance and cost for your specific application.
By considering these factors, you can make an informed decision that aligns with your project’s goals and financial constraints. Whether you’re designing a high-tech drone or a durable piece of sports equipment, understanding your needs and priorities will help you get the most out of carbon fiber.
Comparing Carbon Fiber Products for Cost-Effectiveness
When it comes to finding the most suitable carbon fiber product for your project, understanding the differences between manufacturing methods and product types is essential. Let’s explore some key comparisons to help you make a cost-effective choice.
Prepreg vs. Wet Layup Carbon Fiber
Advantages and Disadvantages of Prepreg
Prepreg carbon fiber comes pre-impregnated with resin, making it a popular option for high-performance applications. Its main advantage lies in its consistent quality. The resin distribution is uniform, which ensures predictable strength and stiffness. Prepreg also reduces waste since the resin content is precisely controlled. This makes it ideal for aerospace, automotive, and other industries where precision matters.
However, prepreg requires specialized storage and handling. You need to keep it refrigerated to prevent the resin from curing prematurely. It also demands curing in an autoclave or oven, which adds to the cost. If your project doesn’t require such high precision, this might not be the most budget-friendly option.
Advantages and Disadvantages of Wet Layup
Wet layup carbon fiber involves manually applying resin to dry carbon fiber fabric. This method is more accessible and cost-effective for smaller projects or prototypes. It doesn’t require expensive equipment, making it a great choice for DIY enthusiasts or low-budget applications.
On the downside, wet layup can result in inconsistent resin distribution. This affects the overall strength and stiffness of the final product. Additionally, the process can be messy and time-consuming. If you prioritize affordability over precision, wet layup might work for you. However, for critical applications, its limitations could be a concern.
Carbon Fiber Tubes and Roll-Wrapped Tubes
Benefits of Carbon Fiber Tubes for Structural Applications
Carbon fiber tubes are widely used in structural applications due to their exceptional strength-to-weight ratio. They provide rigidity and durability, making them perfect for load-bearing components in aerospace, robotics, and automotive industries. These tubes resist bending and deformation, ensuring long-term reliability.
Advantages of Roll-Wrapped Tubes in Terms of Strength and Cost
Among the various types of carbon fiber tubes, carbon fiber roll-wrapped tubes stand out for their versatility. These tubes are manufactured by wrapping layers of carbon fiber fabric around a mandrel, which creates a strong and stiff structure. They perform exceptionally well under multidirectional forces, making them the best carbon fiber tube for demanding applications.
Compared to carbon fiber pultruded tubes, roll-wrapped tubes offer better all-around performance. Pultruded tubes are only strong in one direction, which limits their use in projects requiring multidirectional strength. While roll-wrapped tubes are slightly more complex to produce, they remain a cost-effective choice due to their superior strength and durability. Pultruded tubes, on the other hand, are more expensive to manufacture and less versatile.
Evaluating Suppliers and Manufacturers
Reputation and Reviews
When choosing the right tube or any carbon fiber product, always research the supplier’s reputation. Look for reviews from previous customers to gauge their reliability. A supplier with positive feedback often delivers consistent quality and dependable service. Avoid manufacturers with frequent complaints about defects or delays.
Certifications and Quality Standards
Certifications play a crucial role in ensuring you get the best carbon fiber tube for your needs. Reputable manufacturers adhere to industry standards, such as ISO certifications, which guarantee the quality of their products. Always verify that the supplier meets these standards before making a purchase. This step helps you avoid low-quality materials that could compromise your project.
By comparing these options and evaluating suppliers carefully, you can confidently select the right carbon fiber product for your application. Whether you need carbon fiber roll-wrapped tubes for structural strength or a budget-friendly wet layup solution, understanding these differences ensures you make an informed decision.
Tips for Balancing Performance and Budget
Balancing performance and budget can feel like a juggling act, but with the right approach, you can make smart decisions that meet the unique needs of your project. Let’s explore how you can prioritize effectively, consider alternatives, and plan for long-term success.
Prioritize Your Needs
When selecting carbon fiber, it’s essential to focus on what truly matters for your project. Identifying your priorities helps you avoid unnecessary expenses and ensures you choose the best material for your needs.
Identify Must-Have Features
Start by listing the critical features your project requires. Do you need exceptional strength, lightweight composites, or high durability? For example, if your project involves structural components, prioritize strength and stiffness. On the other hand, recreational applications may benefit more from flexibility and affordability. By narrowing down your must-haves, you can focus on materials that align with your goals.
Avoid Overpaying for Unnecessary Specifications
It’s easy to get drawn into premium options with features you don’t actually need. High modulus carbon fiber, for instance, offers top-tier performance but may be overkill for non-critical applications. Instead, consider whether standard or intermediate modulus carbon fiber can meet your requirements without inflating costs. This approach ensures you’re not paying for features that won’t add value to your project.
Explore Alternatives
Sometimes, the best way to balance performance and budget is by thinking outside the box. Exploring alternative materials or combinations can help you achieve your goals without overspending.
Consider Hybrid Materials (e.g., Carbon Fiber Composites)
Hybrid materials, such as carbon fiber composites, combine carbon fiber with other materials like glass fiber or resin. These composites offer a balance of strength, stiffness, and cost-effectiveness. For example, using a carbon fiber composite with a carefully chosen resin can simplify your design, reduce costs, and expand the range of applications. This makes it an ideal material option for projects where both performance and affordability matter.
Compare Carbon Fiber with Glass Fiber for Cost-Effectiveness
Glass fiber is another alternative worth considering. While it doesn’t match carbon fiber in terms of strength-to-weight ratio, it’s significantly more affordable. For projects where extreme strength isn’t a priority, glass fiber can be a practical substitute. Comparing these materials side by side helps you determine which one aligns better with the unique needs of your project.
Plan for Long-Term Use
Thinking beyond the immediate costs can save you money and headaches down the road. Investing in quality materials and considering the total cost of ownership ensures your project delivers value over time.
Invest in Durability for High-Stress Applications
If your project involves high-stress environments, durability should be a top priority. Carbon fiber’s resistance to wear, fatigue, and harsh conditions makes it a reliable choice for demanding applications. For example, aerospace and automotive industries often invest in higher-quality carbon fiber to ensure long-term performance and safety. Spending a bit more upfront can prevent costly repairs or replacements later.
Calculate Total Cost of Ownership
The initial price tag isn’t the only cost to consider. Factor in maintenance, lifespan, and potential replacements when evaluating materials. While carbon fiber may seem expensive at first, its long-lasting nature often makes it more cost-effective over time. By calculating the total cost of ownership, you can make a more informed decision that balances short-term savings with long-term value.
By prioritizing your needs, exploring alternatives, and planning for the future, you can strike the perfect balance between performance and budget. Whether you’re working on lightweight composites or a high-performance structure, these tips will help you choose the best material for your needs without overspending.
Common Mistakes to Avoid When Buying Carbon Fiber
When buying carbon fiber, it’s easy to make mistakes that can cost you time, money, and even the success of your project. Let’s look at some common pitfalls and how you can avoid them.
Overlooking Application Requirements
Buying the Wrong Type of Carbon Fiber for the Job
One of the biggest mistakes is choosing the wrong type of carbon fiber for your project. Each type has unique properties, and not all of them will suit your needs. For example, using standard modulus carbon fiber for a high-performance aerospace component could lead to failure because it lacks the stiffness required for such applications. On the other hand, opting for high modulus carbon fiber for a recreational product like a fishing rod might be overkill and unnecessarily expensive.
To avoid this, always match the carbon fiber type to your project’s specific requirements. Ask yourself: Does the project need more strength, stiffness, or flexibility? If you’re unsure, consult an expert or do thorough research. Remember, the right choice ensures both performance and cost-effectiveness.
Focusing Solely on Price
Ignoring Quality and Performance Trade-Offs
It’s tempting to go for the cheapest option, but focusing only on price can backfire. Low-cost carbon fiber often compromises on quality, which can lead to poor performance or even material failure. Imagine investing in a carbon fiber part that cracks under stress because it wasn’t built to handle the load. That’s not just frustrating—it’s costly.
Instead of chasing the lowest price, consider the long-term value. High-quality carbon fiber may cost more upfront, but it often lasts longer and performs better. Think about the total cost of ownership, including maintenance and replacement expenses. Balancing quality with affordability ensures you get the best value for your money.
Neglecting Supplier Research
Choosing Unreliable or Uncertified Manufacturers
Not all suppliers are created equal. Some may cut corners, offering subpar carbon fiber that doesn’t meet industry standards. Others might have hidden fees or unreliable delivery times. Choosing the wrong supplier can delay your project or result in materials that fail to perform as expected.
To avoid this, always research suppliers thoroughly. Look for reviews and testimonials from other customers. A reputable supplier will have positive feedback and a track record of delivering high-quality products. Also, check for certifications like ISO standards, which indicate that the manufacturer adheres to strict quality controls. Reliable suppliers not only provide better materials but also offer peace of mind.
“Some things to help guide you along when looking for carbon fiber products include comparing prices from different suppliers, considering any extra costs, determining the budget, considering the lead time, and checking the reputation of the supplier.”
By keeping these mistakes in mind, you can make smarter decisions when buying carbon fiber. Whether you’re working on a structural application or a recreational product, avoiding these pitfalls ensures your project stays on track and within budget.
Real-World Examples of Cost-Effective Carbon Fiber Use
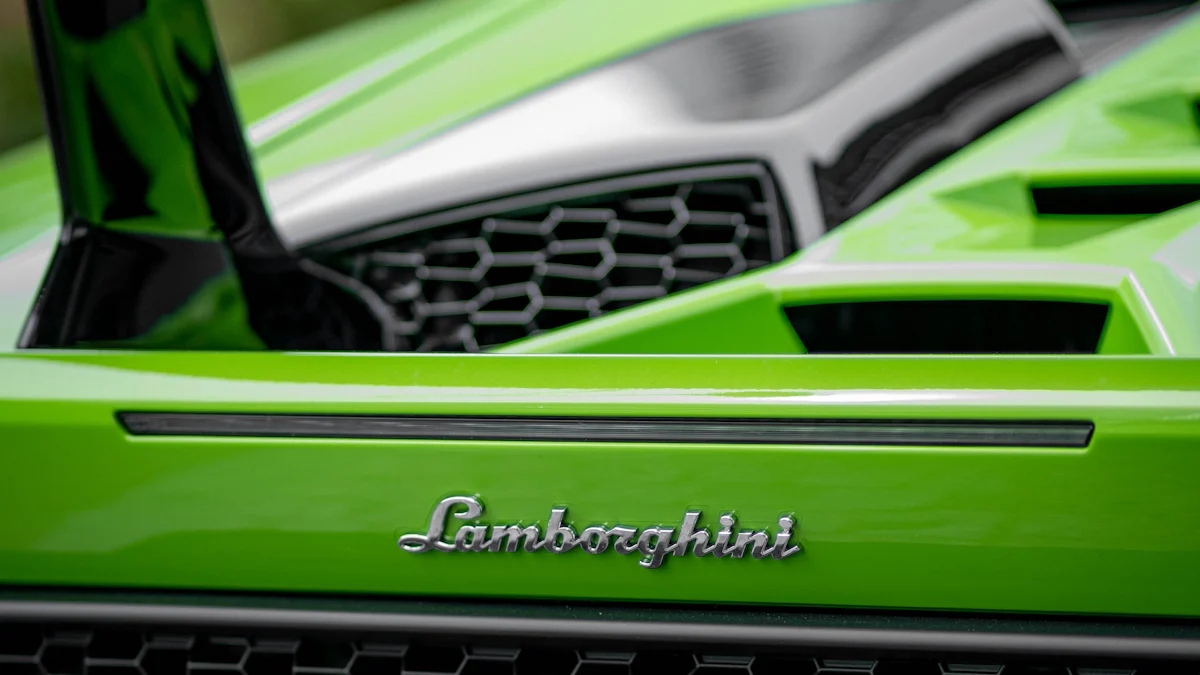
Carbon fiber has transformed industries by offering unmatched strength, lightness, and durability. Let’s explore how it’s being used in real-world scenarios to achieve cost-effective solutions.
Case Study: Automotive Industry
Lightweighting for Fuel Efficiency
In the automotive world, reducing weight is a top priority. Lighter vehicles consume less fuel, which improves efficiency and lowers emissions. Carbon fiber plays a crucial role here. For example, Formula 1 cars rely heavily on carbon fiber for their chassis and body panels. This material not only enhances speed but also ensures safety by absorbing impact during crashes.
Luxury car manufacturers like BMW have also embraced carbon fiber. The BMW i3, an electric vehicle, uses a carbon fiber-reinforced plastic (CFRP) body. This innovation reduces weight significantly without compromising strength. By integrating carbon fiber into structural components, automakers achieve better performance while meeting environmental standards. If you’re in the automotive sector, using carbon fiber can help you strike the perfect balance between efficiency and durability.
Case Study: Sports Equipment
Balancing Performance with Affordability
Sports enthusiasts demand equipment that performs well and lasts long. Carbon fiber has become a go-to material for products like bicycles, tennis rackets, and fishing rods. Its lightweight nature enhances usability, while its strength ensures durability during intense use.
Take bicycles, for instance. High-performance models often feature carbon fiber frames. These frames are not only lighter than aluminum or steel but also absorb vibrations better, providing a smoother ride. Brands like Trek and Specialized offer carbon fiber bikes that cater to both professional athletes and recreational riders. By choosing standard or intermediate modulus carbon fiber, manufacturers keep costs manageable while delivering top-notch performance.
In tennis, carbon fiber rackets offer players better control and power. The material’s flexibility allows for precise engineering, giving athletes an edge on the court. Whether you’re designing sports gear or shopping for it, carbon fiber ensures you don’t have to compromise on quality or affordability.
Case Study: Aerospace Applications
High-Performance Materials for Critical Components
The aerospace industry demands materials that can withstand extreme conditions while remaining lightweight. Carbon fiber meets these requirements perfectly. Aircraft manufacturers use it extensively in wings, fuselages, and other critical components. Its high strength-to-weight ratio improves fuel efficiency and reduces maintenance costs.
For example, Boeing’s 787 Dreamliner incorporates carbon fiber composites in its structure. This design choice reduces the aircraft’s weight by up to 20% compared to traditional materials. The result? Lower fuel consumption and extended range. In space exploration, carbon fiber is equally vital. Satellites and spacecraft rely on it for its ability to endure harsh environments without adding unnecessary weight.
If you’re working on aerospace projects, carbon fiber offers unparalleled performance. While the initial investment may seem high, the long-term benefits make it a cost-effective choice for critical applications.
The Role of Carbon Fiber Prototyping in Cost-Effective Design
Prototyping plays a crucial role in turning ideas into reality, especially when working with advanced materials like carbon fiber. By using carbon fiber prototyping, you can test designs, refine performance, and reduce waste, all while keeping costs under control. Let’s explore why this approach is so effective and how it’s applied in real-world scenarios.
Benefits of Prototyping with Carbon Fiber
Testing Designs for Performance and Durability
Prototyping with carbon fiber allows you to evaluate how your design performs under real-world conditions. Carbon fiber’s unique properties, such as its high strength-to-weight ratio and resistance to wear, make it an excellent choice for testing. For example, if you’re developing a lightweight drone or a high-performance bike frame, prototyping helps you identify weak points and optimize the structure before full-scale production. This process ensures your final product meets both performance and durability standards.
“Carbon fiber is 5 times lighter and 10 times stronger than steel, making it ideal for applications requiring strength and lightness.” – BMF Motorsports
By testing early, you can avoid costly mistakes and ensure your design is ready for demanding environments. Whether it’s aerospace components or sports equipment, prototyping gives you the confidence to move forward with a reliable design.
Reducing Waste and Optimizing Material Use
Carbon fiber part prototyping also helps you minimize material waste. Since carbon fiber can be molded into complex shapes, you can create precise prototypes that use only the necessary amount of material. This precision not only saves resources but also reduces production costs. For instance, in industries like automotive or robotics, where every gram matters, prototyping ensures you’re using carbon fiber efficiently without compromising on quality.
Additionally, prototyping allows you to experiment with different configurations and resin combinations. By doing so, you can find the perfect balance between performance and cost-effectiveness. This step is especially valuable when working with expensive materials like carbon fiber, as it ensures every dollar spent contributes to the success of your project.
Examples of Prototyping Applications
Product Development in Aerospace and Automotive Industries
Aerospace and automotive industries rely heavily on carbon fiber part prototyping to push the boundaries of innovation. In aerospace, prototypes help engineers test components like wings or fuselages for strength and weight reduction. Carbon fiber’s ability to withstand extreme conditions makes it indispensable for these applications. For example, aircraft manufacturers use prototypes to ensure their designs meet safety and performance standards before mass production.
In the automotive sector, prototyping enables the creation of lightweight yet durable parts. From chassis components to body panels, carbon fiber prototypes allow automakers to refine designs for better fuel efficiency and handling. By testing these prototypes, manufacturers can achieve the perfect balance between performance and cost, ensuring their vehicles meet consumer expectations.
Custom Sports Equipment Design
Sports equipment manufacturers also benefit from carbon fiber prototyping. Whether it’s a tennis racket, a bicycle frame, or a fishing rod, prototyping helps designers fine-tune their products for maximum performance. For instance, a prototype bike frame made from carbon fiber can be tested for stiffness, weight distribution, and vibration absorption. This process ensures the final product delivers a smooth and efficient ride.
Custom sports equipment often requires unique designs tailored to specific needs. Prototyping allows you to experiment with different shapes and configurations, ensuring the final product meets the athlete’s requirements. By using carbon fiber part prototyping, manufacturers can create high-performance gear that stands out in the market.
“Carbon fiber composites offer advantages in stiffness, strength, and customization, making them ideal for sports equipment and other specialized applications.” – Element 6 Composites
Prototyping with carbon fiber not only enhances the design process but also ensures you get the most out of this versatile material. Whether you’re working on aerospace innovations or custom sports gear, this approach helps you achieve cost-effective solutions without compromising on quality.
Choosing the right carbon fiber requires understanding its types, characteristics, and cost factors. By focusing on your project’s needs, you can balance performance with budget constraints. Start by assessing what your application demands—strength, lightness, or durability. Research available products and compare options to find the best fit. Always prioritize quality and long-term value over short-term savings. Whether you’re designing for aerospace, sports, or industrial use, making informed decisions ensures your investment pays off in performance and reliability.
FAQ
What is carbon fiber?
Carbon fiber is a fabric mat made of woven fibers. It’s classified as both a composite and a fiber-reinforced plastic. The material consists of 90% polyacrylonitrile (a carbon precursor) and 10% other precursors like pitch or cellulose. Manufacturers create it through processes like carbonization, oxidation, or graphitization. After cutting it into the desired shape, they impregnate it with resin and cure it. The result is a lightweight yet incredibly strong material with an impressive strength-to-weight ratio.
Why is carbon fiber so expensive?
Carbon fiber’s cost comes from its complex manufacturing process and high-quality raw materials. Producing carbon fiber involves multiple steps, including heating, stretching, and curing, all of which require precision and specialized equipment. Additionally, the demand for its unique properties—like strength, lightness, and durability—drives up its price. While it’s costly upfront, its long-term benefits often outweigh the initial expense.
How do I choose the right type of carbon fiber for my project?
Start by identifying your project’s needs. Do you need more strength, stiffness, or flexibility? For general-purpose applications, standard modulus carbon fiber works well. If you need higher performance, intermediate or high modulus options might be better. Consider factors like weight, durability, and budget. Matching the carbon fiber type to your specific requirements ensures the best results.
Can I use carbon fiber for DIY projects?
Yes, you can use carbon fiber for DIY projects. Wet layup carbon fiber is a popular choice for beginners because it doesn’t require expensive equipment. You’ll need basic tools, resin, and carbon fiber fabric to get started. However, keep in mind that working with carbon fiber requires attention to detail and safety precautions, such as wearing gloves and a mask to avoid exposure to resin fumes.
What are the main advantages of carbon fiber?
Carbon fiber offers several key advantages:
Lightweight: It’s much lighter than materials like steel or aluminum.
High strength-to-weight ratio: It’s incredibly strong for its weight.
Durability: It resists wear, fatigue, and harsh environmental conditions.
Thermal and chemical resistance: It performs well in extreme temperatures and resists corrosion.
These properties make it ideal for industries like aerospace, automotive, and sports equipment.
Is carbon fiber environmentally friendly?
Carbon fiber production has a significant environmental impact due to energy-intensive manufacturing processes. However, its long lifespan and ability to reduce weight in vehicles (leading to lower fuel consumption) can offset some of its environmental costs. Researchers are also exploring recycling methods to make carbon fiber more sustainable in the future.
How does carbon fiber compare to glass fiber?
Carbon fiber is stronger and lighter than glass fiber, making it better for high-performance applications. However, glass fiber is more affordable and works well for projects where extreme strength isn’t necessary. If cost is a concern, glass fiber might be a practical alternative. For critical applications requiring superior performance, carbon fiber is the better choice.
Can carbon fiber be repaired if damaged?
Yes, you can repair carbon fiber, but the process requires expertise. Small cracks or surface damage can often be fixed with resin and patches. For structural damage, professional repair is usually necessary to restore strength and integrity. Always assess the extent of the damage before deciding on a repair method.
What industries benefit the most from carbon fiber?
Several industries rely heavily on carbon fiber:
Aerospace: For lightweight and durable components like wings and fuselages.
Automotive: To improve fuel efficiency and performance in vehicles.
Sports equipment: For lightweight and high-performance gear like bicycles and tennis rackets.
Industrial applications: In robotics and manufacturing for its strength and resistance to wear.
Its versatility makes it valuable across a wide range of fields.
How do I maintain carbon fiber products?
Maintaining carbon fiber products is simple. Clean them with mild soap and water to remove dirt and debris. Avoid using abrasive cleaners or tools that could scratch the surface. Inspect regularly for signs of damage, especially if the product is used in high-stress environments. Proper care ensures your carbon fiber items last longer and perform at their best.